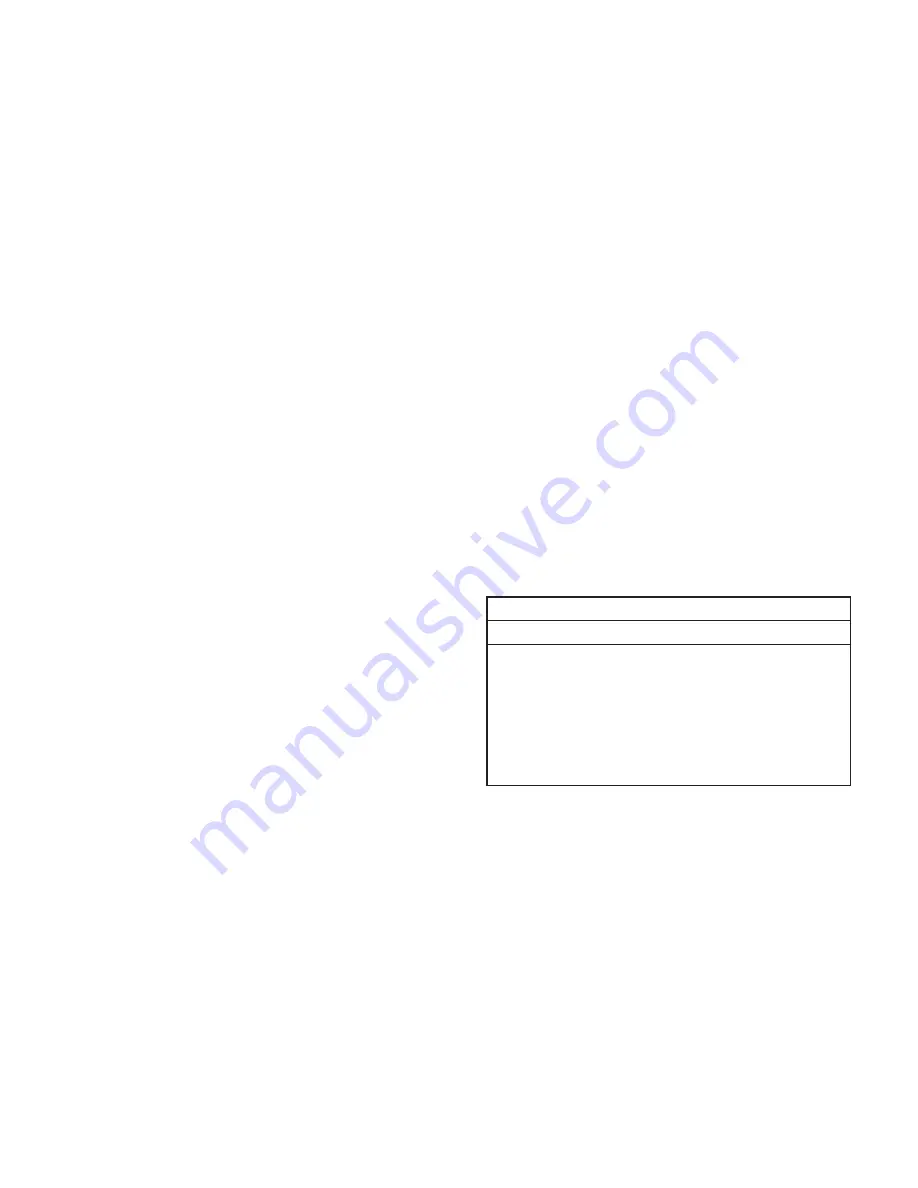
23833A273 10/08/14
3
VALVE SERVICE
When servicing valves always replace O-rings.
Remove bolts and valve clamp. Remove valve cover
on top of fluid access to valve components. Suction
and discharge valve will show a wear pattern on
seating surface but need not be replaced unless
extreme wear, cracks or erosion is present on valve.
