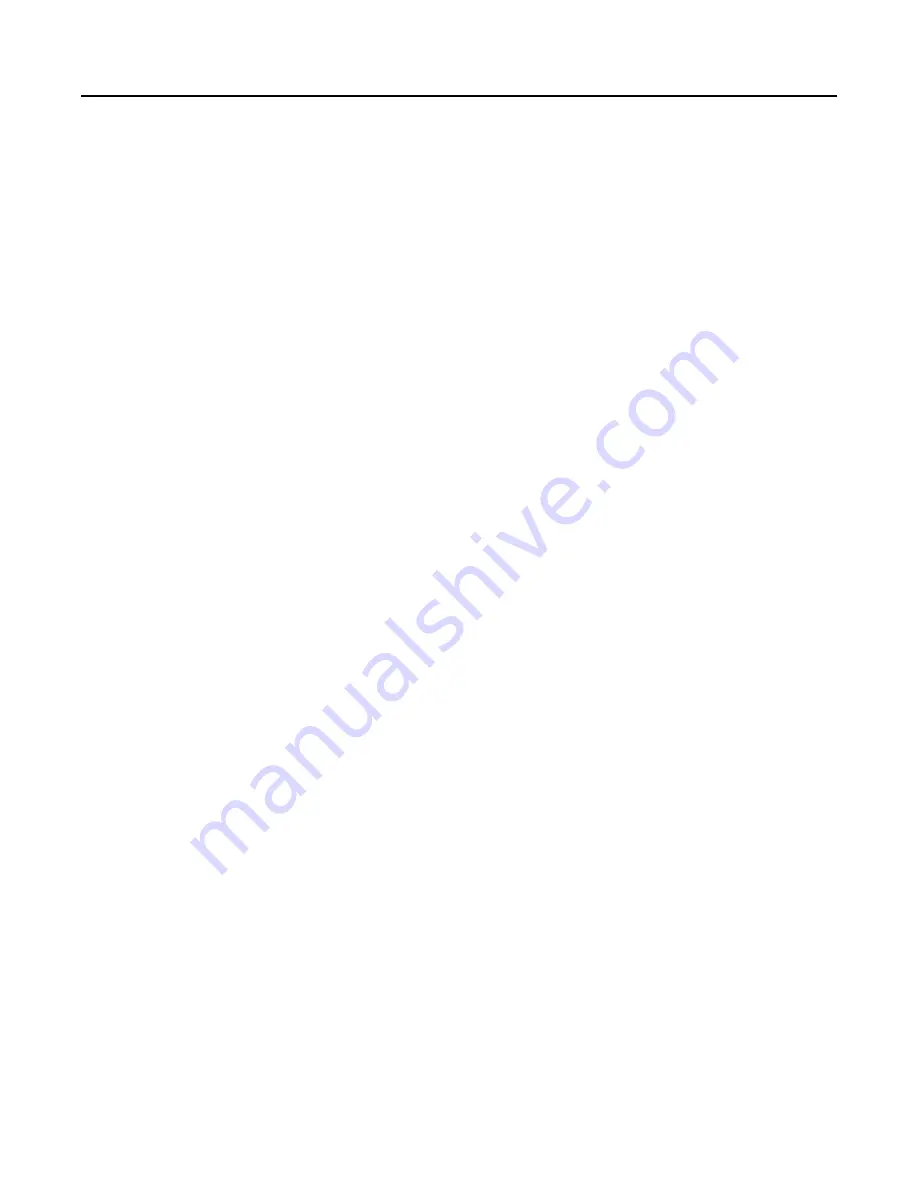
Biodiesel can be blended with distillate diesel fuel.
The blends can be used as fuel. The most commonly
available biodiesel blends are B5, which is 5 percent
biodiesel and 95 percent distillate diesel fuel. B20,
which is 20 percent biodiesel and 80 percent distillate
diesel fuel.
Note:
The percentages given are volume-based. The
U.S. distillate diesel fuel specification
“
ASTM D975-
09a
”
includes up to B5 (5 percent) biodiesel.
European distillate diesel fuel specification
“
EN590:2010
”
includes up B7 (7 percent) biodiesel.
