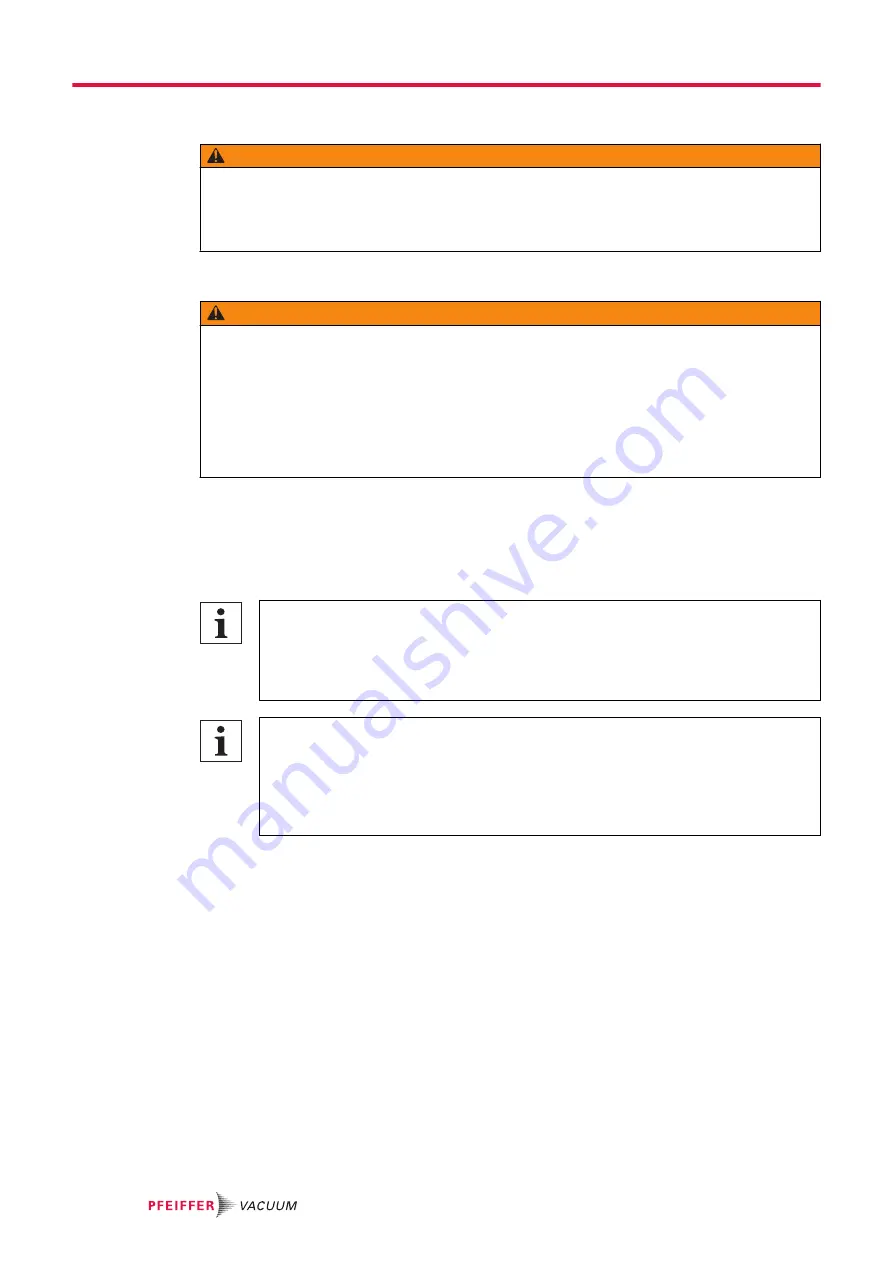
Risks when shipping
WARNING
Risk of poisoning from contaminated products
Where products that contain harmful substances are shipped for maintenance or repair purposes, the
health and safety of service personnel is at risk.
► Comply with the instructions for safe distribution.
Risks during disposal
WARNING
Health hazard through poisoning from toxic contaminated components or devices
Toxic process media result in contamination of devices or parts of them. During maintenance work,
there is a risk to health from contact with these poisonous substances. Illegal disposal of toxic sub-
stances causes environmental damage.
► Take suitable safety precautions and prevent health hazards or environmental pollution by toxic
process media.
► Decontaminate affected parts before carrying out maintenance work.
► Wear protective equipment.
2.3 Safety precautions
The product is designed according to the latest technology and recognized safety engineering rules.
Nevertheless, improper use can result in danger to operator all third party life and limb, and product
damage and additional property damage.
Duty to provide information on potential dangers
The product holder or user is obliged to make all operating personnel aware of dangers
posed by this product.
Every person who is involved in the installation, operation or maintenance of the product
must read, understand and adhere to the safety-related parts of this document.
Infringement of conformity due to modifications to the product
The Declaration of Conformity from the manufacturer is no longer valid if the operator
changes the original product or installs additional equipment.
● Following the installation into a system, the operator is required to check and re-evalu-
ate the conformity of the overall system in the context of the relevant European Direc-
tives, before commissioning that system.
General safety precautions when handling the product
► Observe all applicable safety and accident prevention regulations.
► Check that all safety measures are observed at regular intervals.
► Pass on safety instructions to all other users.
► Do not expose body parts to the vacuum.
► Always ensure a secure connection to the earthed conductor (PE).
► Never disconnect plug connections during operation.
► Observe the above shutdown procedures.
► Keep lines and cables away from hot surfaces (> 70 °C).
► Do not carry out your own conversions or modifications on the device.
► Observe the unit protection degree prior to installation or operation in other environments.
► Provide suitable touch protection, if the surface temperature exceeds 70 °C.
► Inform yourself about any contamination before starting work.
Safety
12/40