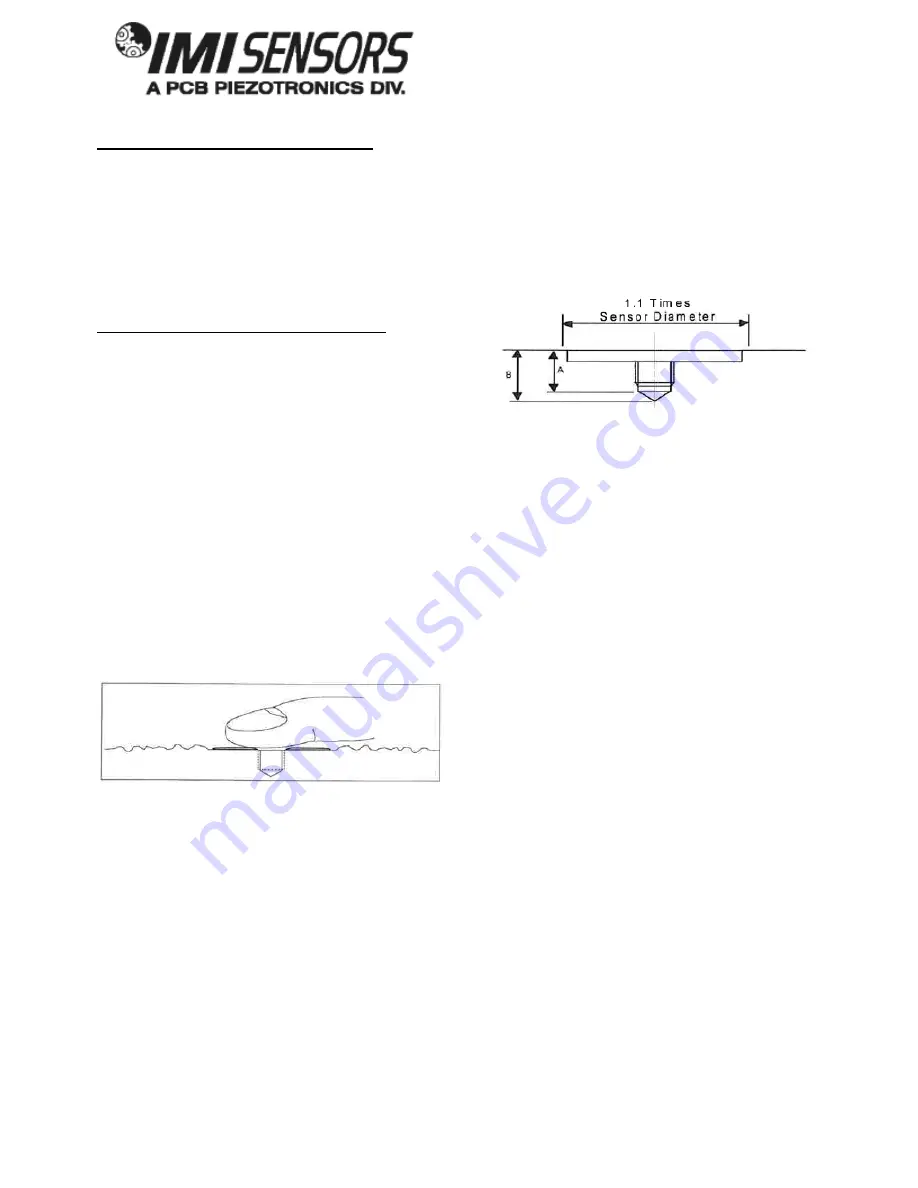
PAGE 10
Standard Stud Mount Procedure
This mounting technique requires smooth, flat contact surfaces for proper operation and is recommended for
permanent and/or secure installations. Stud mounting is also recommended when testing at high frequencies.
Note:
DO NOT attempt mounting on curved, rough or uneven sufaces, as the potential for misalignmen and
limited contact surface may significantly reduce the senor
’s upeer operating frequnecy range.
Figure 6
– direct adhesive mounting
1/4-28 stud 1/4-28 Captive Screw-*
A (in) 0.250 0.250
B (in) 0.350 0.350
Torque (ft-lb) 2 to 5 2 to 5
STEP 1
First, prepare a smooth, flat mounting surface, and then drill and tap a mounting hole in the center of this
area as shown in Figure 6. A precision-machines mounting surface with a minimum finish of 63 µin [0.0016 mm] is
recommended. (If it is not possible to properly prepare the machine surface, consider using an adhesive mounting
pad as a possible alternative.) Inspect the area, checking that there are no burrs or other foreign particles
interfering with the contact surface.
STEP 2
Wipe clean the mounting surface and spread on a light film of grease, oil or similar coupling fluid prior to
installation.
Figure 7
– mounting surface lubrication.
Adding a coupling fluid improves vibration transmissibiliy by filling small voids in the mounting surface and
increasing the mounting stiffness. For semi-ermanent mounting, substitue epoxy or another type of adhesvie.
STEP 3 HAND
–
tighten the sensor/mounting stud to the machine, then secure the sensor with a torque wrench
to the mounting surface by applying the recommended mounting torue ( see enclosed specification data sheet for
proper mounting torque). It is important to use a toque wrench during this step.
Under-toruing the sensor may
not adequately couple the device; over-torquing may result in stud failure and possible permanent
damage.