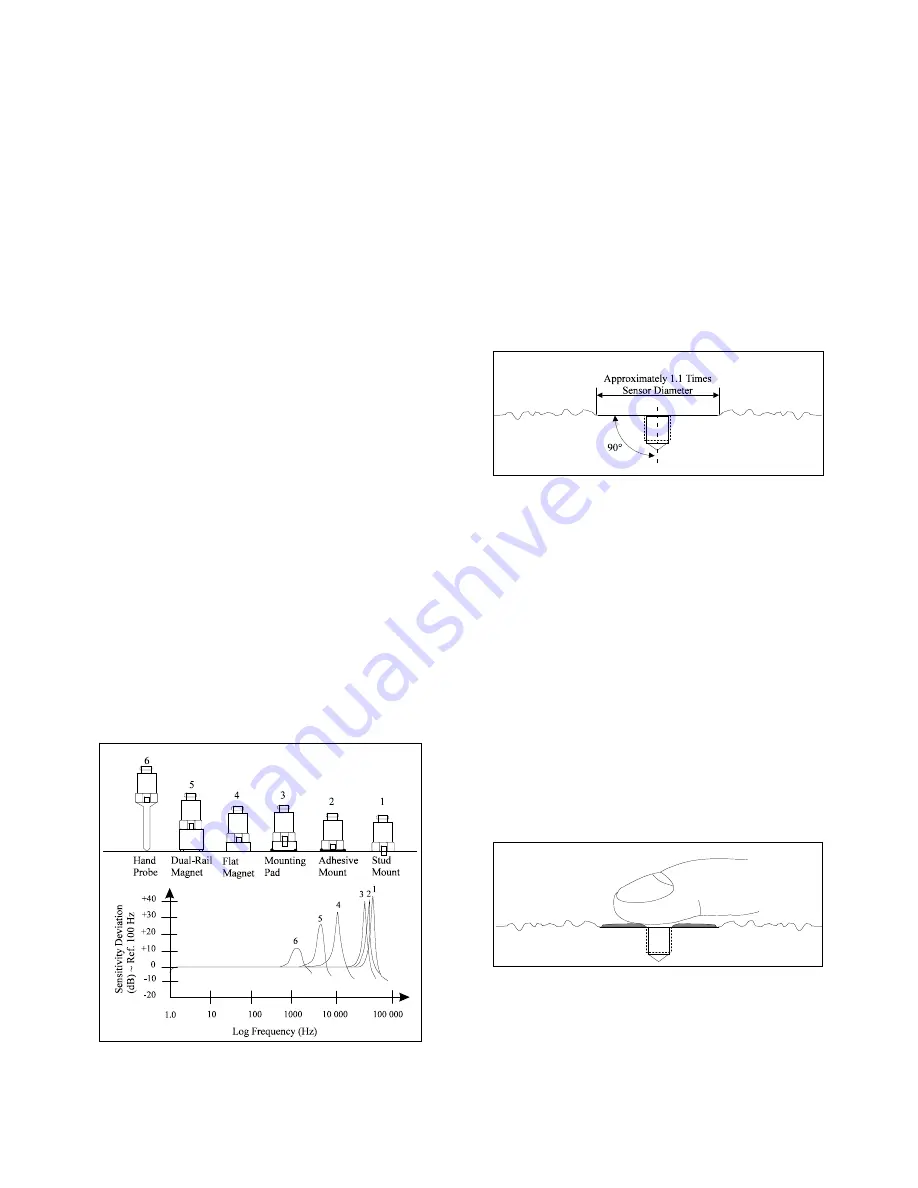
MANUAL: 55308
REV: A
ECO: 49582
5
For optimum performance and measurement find a
rigid location on the machine casing that most
accurately represents the vibration of the rotor,
bearing, fan, etc. to be measured.).
3.4 Mounting Sensor
When choosing a mounting method, consider closely
both the advantages and disadvantages of each technique.
Characteristics like location, ruggedness, amplitude
range, accessibility, temperature, and portability are
extremely critical. However, the most important and
often overlooked consideration is the effect the mounting
technique has on the high-frequency performance of the
accelerometer.
Shown hereafter are six possible mounting techniques
and their effects on the performance of a typical
piezoelectric accelerometer. (Note that not all of the
mounting methods may apply to your particular sensor.)
The mounting configurations and corresponding graph
demonstrate how the high-frequency response of the
accelerometer may be compromised as mass is added to
the system and/or the mounting stiffness is reduced.
Note:
The low-frequency response is unaffected by the
mounting technique. Its roll-off behavior is dependent
upon the coupling type or time constant of the external
charge amplifying device. This characteristic may be
fixed or adjustable, depending on the charge amplifier.
Please refer to the appropriate charge amplifier
specification sheet for information on low-frequency
characteristics.
Figure 1.
Assorted Mounting Configurations and Their
Effects on High Frequency
3.4.1 STUD MOUNT
This mounting technique requires smooth, flat contact
surfaces for proper operation and is recommended for
permanent and/or secure installations. Stud mounting is
also recommended when testing at high frequencies.
Note:
Do NOT attempt mounting on curved, rough, or
uneven surfaces, as the potential for misalignment and
limited contact surface may significantly reduce the
sensor’s upper operating frequency range.
Figure 2.
Mounting Surface Preparation
STEP 1:
First, prepare a smooth, flat mounting surface,
then drill and tap a mounting hole in the center of this
area as shown in Figure 2 and in accordance with the
Installation Drawing
for the specific sensor that is being
mounted
.
A precision-machined mounting surface with a minimum
finish of 63
in (0.00016 mm) is recommended. (If it is
not possible to properly prepare the test structure
mounting surface, consider adhesive mounting as a
possible alternative.) Inspect the area, checking that there
are no burrs or other foreign particles interfering with the
contact surface.
STEP 2:
Wipe clean the mounting surface and spread on
a light film of grease, oil, or similar coupling fluid prior
to installation.
Figure 3.
Mounting Surface Lubrication
Adding
a
coupling
fluid
improves
vibration
transmissibility by filling small voids in the mounting
surface and increasing the mounting stiffness. For semi-