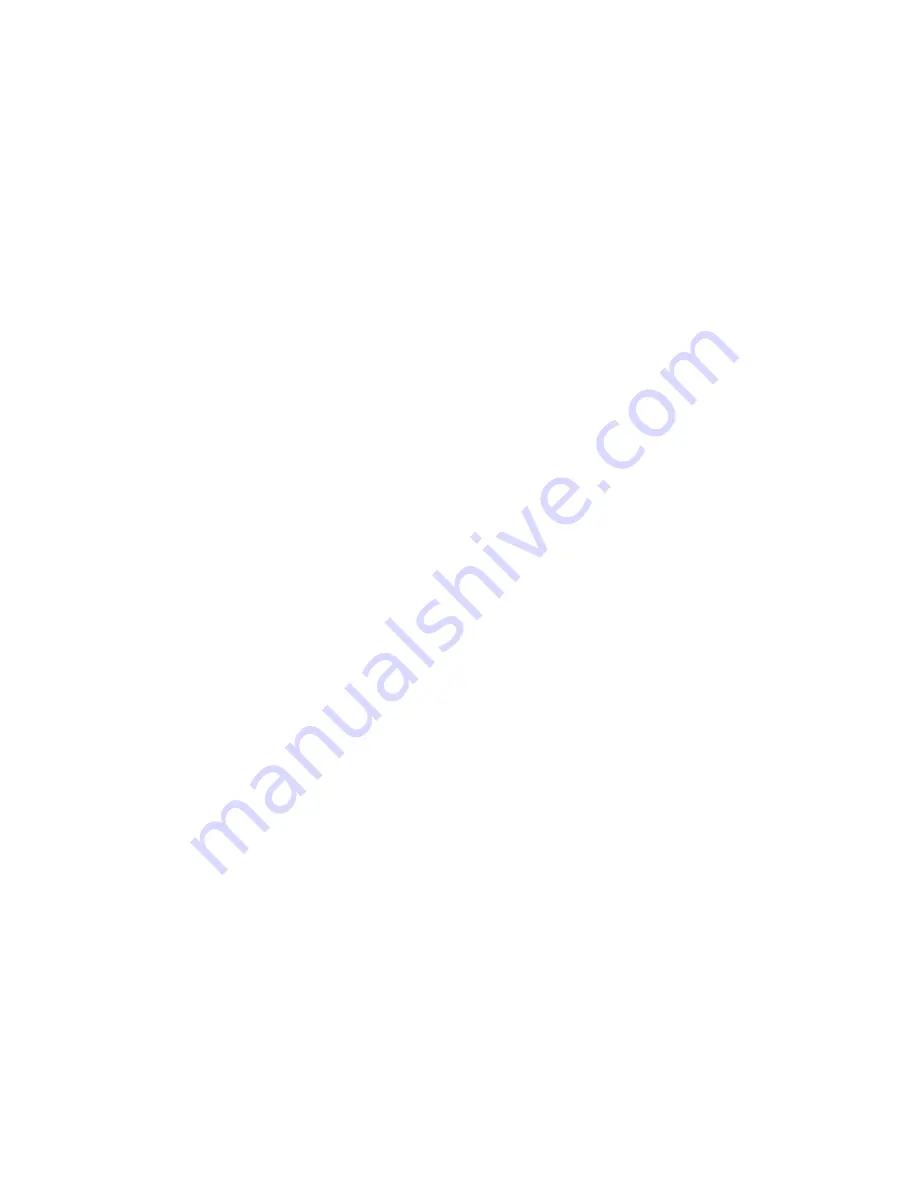
MAIN POWER SUPPLY (Figure 24)
Power is applied to the Main Power supply when the set is turned On. The RAW-DC is
switched to the Main Power supply located on the Main Power supply board. Voltage is
applied to the Primary winding of 5310 via Pins 5 and 3. Voltage is then applied to Pin 7 of
7302. In the Startup mode, voltage from the internal current limiting resistor Rs is routed to
Pin 1 where it charges Capacitor 2344. When the charge on Capacitor 2344 reaches 5.8
volts, Pin 1 is switched to the Internal Supply connection. The Oscillator and PWM drive are
switched On to drive 5310. IC 7302 will continue to drive the Transformer, 5310, until the
charge on 2344 drops below 4.8 volts. The Startup cycles will continue until the secondary
reference voltage, the 9 volts supply, reaches the correct level. When the 9-volt supply
reaches the correct level, 2.5 volts will be applied to the input of Shunt Regulator 7306.
Shunt Regulator 7306 will then turn On causing current to flow through the LED in
Optoisolator 6307. This will turn the transistor inside 6307 to turn On. Voltage from Pins 1
and 2 of the Hot secondary is rectified by 6305 and filtered by 2341. Optoisolator 6307
switches this voltage to Pin 1 of 7302 to provide the operating voltage for the IC.
The secondary pr36, +12, +9, and +22 volt supplies. Shunt Regulator 7304 and
FET 7303 regulate the +12 volt supply.
The PWR_FAIL Main Power Fail detection circuit signals the Microprocessor when power is
about to be lost to the set while it is On. Voltage from Pin 9 of 5310 is rectified by 6309 to
produce a negative voltage, which is filtered by Capacitor 2365. This voltage along with the
+9 volt supply is applied to the input of Shunt regulator 7309 via resistor network of 3354,
3355, and 3353. As long as the negative voltage is present on 2365, the voltage on the input
of 7309 will be less than the 2.5 volts necessary to turn it On. Transistor 7310 will be turned
Off, keeping the PWR_FAIL line Low. When the switched mode supply ceases operation,
Capacitor 2365 will discharge quickly, due to its low value, allowing the voltage on the input of
7309 to increase to 2.5 volts. Shunt Regulator 7309 will turn On, turning transistor 7310 On,
causing the PWR_FAIL line to go High. This will signal the Microprocessor to shut everything
down before the main supply voltage drops.
