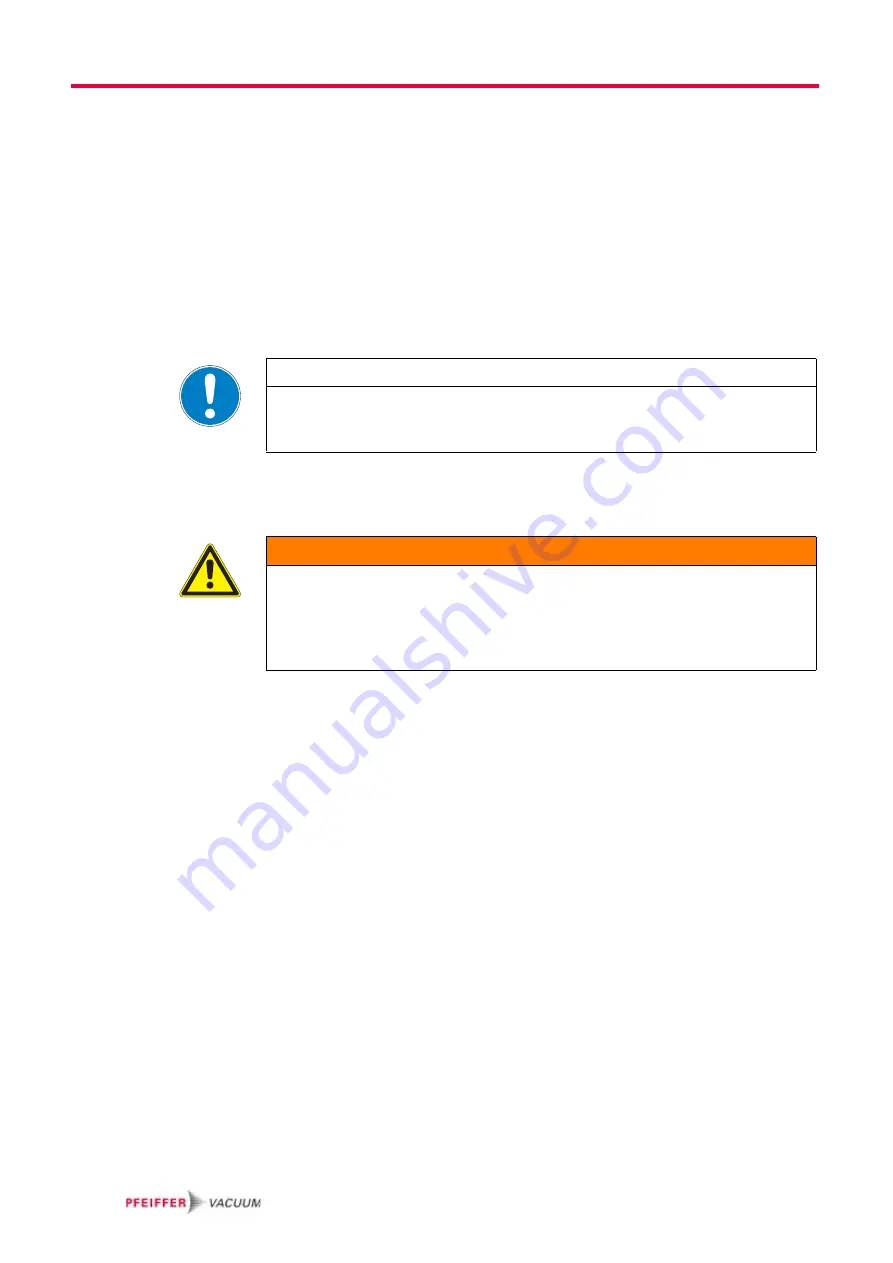
14
Installation
5.7 Connecting an external turbopump
Depending on the configuration the turbopump can be operated seperately from
the pumping station. Please observe the following information!
Î
Install the turbopump according to its operating instructions.
Î
Open the casing of the pumping station if necessary.
Î
Extend necessary control leads for the electronic drive unit of the turbopump
using Pfeiffer Vacuum accessories.
Î
Connect the control leads to the electronic drive unit.
Î
Install an air cooling unit (accessories) for the external turbopump and connect
it to the electronic drive unit.
– Use water cooling optionally.
Installing the high va-
cuum flange
Î
Install the high vacuum flange in accordance with the instructions in the opera-
ting manual of the turbopump.
Î
Ensure the greatest possible cleanliness when installing any high vacuum parts.
Unclean components prolong the pump-down time.
Î
Observe the minimum strengh of 170 N/mm
2
for the flange material.
Connecting the fore-
vacuum side
Î
Extend the fore-vacuum line between turbopump and backing pump.
Î
Connect the fore-vacuum line with small-flange components or threaded hose
couplings. Do not narrow the free cross section of the fore-vacuum flange!
Î
With rigid pipe connections: Install bellows for attenuation of vibrations in the
connection line.
NOTE
Operation of the turbopump with the electronic drive unit separatet
The operation of the turbopump with a separated electronic drive unit is only possible
with by using the respective Pfeiffer Vacuum accessories.
WARNING
Danger of the turbopump being torn-off.
If the rotor is suddenly blocked, torques of up to 4200 Nm can occur; if the turbopump
is not properly fastened, it can tear-off.
Î
Precisely follow installation instructions.
Î
Only use original components for the installation.