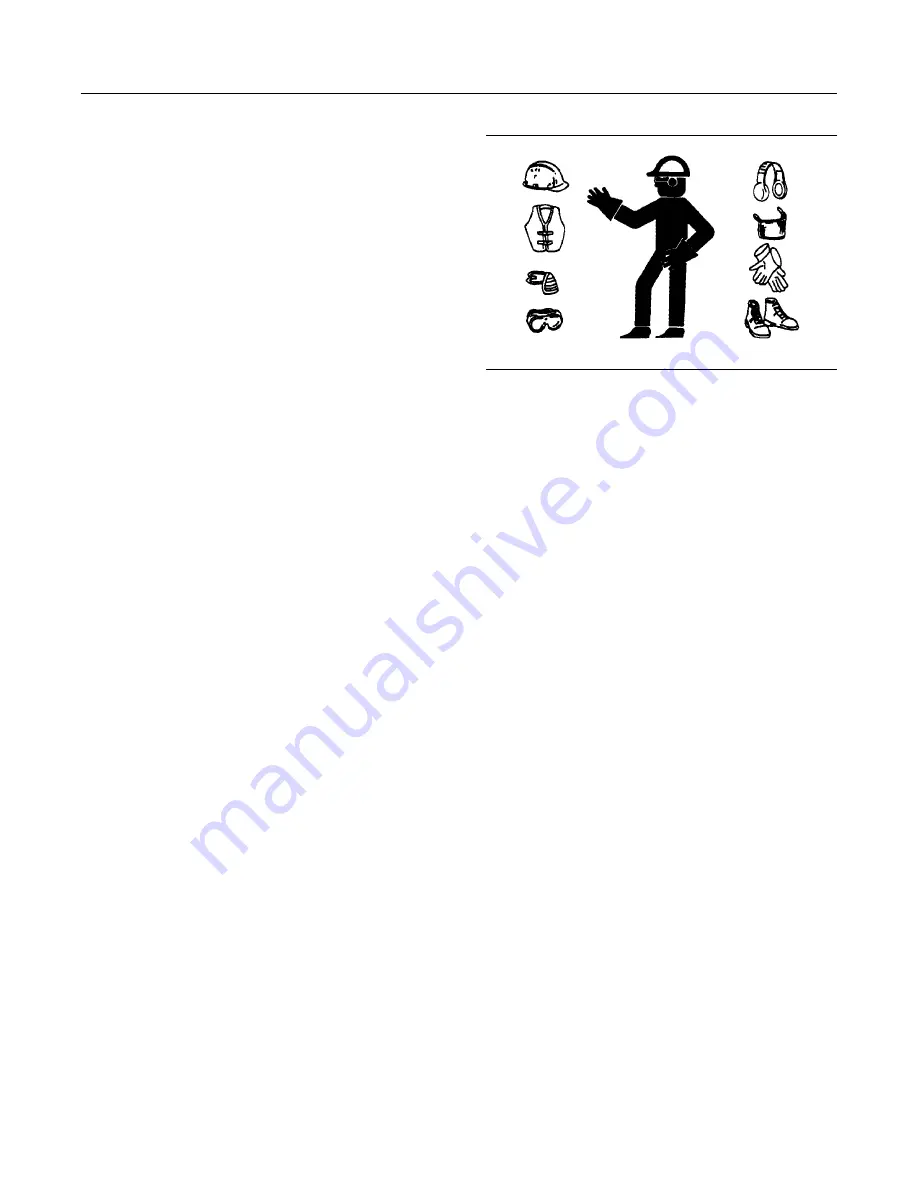
• Do not attempt any repairs or any adjustments to
the engine while the engine is operating.
• Do not attempt any repairs that are not
understood. Use the proper tools. Replace any
equipment that is damaged or repair the
equipment.
• For initial start-up of a new engine or for starting
an engine that has been serviced, make
provisions to stop the engine if an overspeed
occurs. The stopping of the engine may be
accomplished by shutting off the fuel supply and/
or the air supply to the engine. Ensure that only
the fuel supply line is shut off. Ensure that the fuel
return line is open.
• Start the engine from the operators station (cab).
Never short across the starting motor terminals or
the batteries. This action could bypass the engine
neutral start system and/or the electrical system
could be damaged.
Engine exhaust contains products of combustion
which may be harmful to your health. Always start the
engine and operate the engine in a well ventilated
area. If the engine is in an enclosed area, vent the
engine exhaust to the outside.
Cautiously remove the following parts. To help
prevent spraying or splashing of pressurized fluids,
hold a rag over the part that is being removed.
• Filler caps
• Grease fittings
• Pressure taps
• Breathers
• Drain plugs
Use caution when cover plates are removed.
Gradually loosen, but do not remove the last two
bolts or nuts that are located at opposite ends of the
cover plate or the device. Before removing the last
two bolts or nuts, pry the cover loose in order to
relieve any spring pressure or other pressure.
Illustration 6
g00702020
• Wear a hard hat, protective glasses, and other
protective equipment, as required.
• When work is performed around an engine that is
operating, wear protective devices for ears in
order to help prevent damage to hearing.
• Do not wear loose clothing or jewelry that can
snag on controls or on other parts of the engine.
• Ensure that all protective guards and all covers
are secured in place on the engine.
• Never put maintenance fluids into glass
containers. Glass containers can break.
• Use all cleaning solutions with care.
• Report all necessary repairs.
Unless other instructions are provided, perform
the maintenance under the following conditions:
• The engine is stopped. Ensure that the engine
cannot be started.
• Disconnect the batteries when maintenance is
performed or when the electrical system is
serviced. Disconnect the battery ground leads.
Tape the leads in order to help prevent sparks.
• Do not attempt any repairs that are not
understood. Use the proper tools. Replace any
equipment that is damaged or repair the
equipment.
Pressurized Air and Water
Pressurized air and/or water can cause debris and/or
hot water to be blown out. This action could result in
personal injury.
When pressurized air and/or pressurized water is
used for cleaning, wear protective clothing, protective
shoes, and eye protection. Eye protection includes
goggles or a protective face shield.
8
SEBU9074-01