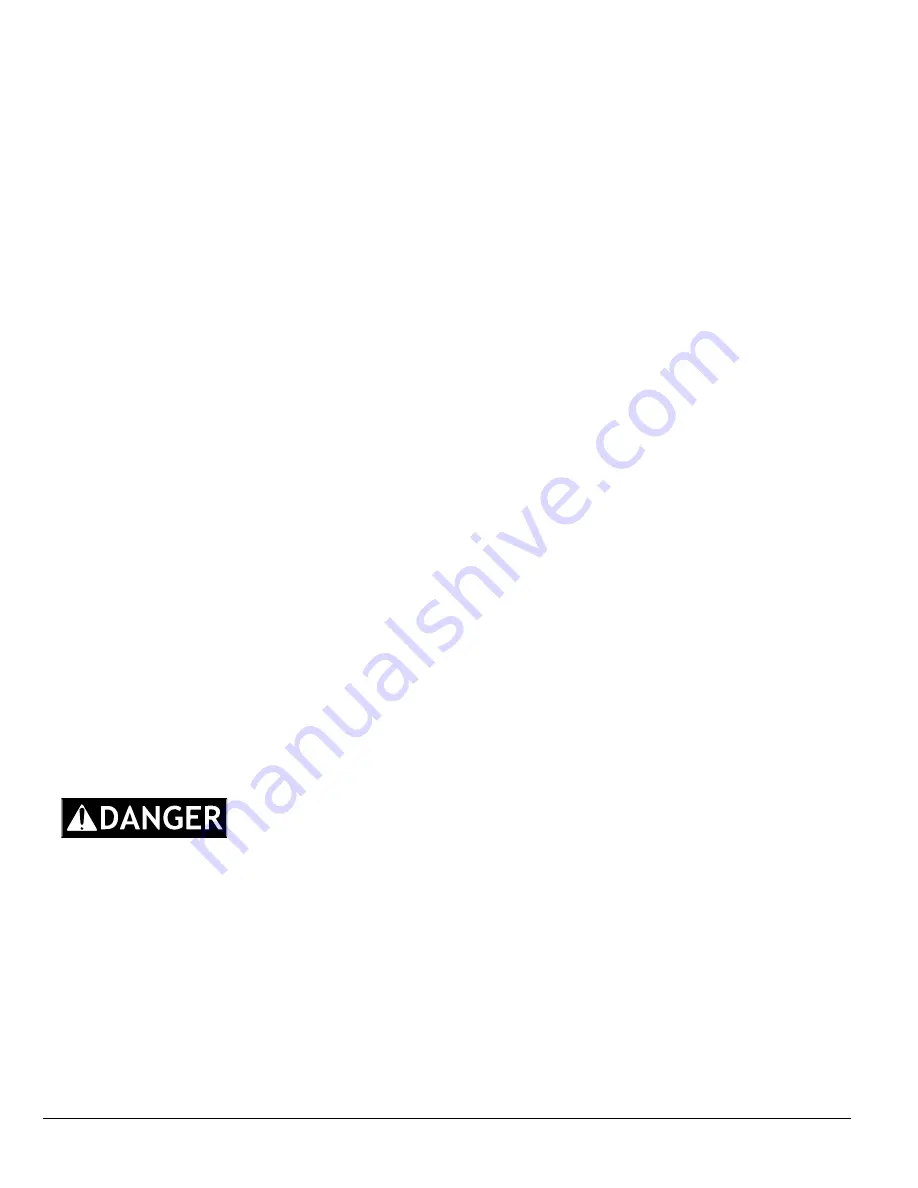
PENTALIFT EQUIPMENT CORPORATION
M086R06
December 8, 2017 10:37 AM
LDL Dock Lift Owners Manual
OWNER RESPONSIBILITY
The Owner's Responsibilities include the following:
1.
The owner should recognize the inherent danger of the interface between dock and transport vehicle. The Owner must,
therefore, train and instruct operators in the safe use of dock levelling devices.
2.
When a transport vehicle is positioned as closely as practicable to a dock levelling device, there shall be at least 4” (100 mm) of
overlap between the front edge of the Hinged Bridge and the edge of the floor or sill of the transport vehicle.
3.
Nameplates, cautions, instructions and posted warnings shall not be obscured from the view of operating or maintenance
personnel for whom such warnings are intended.
4.
Manufacturer’s recommended periodic maintenance and inspection procedures in effect at date of shipment shall be followed,
and written records of performance of these procedures should be kept.
5. Removal from Service:
Any lift not in safe operating condition such as, but not limited to excessive leakage, missing
rollers, pins or fasteners, any bent or cracked structural members, cut or frayed electric, hydraulic or air lines, damaged
or malfunctioning controls or safety devices, etc. shall be removed from service until it is repaired to Pentalift Equipment
Corporation’s standards.
6. Pentalift Equipment Corporation
shall supply replacement nameplates, caution or instruction labels and operating and
maintenance manuals upon request of the owner. The owner shall see that all nameplates and caution and instruction
markings or labels are in place and legible and that the appropriate operating and maintenance manuals are provided to users.
7.
Modifications or alterations of dock levelling devices shall be made only with written permission of
Pentalift Equipment
Corporation
. Alteration permission must be signed by both the Pentalift Post Sale Customer Service Manager and the
President to be valid.
8.
When industrial trucks are driven on and off transport vehicles during the loading and unloading operation, the brakes on the
transport vehicle shall be applied and wheel chocks or positive restraints that provide the equivalent protection of wheel chocks
engaged.
NOTE:
It is recognized that these devices are intended to secure a transport vehicle to a loading dock by mechanical means.
However, no standards currently exist for the strength, construction or attachment of the under ride guard on a transport vehicle. It
is therefore recommended that users of such positive restraint devices review:
•
The means of attachment to the transport vehicle
•
The strength of the overall connection
•
The proper coordination of the actuation of devices with any signalling system used
•
The need to use wheel chocks
9.
In selecting dock levelling devices, it is important to consider not only present requirements, but also future plans or adverse
environments.
iv
Unless specifi cally agreed to in writing by Pentalift Equipment Corporation at the time the
equipment is ordered and prior to the equipment’s manufacture, this equipment is sold as
a complete package. It is not to be altered, changed or added to in any way or form, in its
confi guration and function, without the written permission of Pentalift Equipment Corporation.
If requested by a customer, Pentalift Equipment Corporation is not supplying all or some of the power unit and / or con-
trol components for the equipment’s application. The power unit and controls constitute important safety and functional
aspects of the equipment. It is the customer’s responsibility to address the operational and safety issues associated
with providing the required controls and power units to satisfy the operational and safety requirements of the equipment.
The customer’s decision to supply all or some of these components indicates that the customer is taking full responsibil
-
ity for any and all possible operational, safety and liability issues associated to the product and its configuration. The
customer also agrees to absolve Pentalift Equipment Corporation from any and all possible operation, safety and liability
issues.