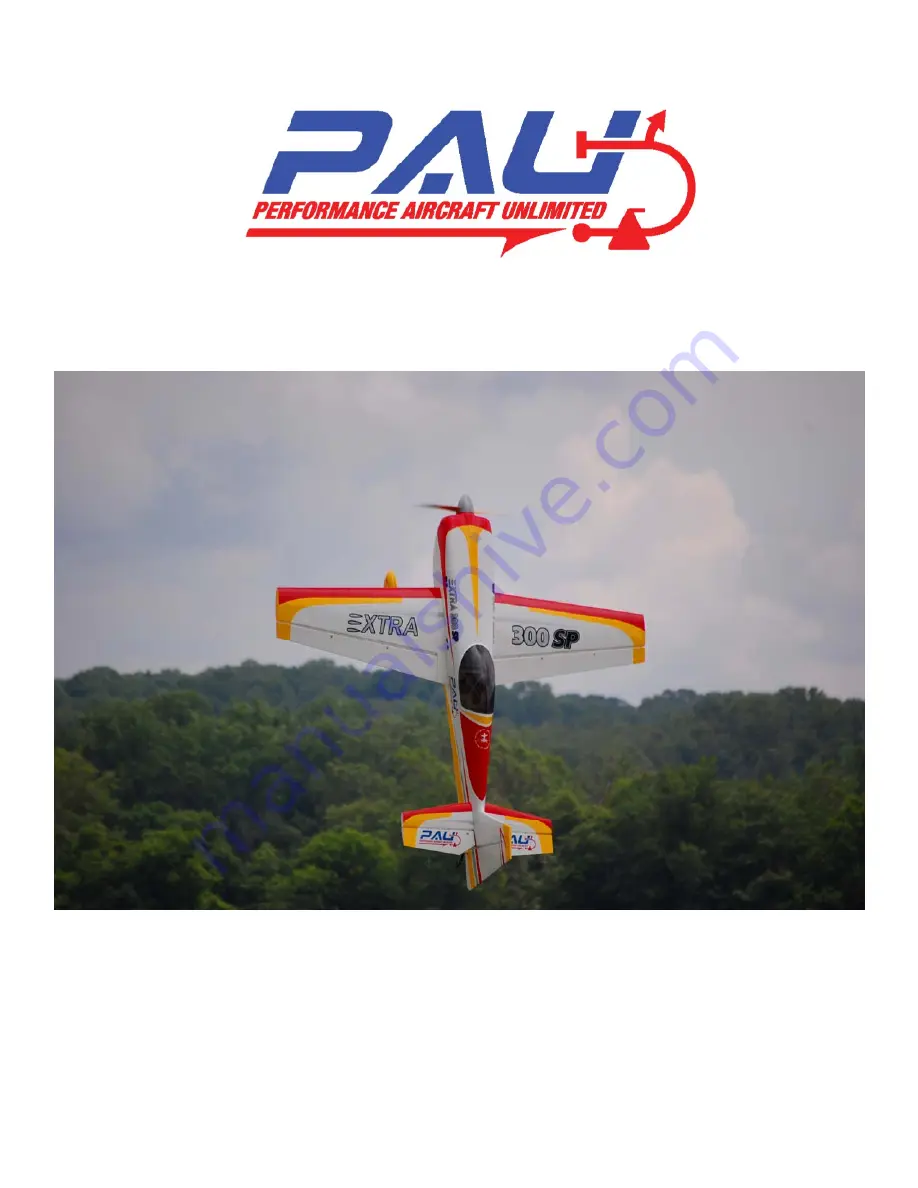
1
100cc Extra 300-SP ARF
Instruction Manual
Congratulations and thank you for purchasing the Performance Aircraft Unlimited 105” Extra 300SP. The Extra
is arguably one of the most renowned aerobatic aircraft ever produced. Walter Extra who designed the original
Extra, named his aircraft by the horsepower rating of the motor placed in them. The Extra 300SP is one of the
newest releases in full scale, and now in R/C version.
Our aircraft was designed with 1,922sq inches of wing area while keep the total weight to a minimum. Whether
you want an aircraft precise enough to compete in IMAC or 3D until you’re airsick, the PAU Extra fits the bill.
Its light weight gives you the stability in high-alpha to take it to the extremes of the flight envelope. If tumbling