Regulation of the secondary is accomplished by monitoring the reference voltage, the +9 volt
supply, to control the On time of the internal FET of 7302. If the +9 volt supply increases,
Shunt Regulator 7306 will conduct harder increasing the amount of current through 6307.
This will cause the LED to increase in brightness, reducing the internal resistance of the tran-
sistor inside the IC. The increase in current will cause the voltage across the internal sensing
resistor Re inside 7302 to increase. The PWM will then reduce the On time of the internal
FET, decreasing the secondary voltage. If the +9 volt supply should decrease, 7306 will con-
duct less, the transistor inside 6307 will conduct less, causing less current to flow through the
sensing resistor Re. The PWM will sense the lower voltage across Re, increasing the On
time of the internal FET to increase the secondary voltage.
Page 14
Summary of Contents for EM7U LCOS
Page 2: ......
Page 12: ...POWER INPUT BOARD MAIN POWER BOARD POWER BOARD SERVICE POSITION Page 9 ...
Page 13: ...Page 10 FIGURE 21 POWER SUPPLY BLOCK ...
Page 14: ...Page 11 FIGURE 22 AC INPUT CIRCUIT ...
Page 16: ...Page 13 FIGURE 23 STANDBY SUPPLY ...
Page 18: ...Page 15 FIGURE 24 MAIN POWER SUPPLY ...
Page 20: ...Page 17 FIGURE 25 3 3 VOLT REGULATOR ...
Page 22: ...Page 19 FIGURE 26 AUDIO POWER SUPPLY OPERATING VOLTAGE FOR THE LAMP SUPPLY REGULATOR ...
Page 24: ...Page 21 FIGURE 27 LAMP SUPPLY ...
Page 27: ...Page 24 FIGURE 29 OVER BLOCK 1FH SECTION ...
Page 34: ...Page 31 FIGURE 35 HIP CIRCUIT ...
Page 36: ...Page 33 FIGURE 36 NTSC COMB FILTER CIRCUIT ...
Page 38: ...Page 35 FIGURE 37 PIP DOUBLE WINDOW INPUT ...
Page 39: ...Page 36 FIGURE 38 PIP DOUBLE WINDOW OUTPUT ...
Page 40: ...Page 37 FIGURE 39 DOUBLE WINDOW CONTROL AND POWER SUPPLY ...
Page 42: ...Page 39 FIGURE 40 FEATURE BOX NOT USED ...
Page 44: ...Page 41 FIGURE 41 EAGLE ...
Page 47: ...Page 44 FIGURE 43 2FH SECTION BLOCK ...
Page 49: ...Page 46 FIGURE 44 VGA INPUT ...
Page 51: ...Page 48 FIGURE 45 AV3 AND AV4 ...
Page 54: ...Page 51 FIGURE 47 DVI INPUT ...
Page 57: ...Page 54 FIGURE 49 SCALER ...
Page 59: ...Page 56 FIGURE 50 OSD AND OUTPUT ...
Page 60: ...Page 57 FIGURE 51 OTC OSD ...
Page 61: ...Page 58 FIGURE 52 OSD SCALER INPUT ...
Page 63: ...Page 60 FIGURE 53 REFERENCE VOLTAGE AND A D CONVERTER ...
Page 64: ...Page 61 FIGURE 54 INPUT LATCH AND PLD SYNC ...
Page 65: ...Page 62 FIGURE 55 ADC CLOCK CIRCUIT ...
Page 67: ...FIGURE 56 TMDS TRANSMITTER Page 64 ...
Page 68: ...Page 65 FIGURE 57 MSB CLOCK AND SYNC ...
Page 69: ...Page 66 FIGURE 58 LIGHT ENGINE BLOCK ...
Page 71: ...Page 68 FIGURE 59 AUDIO SIGNAL FLOW BLOCK ...
Page 73: ...Page 70 FIGURE 60 SSB AUDIO PROCESSING ...
Page 75: ...Page 72 FIGURE 61 AUDIO SIGNAL DELAY ...
Page 78: ...Page 75 FIGURE 63 AUDIO POWER AMPLIFIER ...
Page 80: ...Page 77 FIGURE 65 AUDIO PROTECTION CIRCUIT ...
Page 84: ...Page 81 FIGURE 68 OTC COMMUNICATION ...
Page 87: ...Page 84 FIGURE 72 I 2 C INTERCONNECT PART ONE ...
Page 89: ...Page 86 FIGURE 74 I 2 C INTERCONNECT PART THREE ...
Page 92: ...Page 89 FIGURE 77 FAN DRIVE CIRCUIT ...
Page 93: ...Page 90 FIGURE 78 FAN FAILURE DETECTION CIRCUIT ...
Page 94: ...Page 91 FIGURE 79 WIRING INTERCONNECT PART 1 ...
Page 95: ...Page 92 FIGURE 80 WIRING INTERCONNECT PART 2 ...
Page 96: ...Page 93 FIGURE 81 WIRING INTERCONNECT PART 3 ...
Page 100: ...THEN SLIDE THE PACKAGE OUT OF THE SET POWER INPUT BOARD IN A SERVICE POSITION Page 97 ...
Page 102: ...PIP DW COMB FILTER SYSTEM BOARD SMALL SIGNAL BOARD SSB JACK PANEL SCALER BOARD MSB Page 99 ...
Page 103: ......
Page 104: ...MICKIE MARTIN 05 05 03 ...