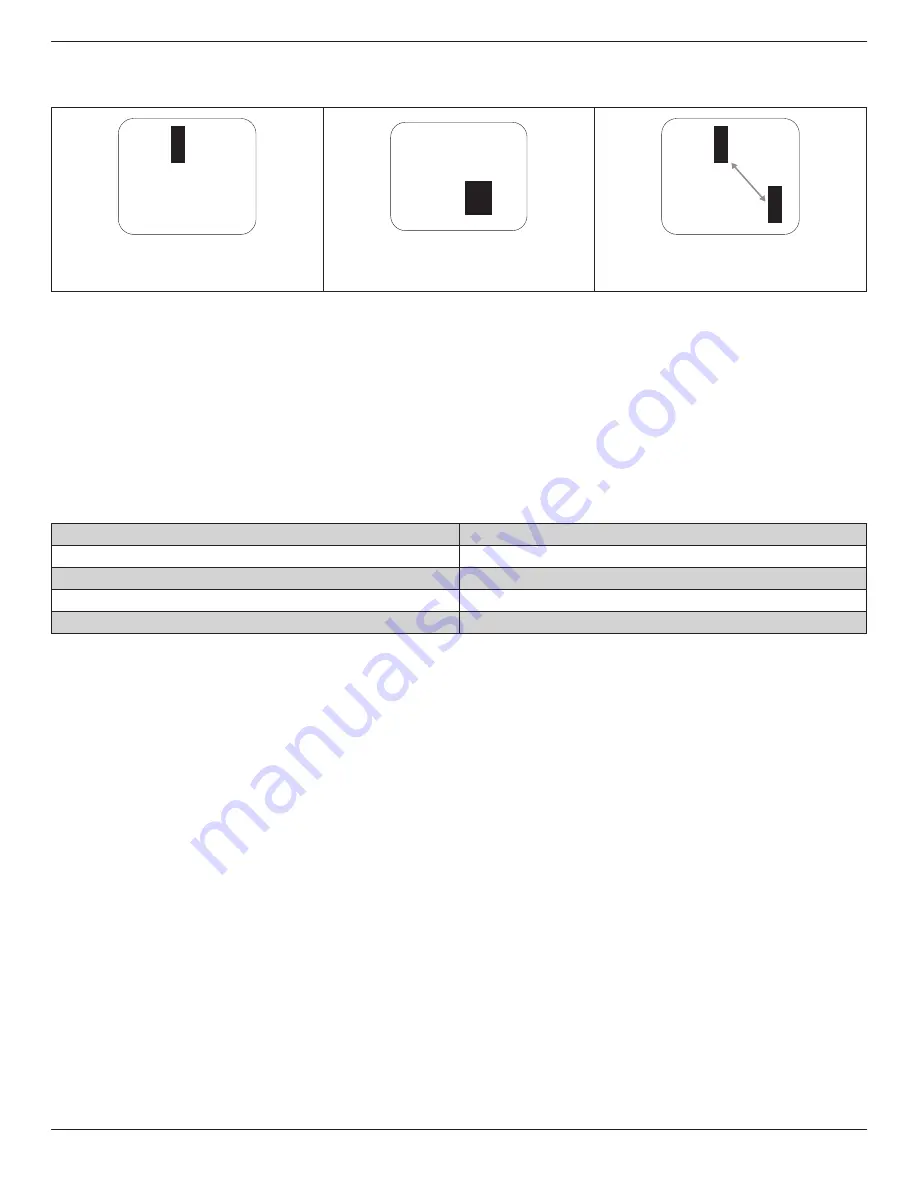
BDL3245E / BDL4245E / BDL4645E
25
6.4. Dark Dot Defects
Black dot defects appear as pixels or sub-pixels that are always dark or “off”. These are the examples of black dot defects:
One dark dot
Two adjacent dark dots = 1 pair of dark dots
Two dark dots, specifications defines the
minimum distance between dark dots
6.5. Proximity of Pixel Defects
Because pixel and sub-pixels defects of the same type that are nearby one another may be more noticeable, Philips also specifies tolerances for the
proximity of pixel defects. In the table below you can find specifications about:
•
Allowed amount of adjacent dark dots = (adjacent dark dots =1 pair of dark dots)
•
Minimum distance between dark dots
•
Total no. of all defective dots
6.6. Pixel Defect Tolerances
In order to qualify for repair due to pixel defects during the warranty period, a PDP / TFT panel in a Philips Plasma / LCD- display must have pixel or sub-
pixel defects exceeding the tolerances listed in the following table.
BRIGHT DOT EFFECT
ACCEPTABLE LEVEL
1 lit sub pixel
2
BLACK DOT EFFECT
ACCEPTABLE LEVEL
1 dark sub pixel
10
TOTAL DOT DEFECTS OF ALL TYPES
12
NOTE: * 1 or 2 adjacent sub pixel defects = 1 dot defect
6.7. MURA
Dark spots or patches may occasionally appear on some liquid crystal display (LCD) panels. This is known within the industry as Mura, which is a Japanese
term for “unevenness.” It is used to describe an irregular pattern or area in which uneven screen uniformity appears under certain conditions. Mura is a
result of the deterioration of the liquid crystal alignment layer and is most commonly caused by long-term operation under high ambient temperatures. It
is an industry- wide phenomenon and Mura is not repairable. It is also not covered by our warranty terms.
Mura has been around since the introduction of LCD technology and with screens getting bigger and in operation 24/7, many displays are running in low
light conditions. This all adds to the possibility of Mura affecting displays.
HOW TO SPOT MURA
There are many symptoms of Mura and also multiple causes. Several of these are listed below:
•
Impurities or foreign particles in the crystal matrix
•
Uneven distribution of LCD matrix during manufacturing
•
Non-uniform luminance distribution of the backlight
•
Panel assembly induced stress
•
Flaws within the LCD cells
•
Thermal induced stress - high temperature operation over long periods of time
HOW TO AVOID MURA
Although we can not guarantee the complete eradication of Mura every time, in general the appearance of Mura can be minimized by these methods:
•
Lower the backlight brightness
•
Use a screen saver
•
Reduce the ambient temperature around the unit