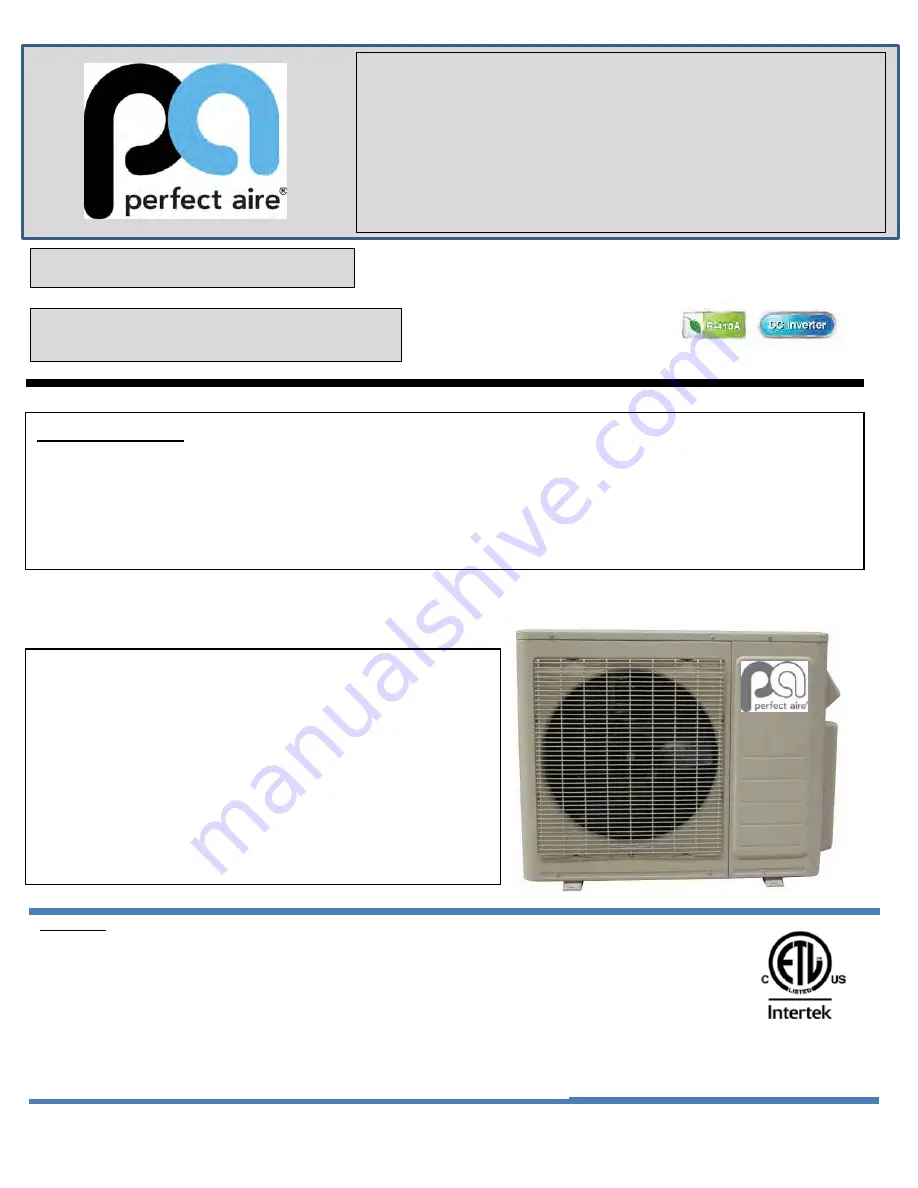
Multi outdoor units
SERVICE MANUAL
Multi zone
CONDENSING UNITS
Revision B:
ODMI-C1-1511
Model Numbers:
WARNING
Installation MUST conform with local building codes or, in the absence of local
codes, with the National Electrical Code NFPA70/ANSI C1-1993 or current edition
and Canadian Electrical Code Part1 CSA C.22.1.
The information contained in the manual is intended for use by a qualified service
technician familiar with safety procedures and equipped with the proper tools and
test instruments
Installation or repairs made by unqualified persons can result in hazards to you
and others.
Failure to carefully read and follow all instructions in this manual can result in
equipment malfunction, property damage, personal injury and/or death.
Table of Contents
1. Indoor Unit Combination
2. Suggested Indoor Unit Model Numbers
3. Dimension Of Outdoor Unit
4. Refrigerant Cycle Diagram
5. Installation Details
6. Electronic Function
7. Wiring Diagrams
8. Trouble Shooting
9. Disassembly Instructions
1PAMSH18-MZO2-16
1PAMSH27-MZO3-16
1PAMSH36-MZO4-16
Summary of Contents for 1PAMSH18-MZO2-16
Page 3: ... Model 1PAMSH27 MZO3 16 W210 metal plate 113 Model 1PAMSH36 MZO4 16 W520 metal plate 128 ...
Page 6: ...2 Suggested Indoor Unit Model Numbers ...
Page 7: ......
Page 9: ......
Page 23: ...7 Wiring Diagrams 8 1 Wiring diagram of 1 drive 2 outdoor 1PAMSH18 MZO2 16 ...
Page 24: ...PCB board of 1PAMSH18 MZ O2 16 ...
Page 25: ...IPM board of 1PAMSH18 MZO2 16 ...
Page 26: ......
Page 27: ...8 2 Wiring diagram of 1 drive 3 outdoor 1PAMSH27 MZO3 16 ...
Page 28: ......
Page 29: ......
Page 30: ...PCB board of 1PAMSH27 MZO3 16 ...
Page 31: ...IPM board of 1PAMSH27 MZO3 16 ...
Page 32: ...8 3 Wiring diagram of 1 drive 4 outdoor 1PAMSH36 MZO4 16 ...
Page 33: ...PCB board of 1PAMSH36 MZO4 16 ...
Page 34: ...IPM board of 1PAMSH36 MZO4 16 ...
Page 35: ...PFC board of 1PAMSH36 MZO4 16 ...
Page 36: ...8 4 Wiring diagram of 1 drive 5 outdoor ...
Page 37: ......
Page 71: ...IPM for dual tri zone IPM for qua zone P N for dual tri zone ...
Page 72: ...P N for qua zone ...
Page 73: ...bridge rectifier for dual tri zone bridge rectifier for qua zone ...
Page 74: ...Remark Measure the DC voltage between and port The normal value should be 190V 250V ...
Page 76: ...Two ports of the inductance Inductance ...
Page 77: ......
Page 80: ...Vsp FG ...
Page 82: ......
Page 85: ......
Page 88: ......
Page 90: ......
Page 103: ...6 EXV check Disconnect the connectors ...
Page 105: ...Red Blue Red Yellow ...
Page 106: ...Brown Orange Brown White ...
Page 121: ...Screws of front panel Screws of right rear panel Screws of top cover ...
Page 136: ...Screws of front panel Screws of big handle Screws of right rear panel ...