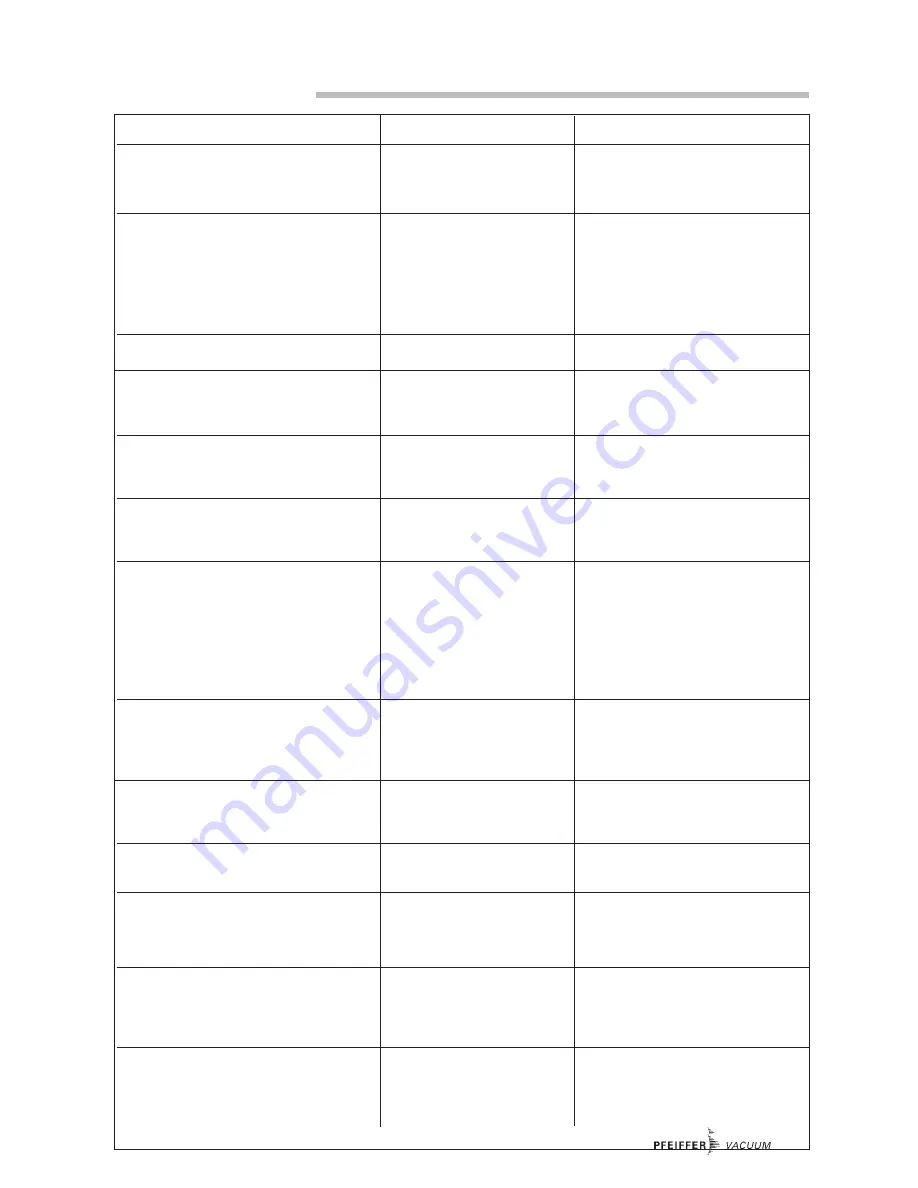
Feature
Unit
TMH 1601 P
TMH 1601 P
TMH 1601 P C H (T)
TMH 1601 P C H (T)
TMU 1601 P
TMU 1601 P
TMU 1601 P C H (T)
TMU 1601 P C H (T)
CCoonnnneeccttiioonn nnoom
miinnaall ddiiaam
meetteerr::
IInnlleett
DDN
N 220000 IISSOO--KK
DDN
N 225500 IISSOO--KK
DDN
N 220000 IISSOO--KK
DDN
N 225500 IISSOO--KKFF
DDN
N 220000 CCFF--FF
DDN
N 225500 CCFF--FF
DDN
N 220000 CCFF--FF
DDN
N 225500 CCFF--FF
OOuuttlleett
DDN
N 4400 IISSOO--KKFF
DDN
N 4400 IISSOO--KKFF
VVeennttiinngg ccoonnnneeccttiioonn
GG 11//88””
GG 11//88””
Nominal rotation speed
Hz (1/min)
600 (36 000)
600 (36 000)
Standby rotation speed
Hz (1/min)
400 (24 000)
400 (24 000)
Start-up time
(up to 90% of the nominal
rotation speed fore-vacuum
pressure
≤
0,1 mbar)
min
6
6
Noise level
dB (A)
47
47
Final pressure, backing pump
mbar
≤
5
≤
2.5
Maximum permissible rotor temperature
°C
120
120
Permissible heat radiation power
W
35
35
Volume flow rate for:
Nitrogen N2
l/s
1000
1400
1000
1400
Helium He
l/s
1100
1200
1100
1210
Hydrogen H2
l/s
750
900
750
900
Compression ratio for:
N2
1011
> 109
He
2 · 107
1 · 105
H2
2 · 105
5 · 103
Maximum fore-vacuum pressure
N2
mbar
14
5
He
mbar
12
4,5
H2
mbar
6
2
Maximum gas throughput1) 2) 3)
with HV pressure of 0.1 mbar
N2
mbarl/s
22
24
Ar
mbarl/s
–––
27
with nominal rotation speed (water cooling)
N2
mbarl/s
12
18
Ar
mbarl/s
7
12
with voltage range 90 - 132 VAC
N2
mbarl/s
9
15
Vertex power characteristics lines4)
A
W / Hz
520 / 600
520 / 600
B
W / Hz
560 / 450
560 / 450
C
W / Hz
480 / 600
480 / 600
D
W / Hz
520 / 348
520 / 348
Final pressure5)
with diaphragm vacuum pump
mbar
< 5 · 10-10
< 1 · 10-8
with rotary vane vacuum pump
mbar
< 5 · 10-10
< 1 · 10-8
with UniDryTM
mbar
< 5 · 10-10
< 1 · 10-8
Lubricant
Type6)
F3
F3
Filling volume
cm3
65
65
Cooling water consumption
with water at 15
Þ
C 7)
l/h
100
100
Cooling water temperature
Þ
C
5 - 25
5 - 25
Permissible ambient temperature
with air cooling
Þ
C
0 - 35
–––
Power consumption:
Casing heating unit
W
170
170
TMS heating
W
–––
1000
Weight
kg
49/51
51/53
49/51
51/53
Permissible magnetic field
mT
3
3
Connection voltage
VDC
140 ± 5%
140 ± 5%
Current consumption
A
4.3
4.3
Power
W
600
600
Protection class8)
IP 30
IP 30
Relative humidity of air
%
5 - 85 non condensing
5 - 85 non condensing
9. Technical Data
Please refer to the next page for explanations.