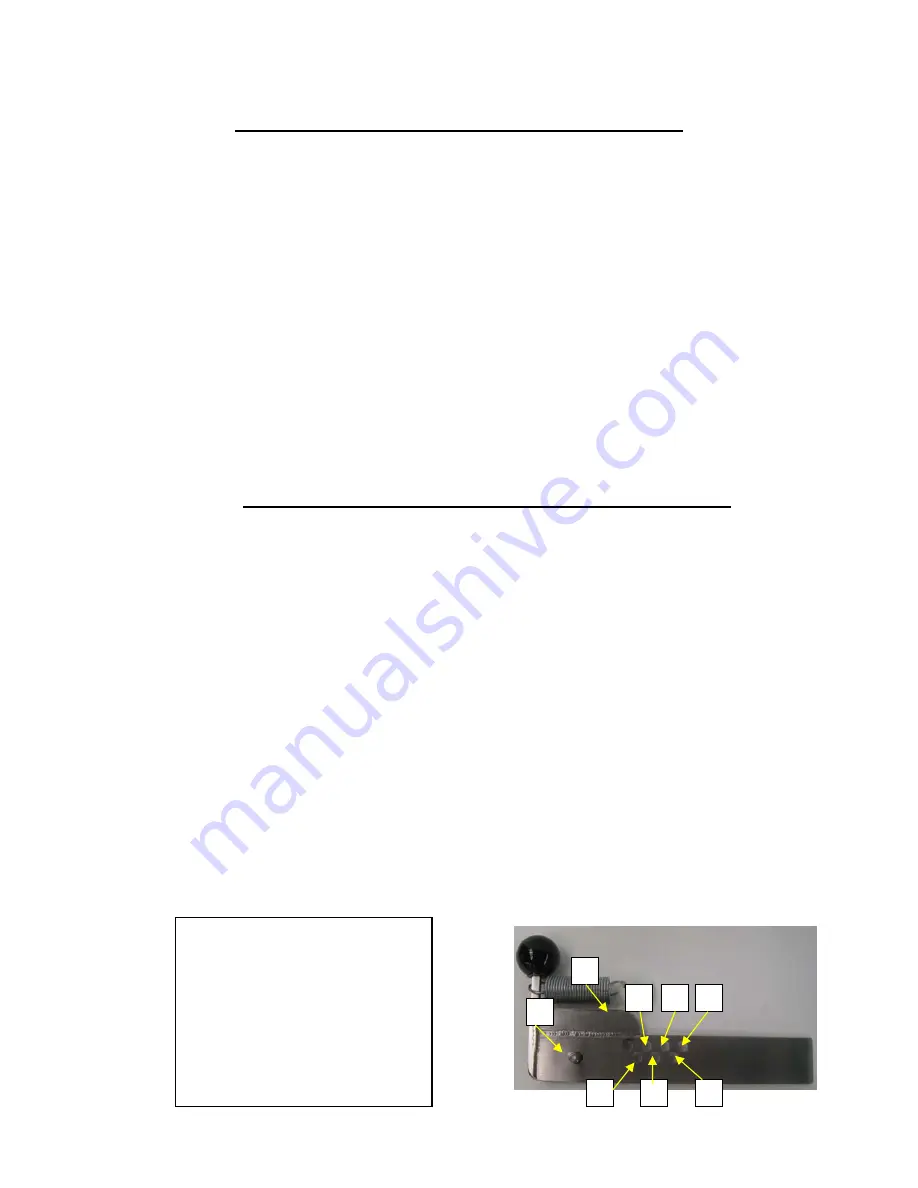
8
Proper Procedure for Operating a Model 330PUB
When the Model 330PUB is fully assembled with all guards secured in their
proper place, put product to be portion molded in the Feed Tray. Push the product
through the holes in the Feed Tray Guard into the Hopper opening.
DO NOT PUT
HANDS OR FINGERS, OR FOREIGN OBJECTS, SUCH AS STOMPERS OR
PLUNGERS INTO THE HOPPER. THERE ARE NO STOMPERS OR
PLUNGERS NEEDED WHEN USING THIS UNIT, THEREFORE NONE ARE
SUPPLIED.
After you allow product to drop into Hopper turn the machine on by
moving the On/Off switch down towards the on position. The machine may need to
cycle a few times to prime the machine with product. As patties are being formed
continue to push product through the holes and under the Feed Tray Guard. Patty paper
may be added to the machine as needed. The machine can hold up to 1 inch of paper at a
time.
As the Mold Plate moves back and forth to form patties, a thin coating of product
may accumulate over its surface. This coating may also accumulate on the edges of the
Knock Out Cup or on the front of the Hopper and Spacer Plate. This accumulation does
occur on all molding machines. It is nothing to be concerned with. There are certain
machine settings that may lessen this accumulation.
Setting the Ring Pin Pressure Plate for your Patty Size
The Purpose of the Pressure Plate is to entrap the amount of product necessary to form
your patty. This part is also used in controlling the firmness of your patty. With the Pressure
Plate set correctly you will in turn have:
- less leakage, oozing, and coating of parts
- less kneading of your product
- and less strain on your machine.
-----------------------------------------------------------
If your patty weight is 8 ounces, keep the ring pin in the storage hole as described in the
picture. This will allow the Pressure Plate to move all the way into the Hopper and stop on the
welded stud which is the maximum volume setting.
If your patty is 4 ounces remove the ring pin from the storage hole and place it in the 4
ounce hole.
If you patty weight is to be 6 ounces, place the ring pin in the 6 ounce hole.
If you would like to have a tightly packed patty, move the ring pin to a higher than
recommended setting for that particular weight. The white collar on the ring pin may be removed
for more fine tuning of patty weight.
THESE ARE ONLY RECOMMENDED SETTINGS. A VARIETY OF CIRCUMSTANCES
MAY CALL FOR YOU TO INSERT THE RING PIN IN A DIFFERENT LOCATION.
1
2
3
4
5
6
7
8
1 - Ring Pin in storage hole
2 - 2 ounce hole
3 - 3 ounce hole
4 - 4 ounce hole
5 - 5ounce hole
6 - 6 ounce hole
7 - 7 ounce hole
8 - 8 ounce welded stop