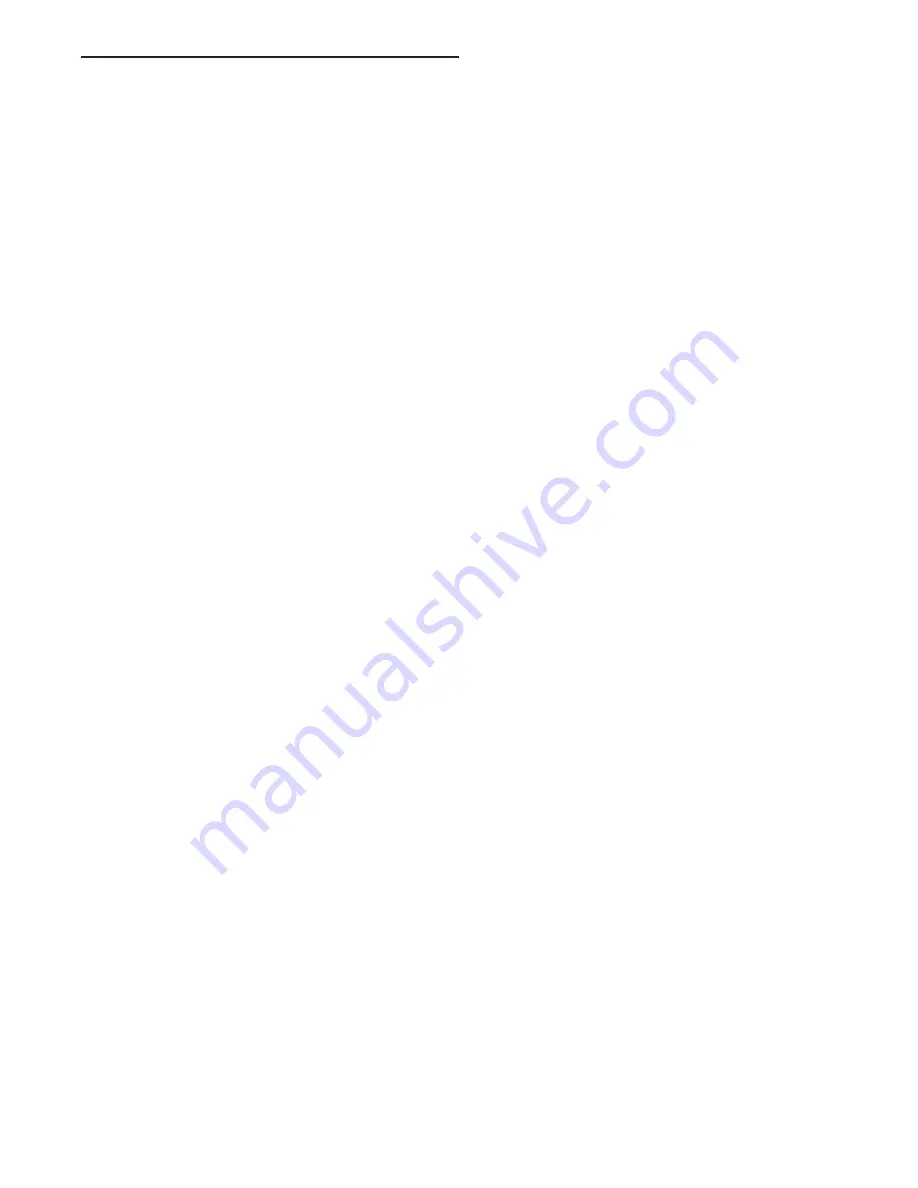
EQUIPMENT INSTALLATION
General Warnings And Safety Information
Electrical
There are no user-serviceable parts in the AC adapter, motor,
or controller. In the event of a failure, these should be replaced.
• All electrical connections must be completed according to
local codes.
• Use only the power AC adapter that is supplied. If the AC
adapter is replaced, use a Class II, 12 volt, 150 mA supply.
• The power outlet must be grounded and always on.
• To disconnect power, unplug the AC adapter from its
power source.
