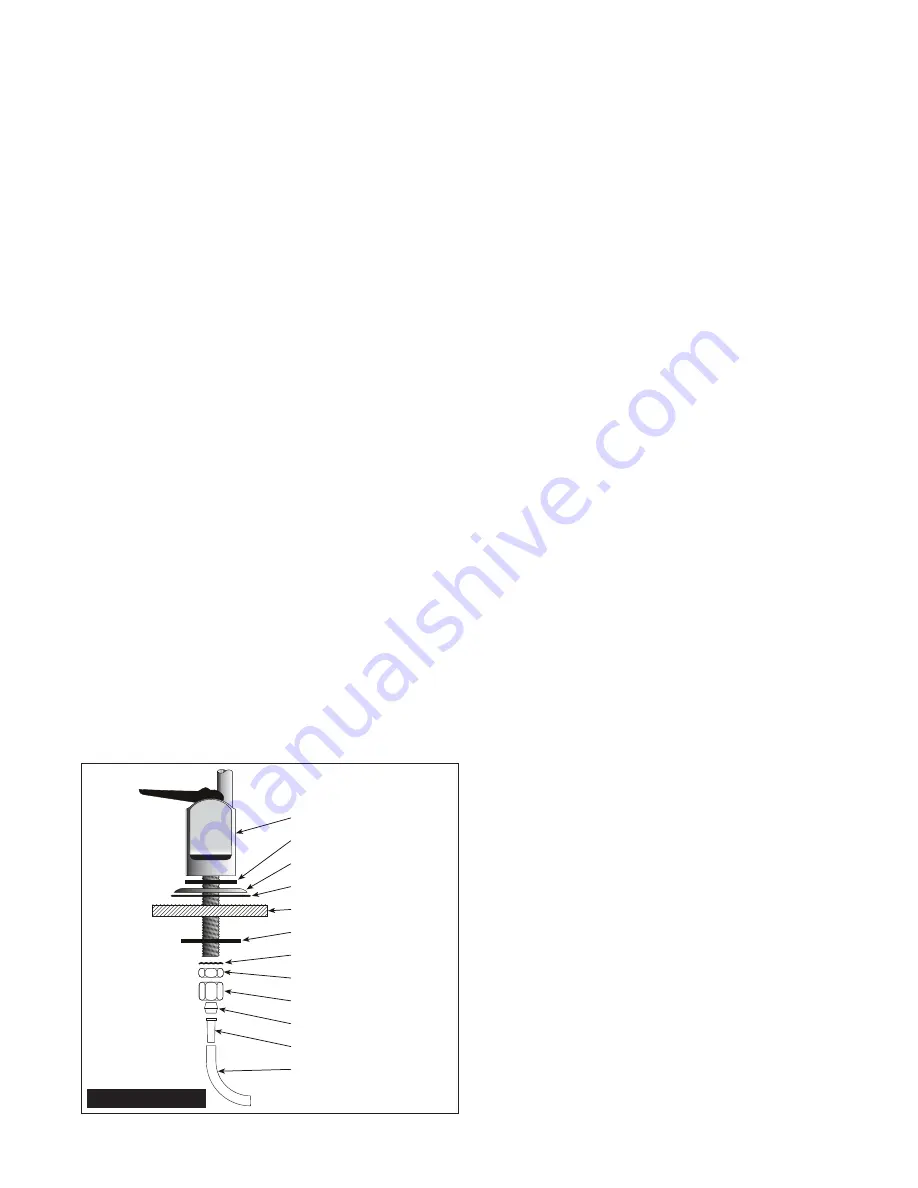
E. Prepare The Appliance For
Installation
Open shipping carton and remove com
po nents.
Check that all installation parts are present which
includes the purification assembly, storage tank,
fau cet, installation hard ware and tubing.
Check that the air supply in the empty tank is ap -
prox i mate ly 7 psi. Adjust if necessary.
SECTION III: INSTALLATION STEPS
All plumbing should be done in accordance with
state and local plumbing codes.
NOTE: Some codes may require installation by a
licensed plumber; check with the local plumbing
au thor i ty prior to installation.
In restricted under-sink areas, it may be easier to
install the faucet first. Allow adequate tubing
lengths for any final component position.
A. Install The Faucet
See Figure 1 for Faucet Installation Diagram
The customer should be consulted before de ter min -
ing faucet location. The faucet should be po si tioned
so that it empties into the sink and the spout
swivels freely for con ve nience.
If the sink already has a hole provided that can ac -
com mo date the RO faucet, then no drilling is re
-
quired and you can proceed to the section on mount-
ing the faucet.
1. Make The Faucet Mounting Hole
IMPORTANT: It is mandatory that safety glass es
be worn during sink hole drilling operations to pre -
vent eye injury.
Before starting the hole making operation, always
check below the sink so that nothing interferes with
mount ing the faucet such as reinforcing ribs,
support brack ets or cabinet construction.
STAINLESS STEEL SINK:
Recommended tools:
• Center punch
• Variable speed drill and high speed drill bits.
• Greenlee chassis punch 7/8" hole size (alternate
9/16" size may be used for non air gap faucet)
• Protective gloves
Procedure:
a) Center punch a small indent at the desired
faucet lo ca tion.
b) Slowly drill the required pilot hole for the
chassis punch.
c) Set up the chassis punch per in struc tions and
tighten nut to cut the desired hole size.
d) Clean up sharp edges with a file if necessary.
PORCELAIN/ENAMEL/CERAMIC ON SHEET
MET AL OR CAST IRON BASE:
Recommended tools:
• Variable speed drill
• Relton porcelain cutter tool set 7/8" size (al ter -
nate 9/16: size may be used for air gap or non
air gap faucet)
• Plumber’s putty
It is important to understand what is in volved in
this procedure. First, the glassy layer of porcelain
must be penetrated through to the base metal.
Second, a center disc of porcelain must be re moved
while pro tect ing the sur round ing porcelain against
chip ping or fracturing. Third, the base metal must
be drilled through to com plete the hole.
Procedure:
a) Mark the center for the 7/8" hole
b) Form shallow putty dam around hole area
and fill with enough water to lubricate carbide
drill bit.
c) Carefully drill pilot hole through por ce -
lain/enam el and base metal using carbide type
pilot drill.
Faucet
Rubber washer
Chrome base plate
Rubber washer
Sink/countertop
Plastic washer
Star washer
Hex nut
Compression nut
Plastic ferrule
Plastic tubing insert
1/4" white tubing
FIGURE 1
Summary of Contents for OmniRO
Page 1: ...Drinking Water Systems Reverse Osmosis Installation Manual...
Page 12: ......