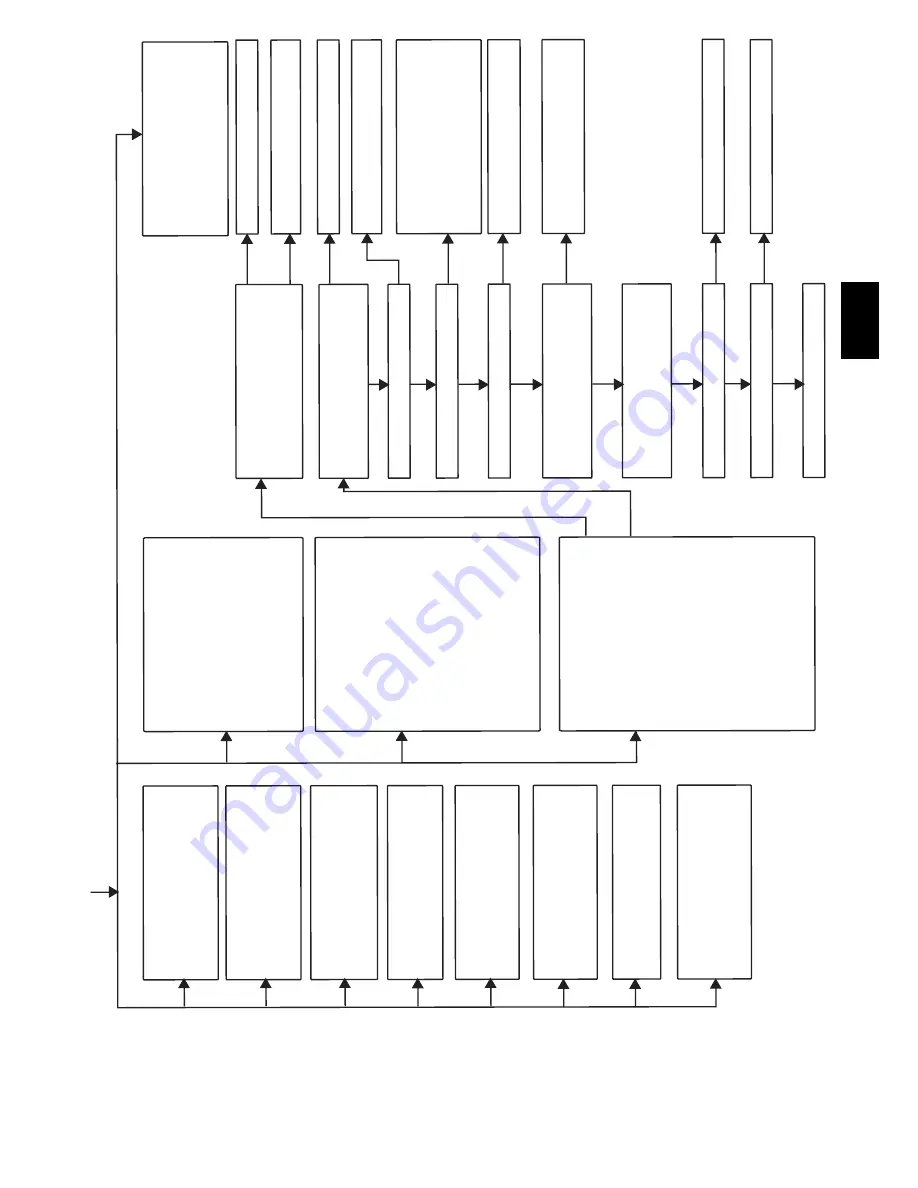
17
11
NO PREVIOUS CODE – Stored codes
are
erased
after 72 hours
. On RED LED
boards stored status codes can also b
e
erased whene
v
er po
wer (115V or 24V
)
is interr
upted.
Run system through
a
heating or cooling cycle to
chec
k system.
12
BLO
WER ON AFTER PO
WER UP
–
(115V OR 24V) – Nor
mal operation.
Bl
ow
er r
uns f
or 90 seconds
, if unit is
po
wered up during a call f
or heat (R-W
closed) or when (R-W o
pens) dur
ing
th
e
b
lo
w
er on-dela
y per
iod.
1
3
LIMIT CIR
CUIT LOCK
O
UT – Loc
kout
occurs if the limit or flame rollout s
w
itch is
open l
onger t
han 3 minutes
. Control wil
l
auto-r
eset after 3 hours
.
See code 33
.
1
4
IGNITION
LOCK
OUT – System f
ailed to
ignite gas
and pro
v
e
flame in 4
attempts
.
Control will auto-reset after 3 hours
.
See status code 34.
21
GAS HEA
TING LOCK
OUT –
T
u
rn off
po
wer and w
ait 5 minutes to retr
y.
Chec
k f
o
r:
-
S
tuc
k closed g
as v
a
lv
e rela
y
on cont
rol.
-
M
is
wire or shor
t to gas v
alv
e wire
.
2
2
ABNORM
AL FLAME-PR
O
VING
SIGNAL
Flame is pro
v
ed while gas v
alv
e is de-
energiz
ed.
Inducer will r
un until f
ault is
cleared.
Chec
k f
o
r:
-
S
tuc
k open or leaky gas v
a
lv
e
.
23
PRESSURE SWITCH DID NO
T OPEN
Chec
k f
o
r:
-
O
bstr
ucted pressure
tube
.
-
P
ressure s
witch stuc
k closed.
