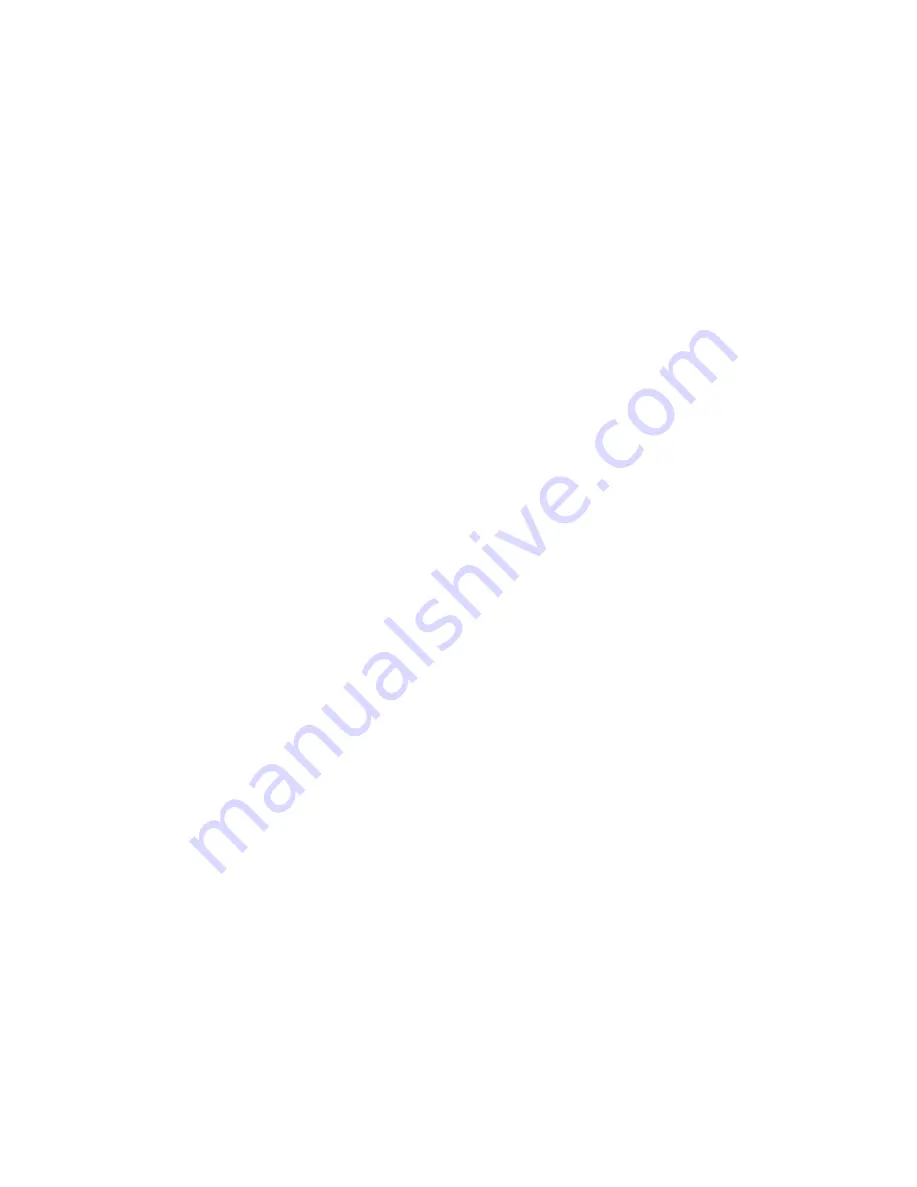
5
C. To increase signal energy of impact, increase the impact velocity and/or
hammer mass.
5). Repeat steps 1 through 4 until satisfactory results are obtained.
Generally speaking, the impact tips affect the impulse frequency content, while the mass
of the impact device and velocity of impact affect the signal energy level. Frequency
content and energy level are interrelated. Therefore, both will be affected by different
hammer structures and Modal Punch configurations. Hammer velocity at impact will
also affect both. In general, massive structures with lower stiffness require the use of a
soft impact tip and large mass to adequately excite low frequency resonances.
During testing, occasionally check and tighten the electrical and mechanical connections.
Repeated impacting may loosen connections, which may result in erratic, noisy signals.
Multiple impacts or penetration into the structure may occur when using too heavy a
mass on too light a structure. This will appear as a series of peaks of decreasing
amplitude in the time history data. Reject such data. Careful techniques used in the
impact process can avoid this problem. In particular, if the Modal Punch is held against
the test structure and allowed to freely recoil after impact, the double impact phenomena
will be reduced or eliminated. Some skill and practice may be required to perfect this
technique.
Distortion, undershoot, and oscillation of the analyzer display is caused by ringing of the
analyzer
’
s anti-aliasing filters. This behavior is normal. To view the correct impulse
waveform, switch the analyzer to a higher frequency range.
6.0 Calibration
Calibration involves testing the functional transfer behavior (sensitivity) of the sensor
under controlled laboratory conditions. Sensitivities to various inputs such as force,
temperature, current, and frequency can be derived by relating the corresponding output
to changes in these inputs. For impact hammers and the Modal Punch, the most
important of these relationships is the sensitivity to the force input. The desired behavior
is linear, since ideal sensors treat output and input amplitudes proportionally. In addition,
the nominal sensitivity should be constant (linear frequency response) within the specific
frequency range, and there should be no induced phase shift in the response (no delay in
the signal).
Different Modal Punch and hammer combinations have different sensitivities because the
structure experiences a force greater than the crystal-sensing elements. The force of
impact on the test structure is a function of the total mass of the Modal Punch and
hammer, while the force on the crystals is a function of the mass behind them. The
impact tip is located in front of the crystal. The differences in mass depend on the ratio
of the tip mass to the mass behind the crystal. This is automatically compensated for
when the Modal Punch is properly calibrated.
Summary of Contents for 088A
Page 14: ......