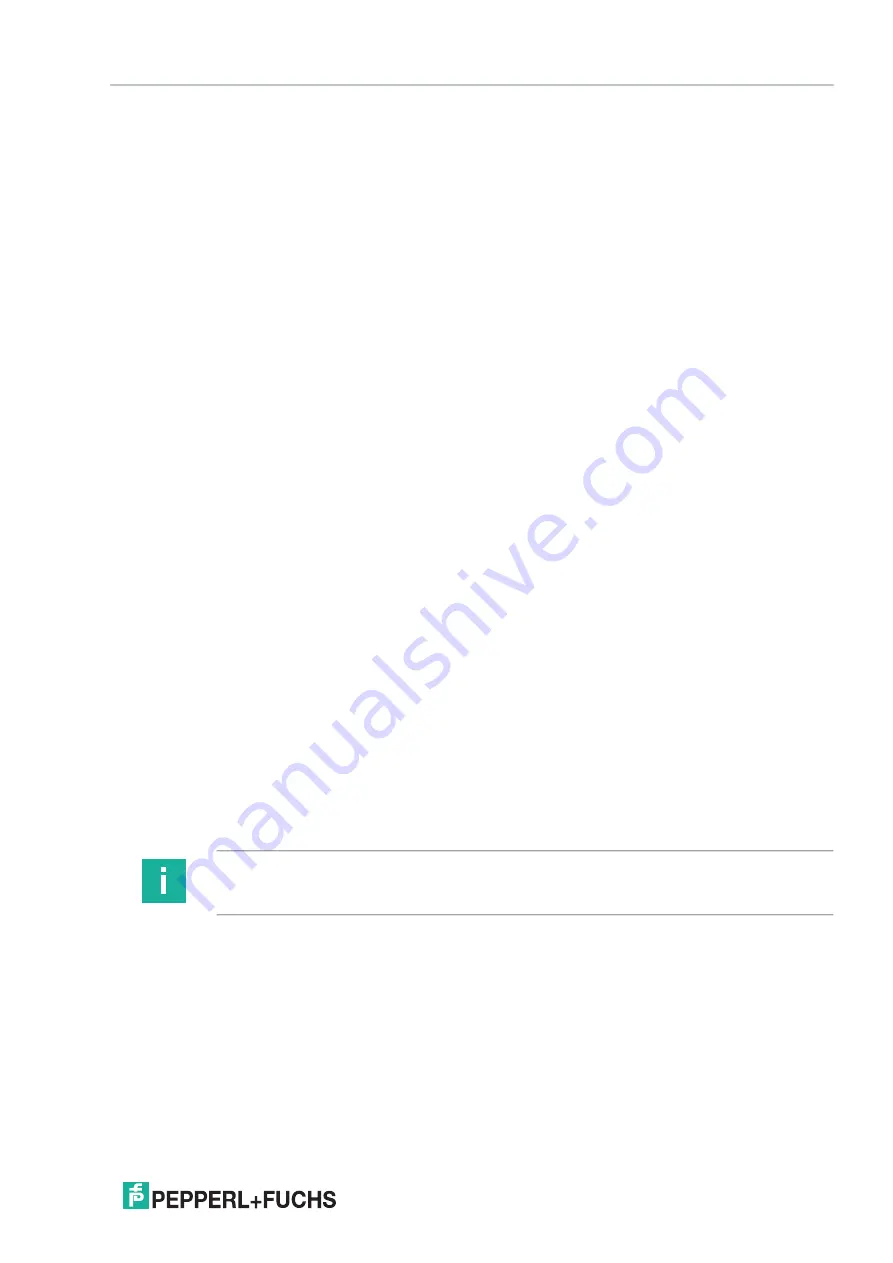
Functional Safety KFD0-CS-(Ex)*.50(P), KFD0-CS-(Ex)*.51(P)
Planning
20
21
-0
7
11
3.2
Assumptions
The following assumptions have been made during the FMEDA:
•
Failure rate based on the Siemens standard SN 29500.
•
Failure rates are constant, wear is not considered.
•
The device will be used under average industrial ambient conditions comparable
to the classification "stationary mounted" according to MIL-HDBK-217F.
Alternatively, operating stress conditions typical of an industrial field environment similar
to IEC/EN 60654-1 Class C with an average temperature over a long period of time
of 40
º
C may be assumed. For a higher average temperature of 60
º
C, the failure rates
must be multiplied by a factor of 2.5 based on experience. A similar factor must be used
if frequent temperature fluctuations are expected.
SIL 2-Application
•
To build a SIL safety loop for the defined SIL, it is assumed as an example that this device
uses 10 % of the available budget for PFD
avg
/PFH.
•
For a SIL 2 application operating in low demand mode the total PFD
avg
value
of the SIF (
S
afety
I
nstrumented
F
unction) should be smaller than 10
-2
,
hence the maximum allowable PFD
avg
value would then be 10
-3
.
•
For a SIL 2 application operating in high demand mode the total PFH value
of the SIF should be smaller than 10
-6
per hour, hence the maximum allowable PFH value
would then be 10
-7
per hour.
•
The safety-related device is considered to be of type
A
device with a hardware fault
tolerance of
0
.
•
Since the safety loop has a hardware fault tolerance of
0
and it is a type
A
device,
the SFF must be > 60 % according to table 2 of IEC/EN 61508-2 for a SIL 2 (sub) system.
3.3
Safety Function and Safe State
Safety Function
The device transfers current signals from the input to the output with a maximum tolerance
of 5 % related to the full signal range.
Safe State
In the safe state the output is < 3.6 mA.
Reaction Time
The reaction time for all safety functions is < 20 ms.
Note
See corresponding datasheets for further information.