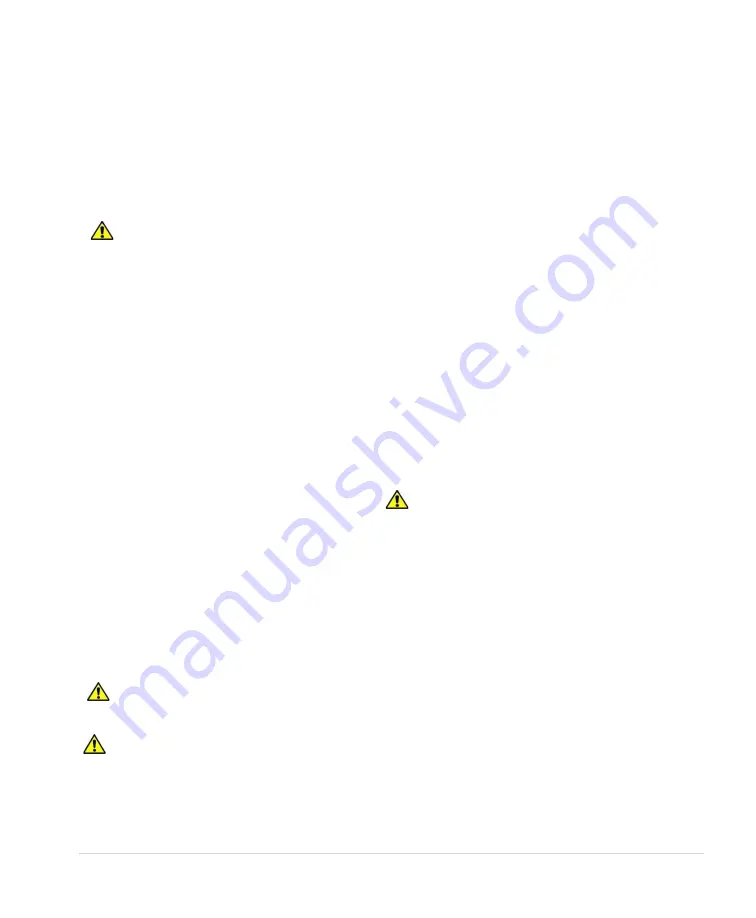
50 |
P a g e
System configuration is set by navigating to the keypad Main Menu item
CHANGE PARAMETER
VALUES > CHANGE INTERFACE PARAMETERS > SYSTEM CONFIG.
Refer to
Section 5.1
Changing Parameter Values,
for detailed instructions. Below is a brief description of each
configuration setting:
•
System Configuration = 0
:
Basic RUN/STOP operation
. This is the factory default configuration for
basic operation of the drive that allows RUN/STOP control of the motor in AUTO mode using a dry
contact on AUX1 and/or AUX2.
CAUTION
:
By default, AUX1 and AUX2 are programmed to be always in RUN mode.
See
parameters
AUX1 SELECT
and
AUX2 SELECT
to change this setting.
System Configuration = 1
:
Analog Constant Pressure
. Use this setting to operate analog constant
pressure systems with a 4-20 mA transducer. Refer to
Section 7.3
Analog Constant Pressure
Systems
, for more information on operating the drive in this mode. Refer to
illustrating connection of the transducer to control terminals. If a redundant analog transducer is used,
connect it to the I_2+ and I_2- terminals in likewise fashion. If the sensor on I_1 fails (current signal is
zero) the drive will look for a signal on I_2 to control pressure. If there is no signal on I_2 the drive will
stop and indicate
SENSOR CONNECTION FAIL
.
System Configuration = 2
:
Speed control with 0-5VDC analog signal.
Use this setting for motor
speed control by a potentiometer connected to the 0-5 VDC control terminals. Refer to
diagram illustrating connection of the potentiometer to control terminals. The drive will ignore the
analog signal until it reaches a value proportional to the speed set by the parameter,
MIN
FREQUENCY
, which has a factory default setting of 30 Hz. For speed control across the full scale
range of the analog signal, set
MIN FREQUENCY
to the minimum value of 5 Hz. AUX1 and AUX2 must
be closed to run in this System Configuration.
CAUTION
:
By default, AUX1 and AUX2 are
programmed to be always ON.
See parameters
AUX1 SELECT
and
AUX2 SELECT
to change this
setting.
System Configuration = 3
:
Speed control with 4-20 mA analog signal
. Use this setting for motor
speed control proportional to a 4-20 mA analog signal. The drive will ignore the analog signal until it
reaches a value proportional to the speed set by the parameter,
MIN FREQUENCY
, which has a factory
default setting of 30 Hz. For speed control across the full-scale range of the analog signal, set
MIN
FREQUENCY
to the minimum value of 5 Hz. Refer to
for a diagram illustrating connection of
the transducer to Control Terminals. When using an active powered 4-20 mA source, connect the leads
to
I_1in+
and COM. AUX1 and AUX2 must be closed to run in this System Configuration.
CAUTION
:
By default, AUX1 and AUX2 are programmed to be always in RUN mode.
See
parameters
AUX1 SELECT
and
AUX2 SELECT
to change this setting.
CAUTION
: This is not a CP control mode. Motor speed will be controlled in a linear fashion
proportional to the analog signal.
The
SYSTEM CONFIG
must be in any of the CP modes to enable Pre-Charge of the plumbing system
or Lead/Lag pump control. See
Section 7.4
Pre-Charge
and
Section 7.5
Lead/Lag Pump
Control
for
more information.
Summary of Contents for 2XD Series
Page 10: ...4 P a g e 2 3 Dimensional Drawings Figure 5 SD Series Line Drawing...
Page 11: ...5 P a g e Figure 6 SD Series Line Drawing if selected with optional breaker see Figure 9...
Page 12: ...6 P a g e Figure 7 SD Series Line Drawing if selected with optional breaker see Figure 9...
Page 14: ...8 P a g e Figure 9 SD Series Line Drawing...
Page 15: ...9 P a g e Figure 10 SD Series Line Drawing...
Page 16: ...10 P a g e Figure 11 2XD Series Line Drawing...