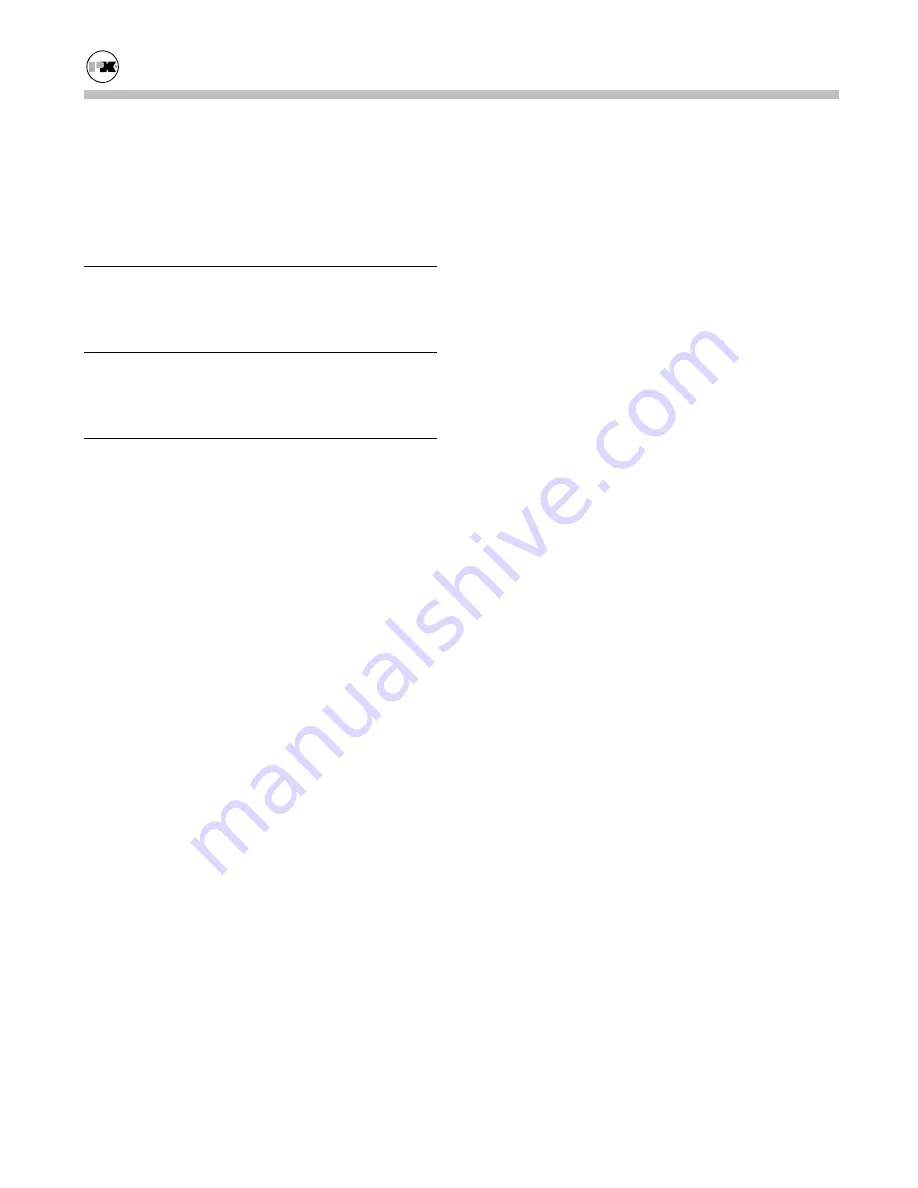
Modu-Fire
®
Gas-Fired Boiler
Maintenance
9. Before re-installing the burner, check the
cleanliness of the heat exchanger and the
condition of the combustion chamber.
5.3
R
EMOVING THE
E
XCHANGER
(Refer To TBIG Latest Edition)
5.4
A
FTER
A
LL
R
EPAIRS OR
M
AINTENANCE
(Refer To TBIG Latest Edition)
5.5
SEQUENCE
OF
OPERATION
5.5.1 STANDARD MODULATING
1. When the On/Off (Main power) switch is turned
on, the switch illuminates. Power is provided to
the flame safeguard control, the temperature
control, and through normally closed contact of
relay-1 to the damper close terminal. Power is
also applied through the “start logic string” a
series of normally closed switches, including
water flow, gas pressure, high stack temp, high
limit temperature, and operating temperature to
the flame safeguard programmer.
2. The water flow limit switch is closed when
there is adequate water flow through the boiler.
Note:
The closing of this switch does not prove
that flow is adequate. Refer to Technical Data
Sheet # TD110 for proper flow requirements.
3. When adequate gas pressure is available, the
low gas pressure limit switch is closed. Manual
reset is required following conditions resulting
in low gas pressure.
4. When the temperature sensed by the high limit
temperature control is below the set limit, the
switch is closed. Manual reset is required
following conditions exceeding high limit
temperature.
5. When heat is required as indicated by the outlet
water temperature, power is applied to Terminal
6 of the programmer, which initiates the burner
ignition and operation sequence.
6. The programmer first energizes Terminal 4
which supplies power to the motor contactor,
the damper motor limit switch, and normally
open contact on relay-2. If the damper motor is
open far enough for purge, the limit switch is
made and relay 2 is energized. This supplies
power to the air flow switch, which initially
shows low air flow with the “LOW AIR”
indicator. This indicator will remain on until
sufficient air flow is sensed. If the damper
motor is not open enough for purge, the limit
switch is not made, relay 2 is not energized and
the combustion sequence does not continue.
7. Once sufficient airflow is indicated by the air
flow switch, Terminal 7 of the combustion
control is energized. This starts the Prepurge
period. The combustion chamber is Prepurged
for 30 seconds.
8. A 10-second “trial for ignition” period is
initiated with both Terminal 8 and 10 being
energized. Terminal 10 of the combustion
control powers the ignition transformer. The
transformer output creates a spark at the igniter.
Terminal 8 powers the pilot gas valve.
9. When a pilot flame is detected by the UV
scanner a signal is sent to the combustion
control. When this signal is detected, Terminal
10 of the combustion control is de-energized,
terminating the spark.
10. After the 10 second “trial for ignition” period,
if pilot flame has been established, Terminal 9
of the Combustion Control is energized. This
opens the main gas valve and energizes the air
gas ratio control. The 10 second Main trial for
ignition” period begins. If pilot flame has not
been established, the unit will lock out on pilot
flame failure.
11. After the 10 second “main trial for ignition
period” if flame has been established, Terminal
8 of the combustion control is de-energized,
closing the pilot valve. Terminal 21 is
energized, energizing Relay-1. If main flame
has not been established, the unit will lock out
on main flame failure.
13
Summary of Contents for THERMIFIC MODU-FIRE
Page 11: ...Modu Fire Gas Fired Boiler Installation 8 Table 1 Table of Parameters ...
Page 20: ...Modu Fire Gas Fired Boiler Parts Technical Support Standard Unit w Siemens Control 17 ...
Page 21: ...Modu Fire Gas Fired Boiler Parts Technical Support Standard Unit w Remote Control 18 ...
Page 22: ...Modu Fire Gas Fired Boiler Parts Technical Support IRI with Siemens Control 19 ...
Page 23: ...Modu Fire Gas Fired Boiler Parts Technical Support IRI with Remote Control 20 ...