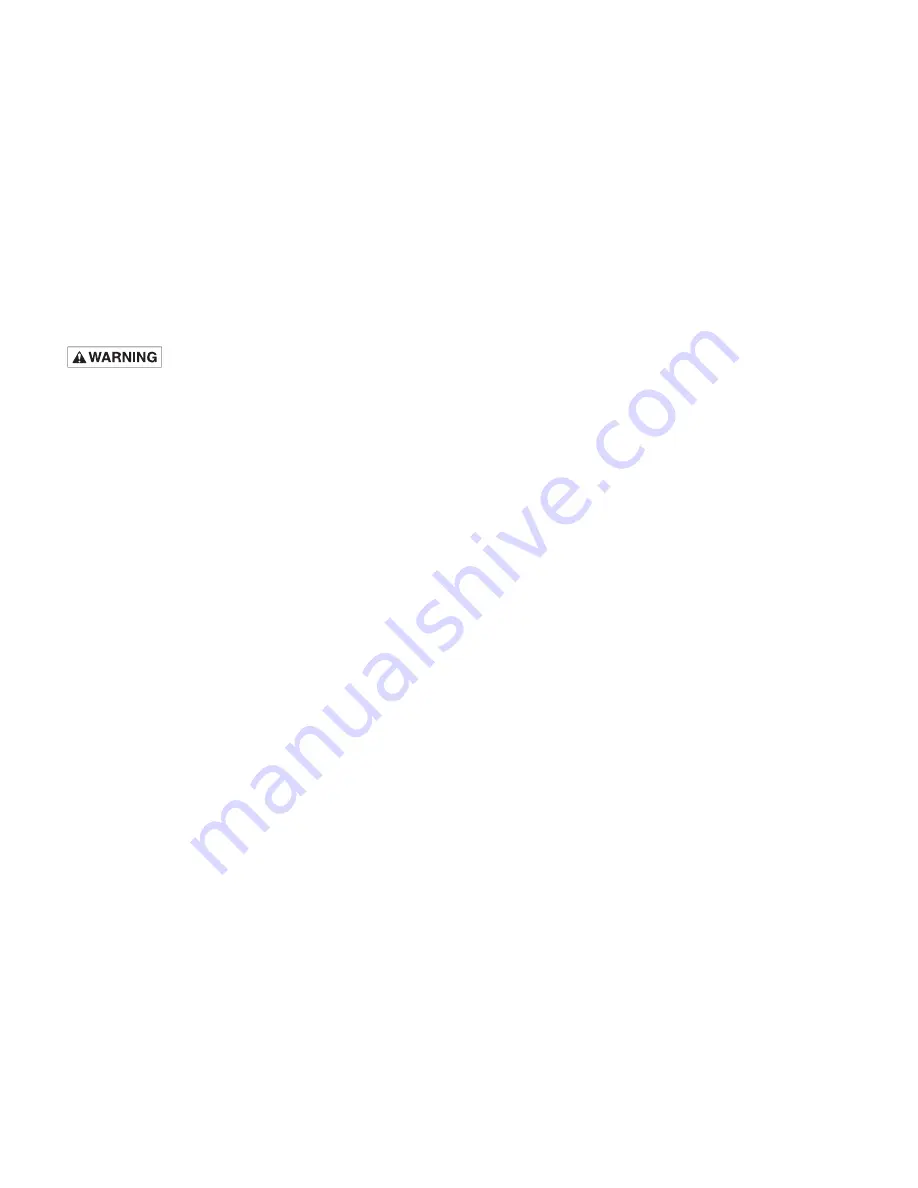
23833A273 10/08/14
2
INSTRUCTIONS
CAUTION: Positive displacement pumps must have a
proper size and operable type of pressure regulating
valve or pressure relief valve piped into the discharge
line. This is mandatory to prevent damage to pump
and piping or possible injury to personnel. Do not
install any valves or shut-off devices in the bypass line
from pressure regulator tank or supply.
CAUTION: All pumps should be installed level. For
mobile applications the maximum angle of intermittent
operation should be no more than
5° in any one direction.
CALIFORNIA PROPOSITION 65 WARNING:
This product and related
accessories contain chemicals known to the
State of California to cause cancer, birth
defects or other reproductive harm.
It is recommended to install a pulsation dampener
in the discharge line to smooth out pressure pulse.
This can protect pump parts and piping for longer life
and quieter operation.
BELT DRIVE
With belt drives the pulley on both the engines and
pump should be located as close as possible to
bearing to reduce bearing and shaft bending loads.
Make sure that all bolts, nuts, set screws, and keys
are properly tightened. On multiple V-belt drives, a
complete set of new belts should be installed when
making a replacement.
STARTING PUMP
Fill pump crankcase with recommended oil (SAE) to
the level mark on oil saber. Replace all drain plugs
in pump and piping. Inspect tank to be sure that
no foreign material is in tank or suction line. Fill the
tank at least half full or connect suction to water
supply. Open valve (if present) in suction line. Avoid
prolonged dry operation which may cause excessive
wear on plunger packing. Be sure that an operating
pressure gauge is located in the discharge line.
Use heavy duty, liquid filled, pulsation free pressure
gauge. Make sure all valves, including spray gun or
nozzles, are open in discharge line. Spray gun may
be anchored to discharge back into tank. Completely
back off the pressure adjusting device on pressure
regulating valve. Check pressure rating for pulsation
dampener, pressure regulator and pipe fitting to make
sure working pressure is not over maximum pressure
rating.
After starting, close discharge valve or spray gun
slowly while watching pressure gauge to make sure
relief valve or unloader is operating properly. Adjust
relief valve or unloader to desired pressure. Cycle
nozzles, or gun on and off to be sure that pressure
adjustment and regulator operation are satisfactory.
Nozzle capacity should not exceed 90% of pump
capacity for satisfactory regulator operation. Avoid
freezing by draining all water from pump and system
in cold weather. There is a 3/8 NPT drain plug for each
cylinder chamber.
SUGGESTED MAINTENANCE SCHEDULE
Check oil level – Daily
Drain & change oil – 300 hrs.
Drain at operating temperature to prevent
contamination from settling.
Inspect piston packing and spacer rings – 500 hrs.
Inspect frequently for leakage; piston packing is
allowed to drip in order to cool and lubricate packing.
Inspect valves and springs – 500 hrs.
Replace if cracks and heavy wear are present.
Inspect connecting link bearing inserts – 1000 hrs.
Replace at first signs of fatigue or wear to prevent
damage to crankshaft.
Inspect crankshaft tapered roller bearings and piston
stud – 2000 hrs.
Replace if there is any pitting on the seal surface or if
the surface is rough.
LUBRICATION
Pump –
Fill crankcase with 2 quarts of oil. Maintain
oil level between the high and the low level marks on
bayonet oil gauge inserted through crankcase cover.
Add extra quart for crankcase speeds under 300 rpm.
Drain oil from crankcase after first 30 hours of
operation. Refill with proper oil. Check oil levels
regularly. Change oil immediately if water droplets are
found on bayonet gauge.
SERVICE
Disconnect electrical leads to motor or remove spark
plug leads on engine before proceeding.
PLUNGER SEAL SERVICE
Remove the three seal lubricating lines and nuts
holding the fluid end and slide head. Rotate
crankshaft until plunger is flush with seal housing.
Slide seal housing forward to clear plunger and
remove. Remove seals and clean seal housing. Install
new seal. Lubricate with waterproof grease and repeat
steps to install plunger seal.