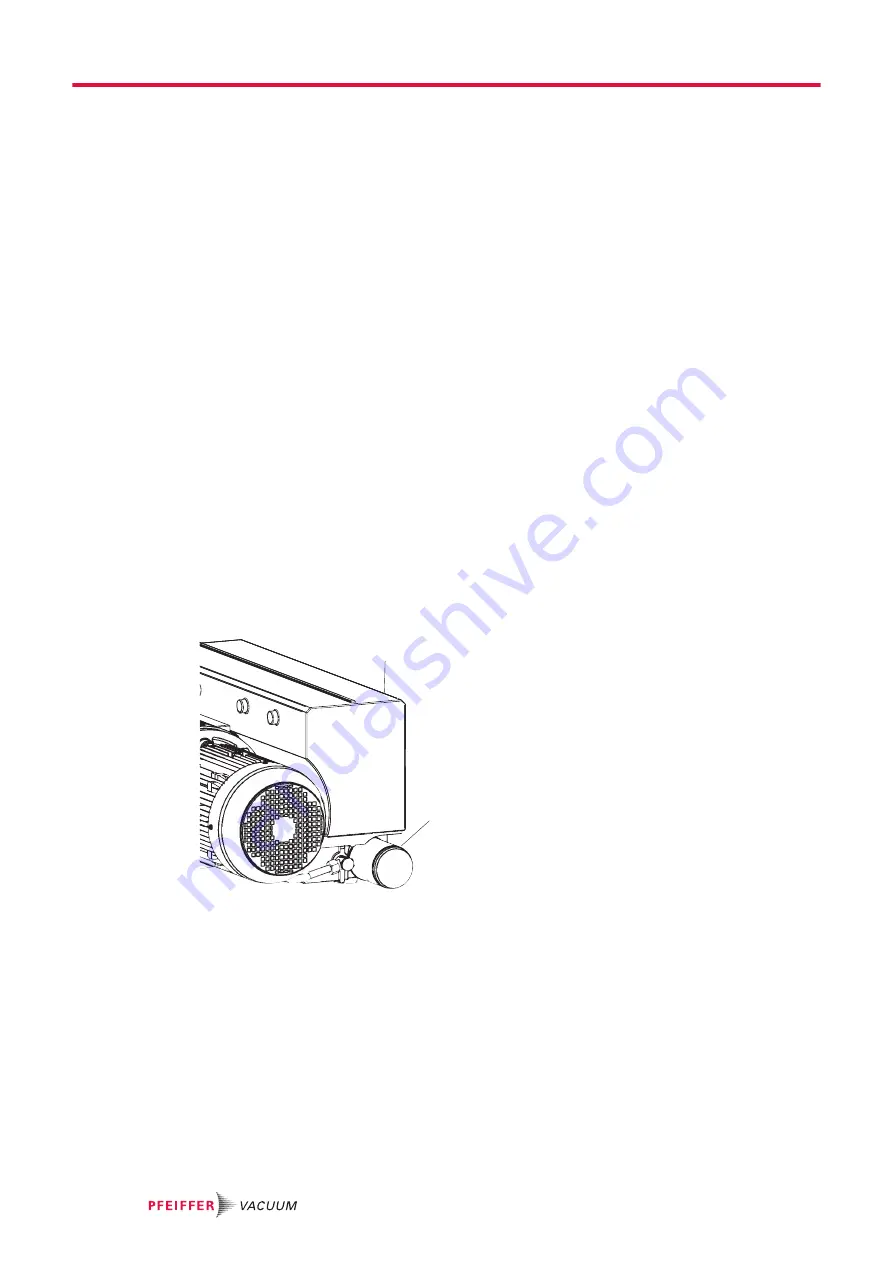
Required aids
● Collection receptacle (> 7 l)
Change operating fluid for cleaning
1. Operate the vacuum pump with the gas ballast open, until it is warm.
2. Perform an operating fluid change.
3. Check the pollution level and repeat the changing of the operating fluid if necessary.
4. In case of highly contaminated operating fluid, replace the operating fluid filter and the exhaust fil-
ter.
7.3.4 Changing the operating fluid filter
The operating fluid filter must be changed:
● in event of saturation
─ You can recognize a saturated operating fluid filter by the fact that the filter housing is cool on
the outside while the rotary vane pump is running at operating temperature.
● with each operating fluid change
● according to the maintenance level
Prerequisites
● Vacuum pump switched off
● Vacuum pump vented to atmospheric pressure
● Operating fluid drained
Required tool
● Strap wrench
Required aids
● Collection receptacle (> 1 l)
1
2
Fig. 17:
Change operating fluid filter
1 Operating fluid separator
2
Operating fluid filter
Procedure
1. Place a collection receptacle below the operating fluid filter.
2. Unscrew the operating fluid filter using a strap wrench.
– Pay attention to escaping operating fluid.
3. Apply oil to the sealing surface of the operating fluid filter.
4. Screw the operating fluid filter on finger-tight.
Maintenance
40/62