All valves and seats are interchangeable but it is
recommended to put them back in the same order as
taken out if not renewing the components. To replace
valve components, clean bores to remove corrosion
or burrs, and lubricate and replace O-rings in bottom
of bore. Lubricate valve seat and replace O-ring. On
the valve, make sure the spring is inserted squarely
before putting assembly into fluid end. Repeat for the
discharge valve, insert valve cover and secure.
REPLACING PISTON ROD SEALS
The rod seal assembly contains two seals, and two
oil seals with lips facing power end. The fluid end
must be removed before the oil seal can be replaced.
Unscrew Allen screws and place into the other two
tapped holes. Gradually screw them in to push oil seal
housing off the retainer. Assemble new seals in oil seal
housing. An assembly thimble should be used on end
of crosshead rod for sliding oil seal housing back into
retainer. Check gasket replace if damaged.
An assembly thimble should be used on small end of
the piston rod to expand sealing edge as it is pushed
on. The thimble should be machined from high carbon
steel and polished on the exterior to reduce possibility
of seal lip damage.
SERVICING CRANKCASE PARTS
To remove the crankcase you do not need to remove
the cylinder body from the crankcase. Remove the
connecting link caps from the connecting links and
push the free links toward the cylinder end as far
as possible. Take off the bearing caps and pull the
crankshaft through the bearing opening.
REPLACING CRANKSHAFT AND
SHIMMING BEARINGS
Remove bolts from both bearing caps. Carefully
remove bearing cap, shims and O-rings and discard
shims and O-rings. Inspect and clean shim surfaces
on both bearing caps and crankcase.
Slide crankshaft into the crankcase and rest bearings
on the sides of the crankcase. Place .045" shim on
the drive side bearing cap and place 4.38" O.D. O-ring
onto the bearing cap.
Cover key-way slot and slide the bearing cap with
oil seal over the drive shaft. Tighten the cap screws.
Install the non-drive side cap without shims or O-ring.
Secure with cap screws and tighten alternately so the
crankshaft can be fully rotated by hand to seat the
tapered roller bearings.
Measure the shim gap adjacent to each of the screws
by inserting a flat feeler gauge in the gap until it
bottoms out. The required shim thickness for this cap
is equal to the average of the two gap measurements,
plus .005" constant.
Remove the two bolts and cap and place the correct
shim thickness on this cap. If the required shim
thickness does not match an .003" increment of a
green shim, round up or down to the nearest .003"
shim increment.
Remove non-drive side bearing cap and place the
4.38" O.D. O-ring on the cap and reinstall. Tighten the
screws as the crankshaft is fully rotated by hand to
seat the bearings and so no significant binding results.
SERVICING CONNECTING LINKS
When the connecting link bearings are worn standard
replacement bearing inserts can be installed in the
connecting links. These bearings should not be
tampered with or changed in size at the time of
assembly. Do not change the size of the link by filing
or grinding the faces. When reinstalling the links on
the crankshaft be sure to place the oil holes upward
for proper lubrication.
When installing new bushings for the wrist pin, these
bushings should be reamed to proper size after
pressing into the link. Do not ream "D" bushings.
RECOMMENDED TORQUE (foot-pounds)
FASTENER LOCATION
Link Bearing Caps - 25
Crankshaft End Caps - 20
Capscrew Holding Piston - 20
Packing Assembly to Piston Rod - 20
Valve and Cylinder Cover Clamps - 80
Capscrew (Fluid End to Crankcase) - 1/2"-50, 5/8"-85
CROSSHEAD AND PISTON RODS
Repair parts for the crosshead and piston rod are
supplied as a complete unit. If either of these parts
becomes worn it is necessary to replace both the
crosshead and piston rod. Under normal conditions
a crosshead will not wear nor will the bore of the
crankcase wear to the extent that replacement will be
required. A clearance of .002" to .004" is standard for
the crosshead.
RECONDITIONING CRANKSHAFTS
When crank pins are slightly damaged, they can
sometimes be reconditioned for further use. This can
be done with emery cloth and polishing until all ridges
are completely removed. The final polishing operation
should be performed by using a very fine emery cloth.