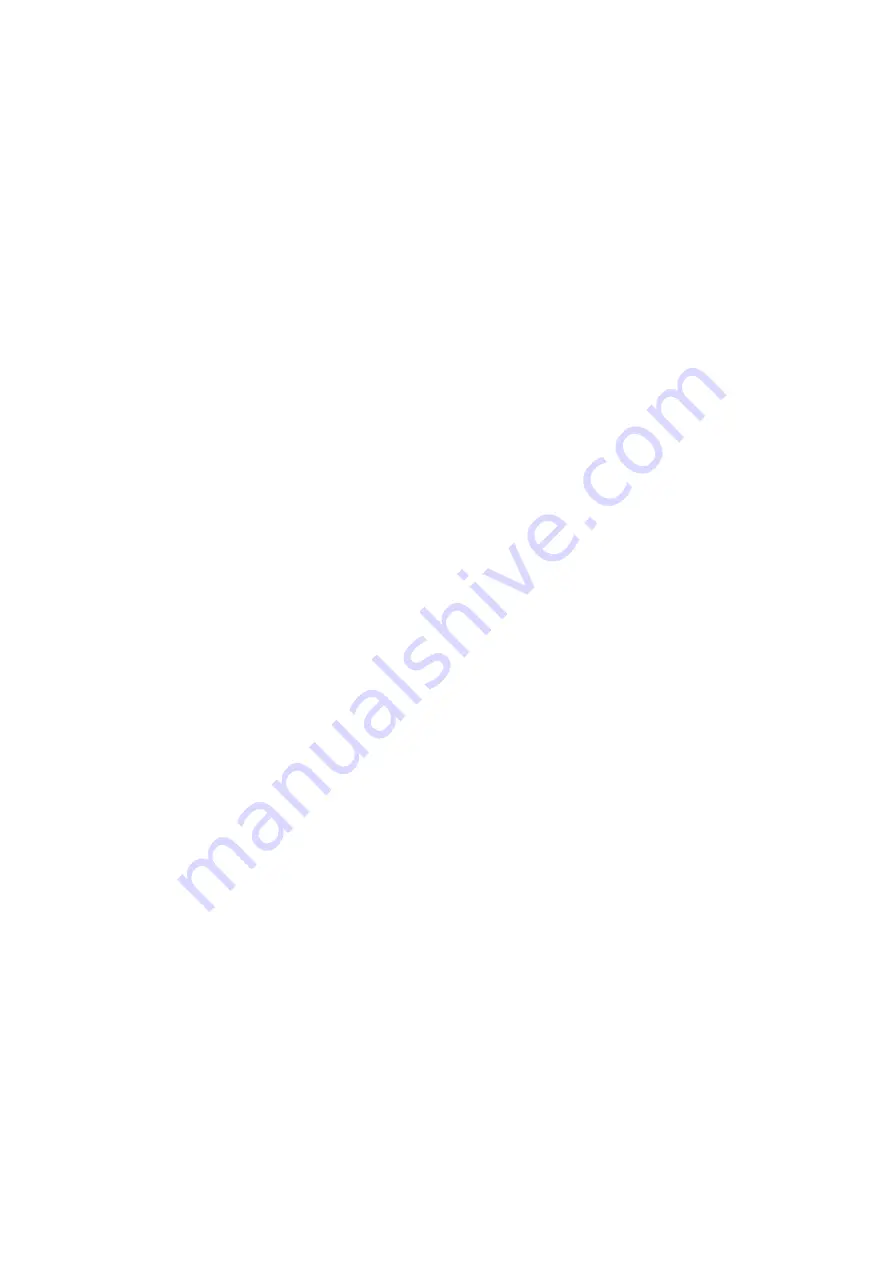
General
1. Preparations before blasting. All parts to be
blasted must be free of oil, grease and moisture.
Make sure the parts are dry before placing them
in the cabinet.
2. Pressure. Normal working pressure is between
3.5 to 5.5 bar. Up to 8.6 bar can be used, but at
such a high pressure destroys certain blasting
materials such as glass balls. Normally the
pressure is set to 5.5 bar, this is suitable for
most materials. For materials such as steel,
aluminum or fragile surfaces you start at a
lower pressure and increase if necessary until
you reach a desired effect.