Note:
Engines that are manufactured by Perkins are
certified by use of the prescribed Environmental
Protection Agency (EPA) and European Certification
fuels. Perkins does not certify engines on any other
fuel. The user of the engine has the responsibility of
using the correct fuel that is recommended by the
manufacturer and allowed by the EPA and other
appropriate regulatory agencies.
Specification Requirements
The neat biodiesel must conform to “EN14214” or
“ASTM D6751” (in the USA). Neat biodiesel can only
be blended in mixture of up to 20 percent, by volume
in acceptable mineral diesel fuel meeting
requirements that are listed in Table14 or the latest
edition of “EN590” and “ASTM D 975” commercial
standards. This blend is commonly known as B20.
Biodiesel blends are denoted as
“
BXX
”
with
“
XX
”
representing the content of neat biodiesel contained
in the blend with mineral diesel fuel (for example B5,
B10, B20).
In United States Biodiesel blends of B6 to B20 must
meet the requirements listed in the latest edition of
“ASTM D7467” (B6 to B20) and must be of an API
gravity of 30-45.
In North America biodiesel and biodiesel blends must
be purchased from the BQ-9000 accredited
producers and BQ-9000 certified distributors.
In other areas of the world, the use of biodiesel that is
BQ-9000 accredited and certified, or that is
accredited and certified by a comparable biodiesel
quality body to meet similar biodiesel quality
standards is required.
Engine Service Requirements with B20
Aggressive properties of biodiesel fuel may cause
debris in the fuel tank and fuel lines. The aggressive
properties of biodiesel will clean the fuel tank and fuel
lines. This cleaning of the fuel system can
prematurely block of the fuel filters. Perkins
recommends that after the initial usage of B20
biodiesel blended fuel the fuel filters must be
replaced at 50 hours.
Glycerides present in biodiesel fuel will also cause
fuel filters to become blocked more quickly. Therefore
the regular service interval should be reduced to 250
hours.
When biodiesel fuel is used, crank case oil and
aftertreatment systems (if installed) may be
influenced. This influence is due to the chemical
composition and characteristics of biodiesel fuel,
such as density and volatility, and to chemical
contaminants that can be present in this fuel, such as
alkali and alkaline metals (sodium, potassium,
calcium, and magnesium).
• Crankcase oil fuel dilution can be higher when
biodiesel or biodiesel blends are used. This
increased level of fuel dilution when using
biodiesel or biodiesel blends is related to the
typically lower volatility of biodiesel. In cylinder
emissions control strategies utilized in many of the
industrial latest engine designs may lead to a
higher level of biodiesel concentration in the
engine oil pan. The long-term effect of biodiesel
concentration in crankcase oil is unknown.
• Perkins recommends the use of oil analysis to
check the quality of the engine oil if biodiesel fuel
is used. Ensure that the level of biodiesel in the
fuel is noted when the oil sample is taken.
Performance Related Issues with B20
Due to the lower energy content than the standard
distillate fuel B20 will cause a power loss in order of 2
to 4 percent. In addition, over time the power may
deteriorate further due to deposits in the fuel
injectors.
Biodiesel and biodiesel blends are known to cause
an increase in fuel system deposits, most significant
of which are deposits within the fuel injector. These
deposits can cause a loss in power due to restricted
or modified fuel injection or cause other functional
issues associated with these deposits.
Perkins T400012 Fuel Cleaner is most effective in
cleaning and preventing the formation of deposits.
Refer to “Perkins Diesel Fuel System Cleaner” for
more information. Perkins Diesel Fuel Conditioner
helps to limit deposit issues by improving the stability
of biodiesel whilst also hindering the production of
new deposits. For more information refer to “Perkins
Diesel Fuel Conditioner”. Therefore the use of Diesel
Fuel Cleaner and or Diesel Fuel Conditioner is
recommended when running biodiesel blends,
especially B20.
General Requirements
Biodiesel has poor oxidation stability, which can
result in long-term problems in the storage of
biodiesel. Biodiesel fuel should be used within 6
months of manufacture. Equipment should not be
stored with the B20 biodiesel blends in the fuel
system for longer than 3 months.
44
SEBU9077-01