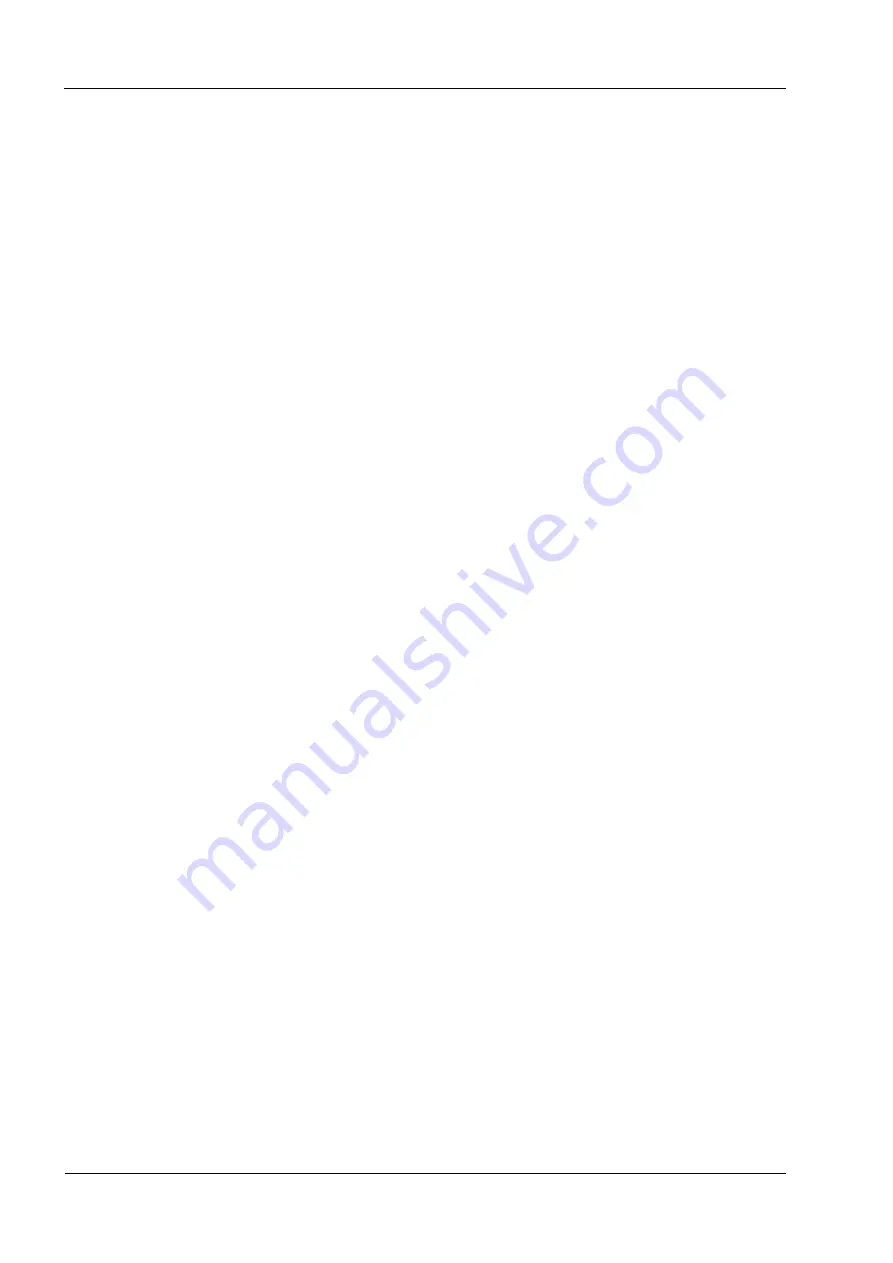
1
4
User’s Handbook, TSL 4230, Issue 4
4016-E61TRS
Clothing
l
Do not wear loose clothing, ties, jewellery, etc.
l
Always wear steel toe cap shoes/boots.
l
Always wear the correct head, eye and ear protection.
l
Always wear suitable overalls.
l
Always replace a spillage contaminated overall immediately.
Lifting heavy components
l
Always use the correct lifting equipment.
l
Never work alone.
l
Always wear a helmet, if the weight is above head height.
De-scaling solution
l
Always wear both hand and eye protection when handling.
l
Always wear overalls and correct footwear.
Waste disposal
l
Do not leave oil covered cloths on or near the engine.
l
Do not leave loose items on or near the engine.
l
Always provide a fireproof container for oil contaminated cloths.
Note: Most accidents are caused by failure to observe basic safety precautions and can be prevented by
recognising potentially dangerous situations before an accident occurs. While there are many potential
hazards that can occur during the operation of the engine which cannot be always be anticipated, and thus a
warning cannot be included to cover every possible circumstance that might involve a potential hazard, by
following these basic principles the danger can be minimised.
This document has been printed from SPI². Not for Resale