3. The angle and distance of the blasting gun. Aim
the gun at a 45˚ to 60˚ angle at the object. Let
the ricochets that face the back of the cabinet.
Do not hold the gun at a 90˚ angle to the object
as the blasting material will then bounce back
against the gun and reduce the blasting jet. It
also wears on the parts of the pistol and on the
sight box. Keep the gun at a distance of about
15 cm. Warning. The pistol must always point
away from the operator towards the object to be
blasted. Never blast with the cabinet door
unlocked or open. Always remove the air
connection during maintenance and service of
the appliance.
4. Blast media. The blast media must always be of
good quality and dry. Moisture causes the blast
media to flow less and clog intake pipes, hoses
and containers.
5. The size of the nozzle. By increasing the
diameter of the nozzle, the felling can be
increased significantly, but this requires
increased air flow (the compressor must be able
to provide this).
Increase operational reliability through
preventive measures
The most common problem for a user with their
blasting equipment is that production capacity
decreases. A well-maintained blasting cabinet will
be able to provide the user with many years of
constant service. When production decreases, the
operator can usually find the cause of the problem
by checking the following:
1. Air supply.
If the pressure gauge shows a
satisfactory unloaded value (the blast gun is not
activated), activate the blast gun and check the
pressure gauge, if the pressure drops
significantly it indicates that the air supply is not
Maintenance
1. The blasting gun.
After 10-12 hours of use,
check the nozzle. If the nozzle wears unevenly,
turn it 1/4 turn after 10 hours of use.
2. Lumping of blast media.
Lump formation is caused by moisture in the air
supply or from parts that are greasy or oily. If
not remedied, the blast media will flow unevenly
and eventually clog the intake manifold or gun.
Check the air supply, install an effective
moisture trap if necessary. Degrease parts to be
blasted properly before blasting.
3. Reverse pressure.
If the blast media
sometimes stops, hold the nozzle on the gun
and press the trigger for a few seconds. This
causes the air to be forced out backwards and
the blast hose is cleaned. In this way, clogging
can be easily removed.
4. The blast gun drops in pressure.
Set the
regulator to 5.5 bar, activate the blast gun and
check the pressure gauge, if the pressure drops
significantly it indicates that the air supply is not
sufficient. This may be because the hose has a
too small diameter, a reducing quick coupling,
a clogged filter or a compressor that does not
provide sufficient flow. The air hose should be
1/2 ”or larger.
5. Poor visibility - extremely dusty.
The air
intake must be free of objects and must
allow air to enter the cabinet. The dust collector
container may be full and needs to be emptied
(open the lid at the bottom of the dust collector
to empty the container). The dust filter in the
dust collector may be clogged or need to be
replaced. The blast media can be consumed and
consists mostly of dust particles, empty out and
replace the agent, clean dust separators and
filters.
6. Poor visibility - the window is dusty.
The window has a clear protective film
mounted. Gradually, the film will wear down,
then replace it with a new one. By using
protective film, the life of the sight window can
be extended. Be sure to tape properly when
installing a new protective film, otherwise dust
will come in and settle between the glass and
the film.
7. Poor flow of blast media.
Check that there
is no moisture in the cabinet, install a moisture
separator if necessary, replace a damp blast
media and clean hoses and nozzles. Look for
any holes in the hoses, replace if
necessary. Debris in the blast media, be careful
not to put any paper in the media, this easily
causes nozzles and hoses to become clogged.
Replace or sift the blast media.
Summary of Contents for 502331
Page 1: ...Bl stersk p med trycktank Sandblast Cabinet Item No 502331...
Page 11: ......
Page 12: ......
Page 13: ......
Page 14: ......
Page 15: ......
Page 16: ......
Page 17: ......
Page 18: ......
Page 28: ......
Page 29: ......
Page 30: ......
Page 31: ......
Page 32: ......
Page 33: ......
Page 34: ......
Page 35: ......