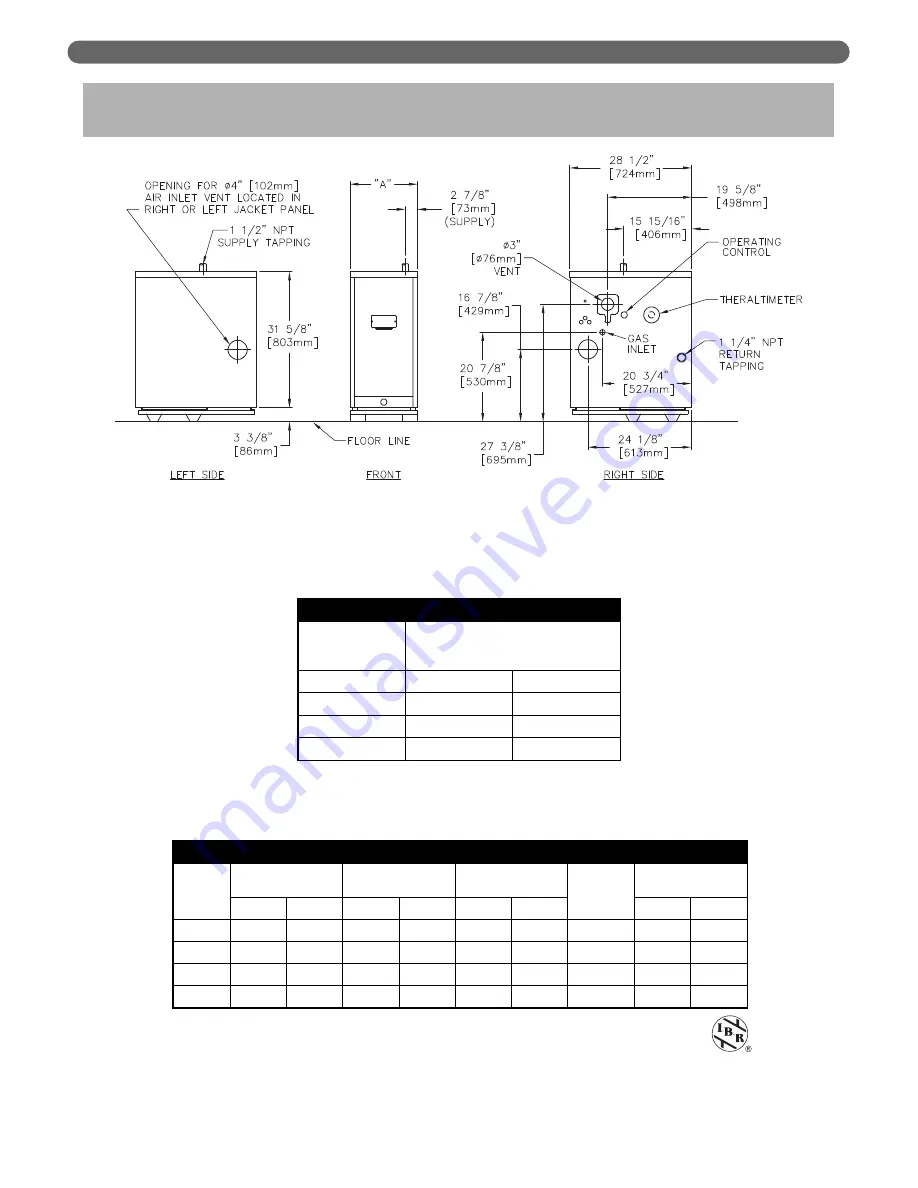
31
BOILER DIMENSIONS & RATINGS
10. BOILER DIMENSIONS & RATINGS
Figure 10.1: Boiler Views
Table 10.1: Series PSC II™ Boiler Dimensions
Table 10.2: Series PSC II™ Boiler Ratings
1 Net I=B=R water ratings based on an allowance of 1.15.
2 Consult factory before selecting a boiler for installations having unusual piping and pickup
requirements, such as intermittent system operation, extensive piping systems, etc.
3 Heating Capacity and Annual Fuel Utilization Efficiency (AFUE) ratings are based on U.S.
Government test.
SERIES PSC II™ BOILER DIMENSIONS
Boiler
Model
Number
Jacket Width “A”
PSCII-03
12-1/2"
318 mm
PSCII-04
15-7/8"
403 mm
PSCII-05
19-1/4"
489 mm
PSCII-06
22-5/8"
575 mm
SERIES PSC II™ BOILER RATINGS
Boiler
Model
Number
Input
DOE Heating
Capacity
3
Net I=B=R
Ratings Water
1,2
Seasonal
Efficiency
3
(AFUE)%
Water Content
MBH
kW
MBH
kW
MBH
kW
Gallon
Liter
PSCII-03
65
19
56
16
49
14
86.0
4.72
17.87
PSCII-04
90
26
77
23
67
20
85.0
6.00
22.71
PSCII-05
120
35
102
30
89
26
85.0
7.28
27.56
PSCII-06
150
44
128
37
111
32
85.1
8.56
32.40
Summary of Contents for PSC II Series
Page 19: ...17 ELECTRICAL Figure 6 3 Ignition System Operating Sequence ...
Page 20: ...18 ELECTRICAL Figure 6 4 Zone Wiring with Zone Valves Figure 6 5 Zone Wiring with Circulators ...
Page 23: ...21 START UP PROCEDURES Figure 7 3 Operating Instructions ...
Page 32: ...30 MAINTENANCE Figure 9 2 Inspection of Flueways Burners and Vent System ...
Page 36: ...34 REPAIR PARTS Figure 11 2 ...
Page 38: ...36 NOTES ...
Page 39: ...37 NOTES ...