24
SECOND
AR
Y
V
O
LT
A
G
E
FUSE
IS
OPEN
Chec
k f
o
r:
-S
h
o
rt circuit in secondar
y
vo
ltage (24V)
wir
ing including ther
mostat leads
.
D
isconnect ther
mostat leads to isolate
shor
t circuit.
3
1
PRESSURE
SWITCH DID NO
T CLOSE
OR REOPENED – If open longer than
5
minute
s
, inducer shuts off f
or 15 minutes
bef
ore retr
y.
If opens dur
ing b
lo
w
er on-
dela
y
per
iod,
b
lo
w
er will come on
for th
e
selected b
lo
w
er off-dela
y.
Chec
k f
o
r:
-
P
roper v
ent sizing.
-
L
o
w
inducer v
oltage (115V).
-
L
o
w
inlet
gas pressure
(if LGPS used).
-
Inadequate comb
ustion air supply
.
-D
isconnected or obs
tr
ucted pressure
tubing.
-D
ef
ectiv
e inducer motor
.
-D
ef
ectiv
e pressure s
witch.
-
E
xcessiv
e wind.
-R
estr
icted v
ent.
33
LIMIT CIRCUIT F
AU
LT
– Indicates the
limit or flame
rollout s
witch
is
open.
Blo
w
er
will r
un f
or 4 minutes
or until open
sw
itc
h
remak
es whiche
v
er is longer
. If open
longer than 3 minut
e
s
, code changes to
loc
k
out #13.
If open less than
3 min.
status code #33 continues to flash un
til
b
lo
w
er shuts off
. Flame rollout s
witch
requires manual reset.
Chec
k f
o
r:
-
D
ir
ty filter or restr
icted duct system
.
-
Loose b
lo
w
er wheel.
-
D
ef
ectiv
e s
witch or conn
ections
.
-D
ef
ectiv
e b
lo
w
er motor or capacitor
.
-
Inadequate comb
ustion air su
pply
(flame rollout s
witch open).
-R
estr
icted v
ent.
-
P
roper v
ent sizing.
-
E
xcessiv
e wind.
- Blo
w
er motor on incorrect speed tap
.
- Input rate to fur
nace set too high.
34
IGNITI
ON PR
O
V
ING
F
AILURE
– If
flame
is not sensed dur
ing the tr
ial f
or ignition
per
iod,
the control will repe
at the ignition
sequence 3 more times bef
ore lo
ck
out
#14 occur
s
. If flame signal is lost dur
ing
the b
lo
w
er on-dela
y per
iod, b
lo
w
er wil
l
come on f
o
r the selected
b
lo
w
er off-dela
y.
Chec
k the f
ollo
w
ing items first bef
ore
proceeding to
the ne
xt step
.
-
G
as v
alv
e tur
ned off
.
-
M
anual shut-off v
alv
e
.
-G
reen/Y
ello
w
wire
MUST be connected
to fur
nace sheet metal
.
-
F
lame sensor m
ust not be grounded.
T
o
deter
mine whether the prob
lem is in
the gas v
a
lv
e
,
igniter
, or flame sensor the
system can be operated
in the component
test mode to chec
k the ignit
er
. First
remo
ve
the R ther
mostat connection from
the control and initiate the component
test sequence
. Does the igniter gl
ow
orange/white
b
y
the end of the 15 second
w
a
rm
-up per
iod?
Unplug igniter har
ness
from control and initiate
another component
test sequence
. Chec
k
for 115V between
pin 1 and
NEUTRAL-L2
on
the control.
W
as 115V present f
or the 15
second per
iod?
Reconnect the R the
rm
ostat lead and set
ther
mostat to call f
o
r heat.
Connect
v
o
ltmeter
across gas v
a
lv
e
connections
. Does gas v
a
lv
e
receiv
e 24V?
Does gas v
alv
e open and allo
w
gas to flo
w
?
Do the main b
ur
ners ignite?
Do the main b
ur
ners sta
y on?
Repeat call f
or heat and chec
k flame sensor
current dur
ing tr
ial f
or ignition per
iod.
Is the
DC microamps bel
ow
0.5?
Is current near typical v
alue?
Will main b
ur
ners ignite and sta
y on?
Fix
ed.
Clean flame
sensor with fine steel wool and
rechec
k current.
Nominal current i
s 4.0 to 6.0
microamps
.
45
CONTR
O
L CIRCUITR
Y LOCK
OUT
A
uto-reset after 1 hour lo
c
k
out due to:
-
F
lame circuit f
ailure
.
-
G
as v
alv
e rela
y stuc
k open.
-
S
oftw
are chec
k error
.
Reset po
wer to clear lo
c
k
out.
Replace
control if code re
peats
.
Replace fur
nace control
.
Chec
k
fo
r
continuity in the
har
n
ess
and
ignit
er
.
Replace def
ectiv
e component.
Chec
k connections
. If OK, replace control
.
Chec
k that all gas v
alv
es are tur
ned on.
Replace v
al
ve
.
Chec
k f
o
r:
-
Inadequate flame carr
yov
er or rough
ignition.
-
L
o
w
inlet gas pressure
.
-
P
roper fir
ing rate
.
Allo
w
b
lo
w
er to come on and repeat test to
chec
k f
or inter
mittent operation.
Chec
k connections and retr
y.
If current is
near typical
v
alue (4.0-6.0
nominal) and
b
u
rners will not sta
y on, replace
control.
Replace electrode
.
Replace fur
nace control
.
YES
YES
YES
YES
NO
YES
YES
YES
NO
YES
NO
NO
NO
YES
NO
NO
NO
NO
A05096
PG
9M
AB