• Install an appropriate grounding strap across the inlet
and outlet piping of the water system to ensure proper
grounding is maintained.
Mechanical
• Do not use petroleum based lubricants such as petroleum
jelly, oils, or hydrocarbon based lubricants. Use only 100%
silicone lubricants.
• All plastic connections should be hand tightened.
Plumber's tape should be used on connections that do not
use an O-ring seal. Do not use pliers or pipe wrenches.
• All plumbing must be completed according to local codes.
• Soldering of the plumbing should be done before
connecting to the valve. Excessive heat will cause interior
damage to the valve.
• Observe drain line requirements.
• Do not use lead-based solder for sweat solder
connections.
• The drain line must be a minimum of 1/2-inch diameter.
Use 3/4-inch pipe the pipe length is greater than
20 feet (6 m).
• Do not support the weight of the system on the control
valve fittings, plumbing, or the bypass.
• It is not recommended to use sealants on the threads.
Use plumber's tape on all threads.
General
• Observe all warnings that appear in this manual.
• This system is not intended to be used for treating water
that is microbiologically unsafe or of unknown quality
without adequate disinfection before or after the system.
• Keep the unit in the upright position. Do not turn on side,
upside down, or drop. Turning the tank upside down will
cause media to enter the valve.
• Operating ambient temperature is between 34°F (1°C)
and 120°F (49°C).
• Operating water temperature is between 35°F (1°F) and
100°F (38°C).
• Working water pressure range is 20 to 125 psi
(1.38 to 8.61 bar). In Canada, the acceptable working
water pressure range is 20 to 100 psi (1.38 to 6.89 bar).
• Use only salts designed for water softening. Acceptable
salt type is sodium chloride pellet salt.
• Follow state and local codes for water testing. Do not use
water that is micro-biologically unsafe or of unknown
quality.
• When filling media tank, do not open water valve
completely. Fill tank slowly to prevent media from exiting
the tank.
• Always make modifications to house plumbing first.
Connect to valve last.
• Plastic parts and O-rings may be damaged by heat and
solvents. When constructing plumbing connections, allow
heated parts to cool and protect parts from solvents.
System Recharge Cycles
Service (Downflow):
Untreated water is directed down through the resin bed and up
through the riser tube. The hardness ions attach themselves
to the resin and are removed from the water. The water is
conditioned as it passes through the resin bed.
When a recharge cycle starts, the softener goes through seven
cycles. During the recharge cycle, the softener will allow
untreated water to bypass into the building.
1. Backwash 1 (Upflow):
The flow of water is reversed by the control valve and
directed down the riser tube and up through the resin bed.
During the backwash cycle, the bed is expanded and debris
is flushed to the drain.
2. Brine Draw (Downflow):
The brine draw cycle takes place during the slow rinse
cycle. The control directs water through the brine injector
and brine is drawn from the salt tank. Brine draw is
completed when the air check in the salt tank closes.
Slow Rinse (Downflow):
The brine is directed down through the resin bed and up
through the riser tube to the drain. The hardness ions are
displaced by sodium ions and are sent to the drain. The
resin is recharged during the brine cycle.
3. Repressurize Cycle (Hard Water Bypass Flapper Open):
This cycle closes the flappers for a short time to allow the
air and water to hydraulically balance in the valve before
continuing the recharge.
4. Fast Rinse 1 (Downflow):
The control directs water down through the resin bed and
up through the riser tube to the drain. Any remaining brine
residual is rinsed from the resin bed.
5. Backwash 2 (Upflow):
The flow of water is reversed by the control valve and
directed down the riser tube and up through the resin bed.
During the backwash cycle, the bed is expanded and debris
is flushed to the drain.
6. Fast Rinse 2 (Downflow):
The control directs water down through the resin bed and
up through the riser tube to the drain. Any remaining brine
residual is rinsed from the resin bed.
7. Brine Refill:
Water is directed to the salt tank at a controlled rate, to
create brine for the next recharge.
AUTOTROL
368 Service Manual• 3