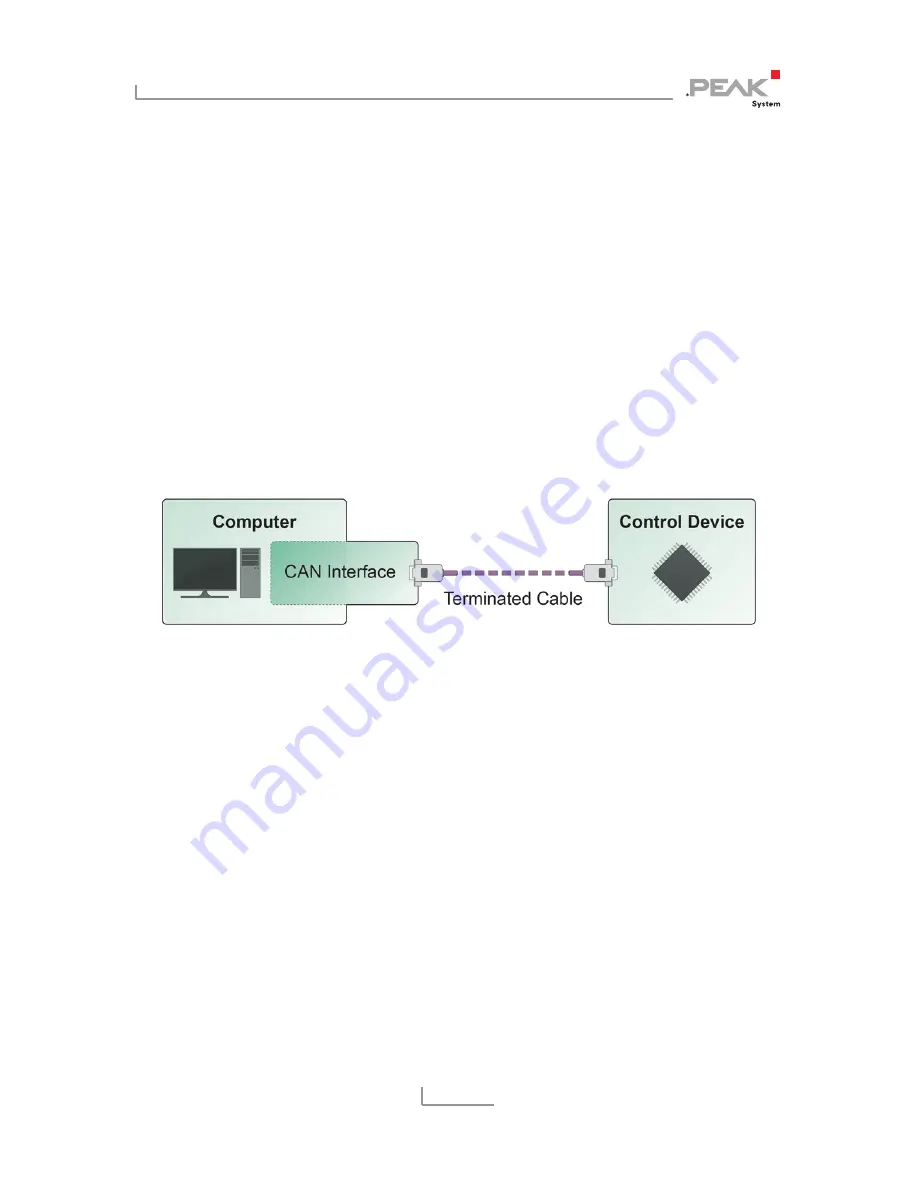
PCAN-miniPCIe – User Manual
10
3.2
Cabling
3.2.1
Termination
A High-speed CAN bus (ISO 11898-2) must be terminated at both
ends with 120 Ohms. Otherwise, there are interfering signal reflec-
tions and the transceivers of the connected CAN nodes (CAN
interface, control unit) do not work.
The PCAN-miniPCIe card does not have an internal termination. Use
the adapter on a terminated CAN bus.
3.2.2
Example of a Connection
Figure 5: Simple CAN connection
This example shows a connection between the PCAN-miniPCIe card
and a control unit. The connection cable is terminated with 120
ohms at both ends.