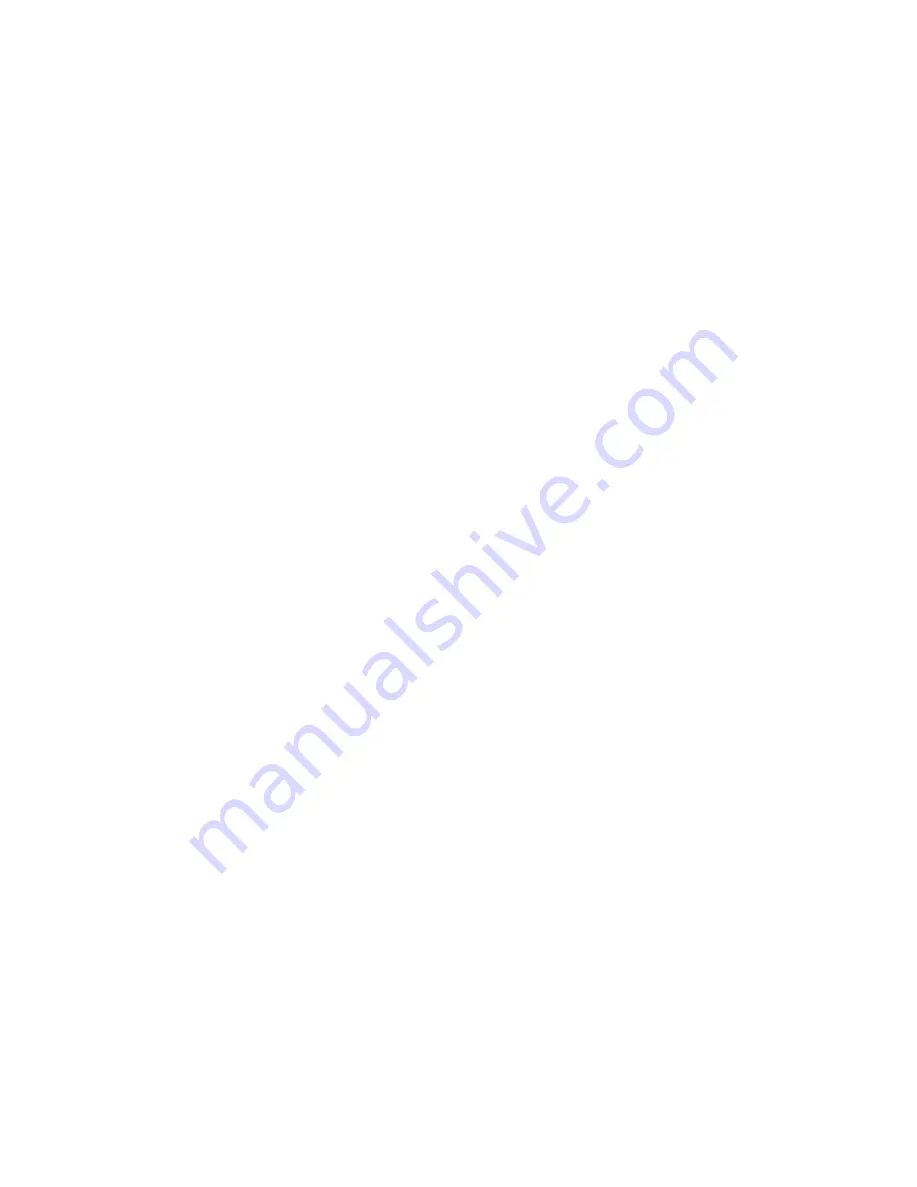
6
The Modal Punch can be calibrated by hitting a freely-suspended mass instrumented with
a quartz reference accelerometer. The mass, pendulously suspended or placed on a piece
of foam rubber, will behave as a rigid body. According to Newton
’
s second law of
motion, at any instant in time, the force experienced by the mass is simply the mass
multiplied by the measured acceleration.
On a storage oscilloscope, dividing the peak output signal of the hammer (mV) by the
mass (lb) times the peak acceleration (g
’
s) gives the hammer sensitivity directly in
mV/lb. Calibration on a FFT analyzer produces the same result as a function of
frequency. The transfer function of acceleration versus force produces a calibration
constant (ideally 1/M) at each discrete frequency. This calibration curve is linear over a
specified frequency range.
PCB
®
’
s Model 963A Gravimetric Calibrator is ideally suited for calibration of the Modal
Punch. The device calibrates accelerometers, force sensors, and PCB
®
Impulse Force
Test Hammers and tests the functional transfer behavior, sensitivity, and phase of sensor
structures.
7.0 Maintenance
The rigid construction of the Modal Punch is designed to provide reliable, long-term
service life. Problems may arise when the instrument is exposed to temperatures
exceeding the specific range, prolonged exposure to moisture, or extremely high
mechanical shock. There are no user-serviceable components in the Modal Punch, so
users should not attempt to make repairs to the unit (and doing so will void the unit
’
s
warranty).
Should service be required, the Modal Punch should be returned to the factory, along
with a description of the problem, in order to expedite the repair process. Before sending
the Modal Punch back to the factory for service, PCB recommends that all cables and
connections be checked to verify that they are not the cause of the problem.
8.0 Cautions
Although the Modal Punch is rugged in construction, personal injury or damage to the
unit may result from misuse. When observed, the following precautions can ensure long
service life and safe, accurate data acquisition:
1). Do not attempt to dismantle the sensor element from the Modal Punch structure. All
service should be performed at the factory.
2). Never generate more than five times the rated impact force range for the Modal
Punch. In general, observe the maximum force rating for a 10V output. 100 volts will
destroy the precision built-in micro-electronics and/or the sensing element.
Summary of Contents for 088A
Page 14: ......