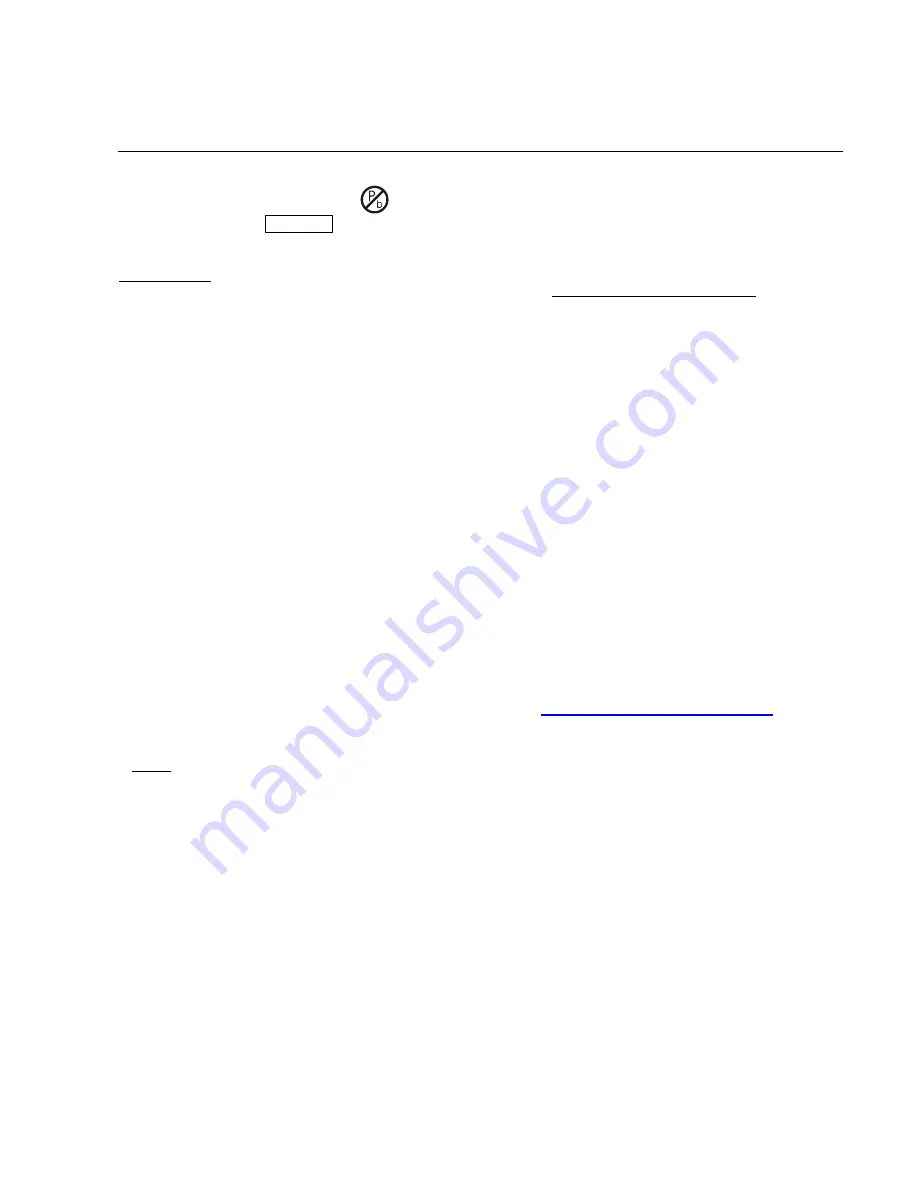
Lead-Free requirement for service
INDENTIFICATION:
Regardless of special logo (not always indicated)
One must treat all sets from
1.1.2005
onwards, according next
rules.
Important note: In fact also products a little older can
also be treated in this way as long as you avoid mixing
solder-alloys (leaded/ lead-free). So best to always
use SAC305 and the higher temperatures belong to
this
.
Due to lead-free technology some rules have to be respected by the
workshop during a repair:
•
Use only lead-free solder alloy Philips SAC305 with
order code 0622 149 00106. If lead-free
solder-paste is required, please contact the
manufacturer of your solder-equipment. In general
use of solder-paste within workshops should be
avoided because paste is not easy to store and to
handle.
•
Use only adequate solder tools applicable for
lead-free solder alloy. The solder tool must be able
o
To reach at least a solder-temperature of
400°C,
o
To stabilize the adjusted temperature at the
solder-tip
o
To exchange solder-tips for different
applications.
•
Adjust your solder tool so that a temperature around
360°C – 380°C is reached and stabilized at the
solder joint. Heating-time of the solder-joint should
not exceed ~ 4 sec. Avoid temperatures above
400°C otherwise wear-out of tips will rise drastically
and flux-fluid will be destroyed. To avoid wear-out of
tips switch off un-used equipment, or reduce heat.
•
Mix of lead-free solder alloy / parts with leaded
solder alloy / parts is possible but PHILIPS
recommends strongly to avoid mixed
solder alloy types (leaded and lead-free). If one
cannot avoid, clean carefully the
solder-joint from old solder alloy and re-solder with
new solder alloy (SAC305).
•
Use only original spare-parts listed in the
Service-Manuals. Not listed standard-material
(commodities) has to be purchased at
external companies.
•
Special information for BGA-ICs:
- always use the 12nc-recognizable soldering
temperature profile of the specific BGA (for
de-soldering always use highest lead-free
temperature profile, in case of doubt)
- lead free BGA-ICs will be delivered in
so-called ‘dry-packaging’ (sealed pack
including a silica gel pack) to protect the IC
against moisture. After opening, dependent of
MSL-level seen on indicator-label in the bag,
the BGA-IC possibly still has to be baked dry.
This will be communicated via AYS-website.
Do not re-use BGAs at all.
•
For sets produced before 1.1.2005, containing
leaded soldering-tin and components, all
needed spare-parts will be available till the
end of the service-period. For repair of such
sets nothing changes.
•
On our website:
www.atyourservice.ce.Philips.com
You find more information to:
BGA-de-/soldering (+ baking instructions)
Heating-profiles of BGAs and other ICs used
in Philips-sets
You will find this and more technical
information within the “magazine”, chapter
“workshop news”.
For additional questions please contact your local
repair-helpdesk.
Warnings,
Notes
1-5
Summary of Contents for SDV434/19
Page 23: ...Service Engineer Remarks 6 2 ...
Page 25: ...6 4 6 4 Front Board Top Side Front Board Bottom side ...
Page 29: ...7 3 7 3 Power Board Top Side ...
Page 36: ...8 6 8 6 Mpeg Board Top Side ...
Page 37: ...8 7 8 7 Mpeg Board Bottom Side ...
Page 42: ...Mechanical Exploded view 9 1 ...
Page 44: ...REVISION LIST Version 1 0 Initial release 10 1 ...