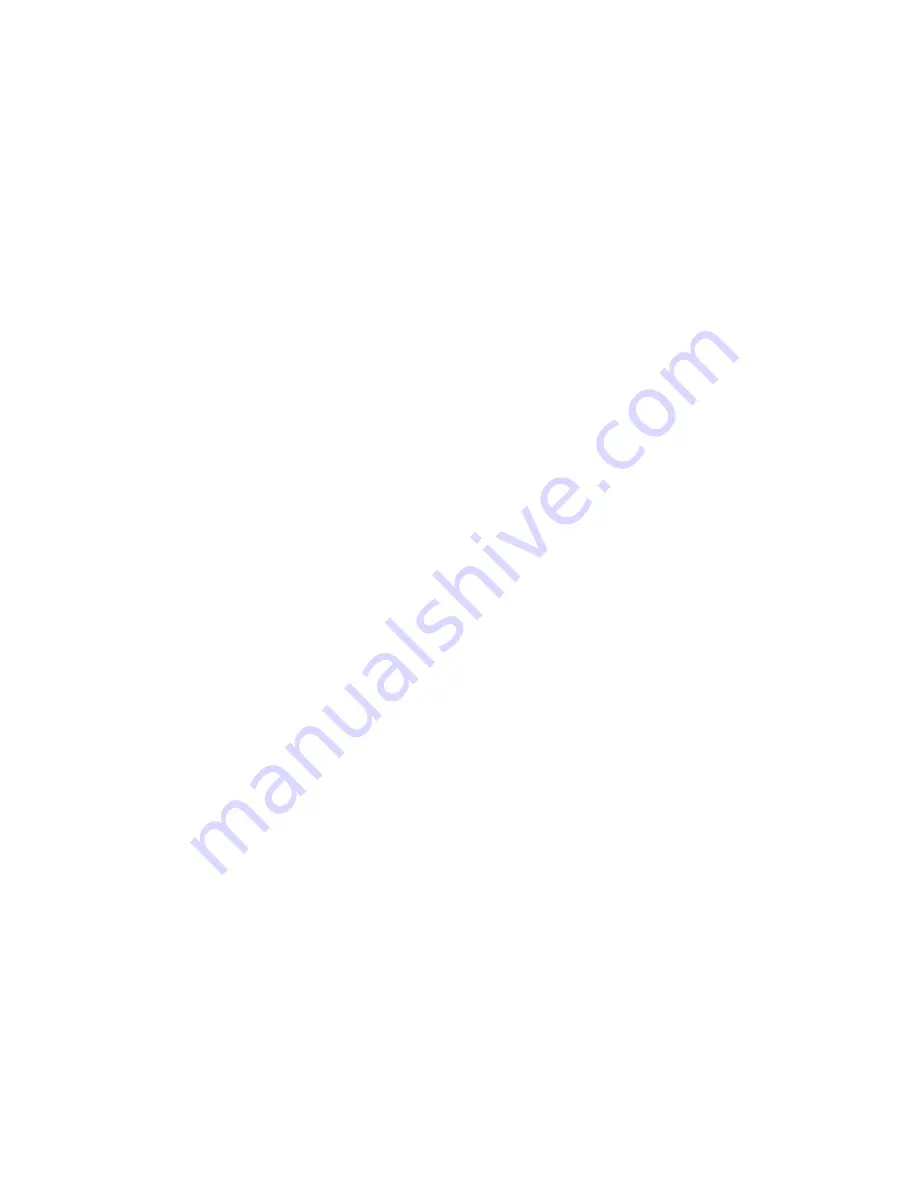
• Do not indulge in horseplay. Distraction can cause accidents.
• Keep hands and fingers away from the throttle lever until it is time to operate the tool.
• Never rest the tool or drill steel on your foot.
• Never point the tool at others.
• Compressed air is dangerous. Never point an air hose at other people or yourself.
• Never use compressed air to blow clothes free of dust.
• Be sure all the hose connections are tight. A loose hose not only leaks but can come completely off of a tool
and, while whipping under pressure, injure the operator and others in the area. Attach safety cables to all hoses
to prevent injury in case a hose is accidentally broken.
• Never disconnect a pressurised air hose. Always turn off the air supply and bleed the tool before disconnecting
a hose.
• The operator must keep limbs and body clear of the drill steel. If a drill steel breaks, the tool with the broken drill
steel projecting from the tool will suddenly surge forward.
• Do not ride the tool with one leg over the handle. An injury can occur if the drill steel breaks while riding the
tool.
• Learn what is underneath the worked material. Be alert for hidden water, gas, sewer, telephone or electric lines.
• To clean any parts of the rock drill, only use proper cleaning solvents that meet current safety and health
standards. Use the cleaning solvents in a well-ventilated area.
• Do not flush the tool or clean any of its parts using diesel fuel. Diesel fuel residue will ignite as the tool is
operated, causing damage to its internal parts. While using models with outside triggers or throttle levers, take
care to prevent accidental operation when laying the tool down.
• Do not operate a tool with broken or damaged parts.
• Never start a tool while it is lying on the ground.
• This tool is not designed for working in explosive atmospheres.
• This tool is not insulated against electric shock.
OPERATION
Lubrication
Always use an air line lubricator with these tools.
Recommended environmentally friendly oils:
TOTAL PNEUMA
SHELL TORCULA 32
Top Oil BIO Uni
Atea PNEU-EKO
Attach the lubricator as close to the tool as practical. Use the recommended LR-1 oiler or the SOOR 6 unit to
ensure sufficient lubrication. If an air line lubricator is not available, disconnect the air hose and pour about 0.5
dcl / 50 ccm of oil into the air inlet and 0.1 dcl / 10 ccm into the supply elbow of the tool at the beginning of each
work shift. Repeat after every 30 minutes of operating the machine.
For operating multiple drilling hammers at one work site, usage of the SOOR unit (for 3 hammers) or the
distribution frames R4 (for 4 hammers) or R5 (for 5 hammers) is recommended.
Before storing the tool or if the tool is to be idle for a period exceeding 3 weeks, pour about 0.5 dcl / 50 ccm of oil
into the air inlet and operate the tool shortly to coat the internal parts with oil.
Lubricate the fronthead regularly (beginning of each shift) with a water resistant grease (use grease nipple).
Do not use any of the environmentally friendly oils for conservation.
Air Supply and Connections
Always use clean, dry lubricated air. Dust, corrosive fumes and/or excessive moisture can ruin the motor of an
air tool. An air line filter can greatly increase the life of an air tool. The filter removes dust and moisture.
Make sure all hoses and fittings are tightly secured and of the correct size.
Water Supply and Connections
Always use clean water. Make sure all hoses and fittings are tightly secured and of the correct size.
Air Leg Installation
Connect the air leg to the yoke of the hammer and firmly tighten the cap nut. Check regularly during the
operation.
Recommended mineral oil:
PARAMO PNEUMAT 46
Summary of Contents for VK 23
Page 6: ......