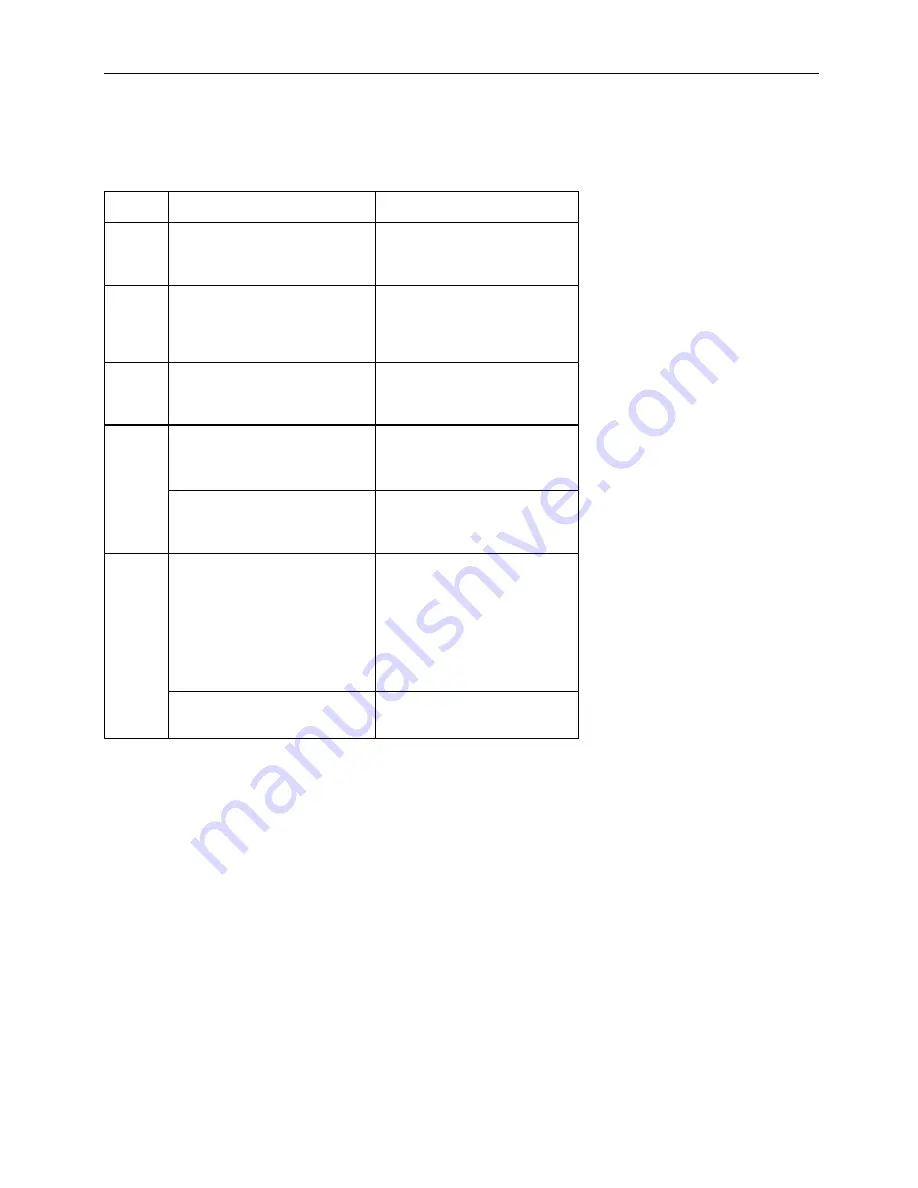
Troubleshooting
Second Edition 03/18/1997 – CSH (con:K2AA V1.0) 031-300-190014_A.doc
17
Operating Errors
Malfunctions in the system that are caused by range exceeding or operating errors by the crane operator
himself are indicated on the display. These error codes are E01, E02, E03, E04, and the crane operator
himself can normally eliminate E05 and them.
Error
Code
Cause
Elimination
E01
Fallen below the minimum
radius or above the angle given
in the load capacity chart due to
luffing up the boom too far.
Luff down boom to a radius or
angle given in the load capacity
chart.
E02
The maximum radius or
minimum angle given in the load
capacity chart was exceeded
due to luffing down the boom
too far.
Luff up boom to a radius or
angle given in the load capacity
chart.
E03
Boom position is out of the
permissible working area (over
front).
Move boom back to the
permissible working area. See
lifting diagram in the load
capacity charts.
E04
Operating mode at the console
incorrectly set.
Correctly set operating mode to
the code assigned to the
operating mode of the crane.
Operating mode is not
permissible with the actual
crane configuration or boom
position
Be sure crane is set up
according to proper operating
configurations.
E05
Boom was telescoped too far or
not far enough, you may only
operate up to a certain
maximum or minimum boom
length or with load curves for
boom extension where you have
to telescope the main boom to a
certain length.
Telescope boom to correct
length, given in the load
capacity chart.
Length sensor adjustment
changed i.e. length sensor cable
slid off the length sensor drum.
For elimination, refer to service
manual.
Summary of Contents for DS 50
Page 2: ......
Page 4: ......
Page 8: ...Operator s Manual DS 50 0002 4 Fig 1 Components of the LMI system PAT DS 50...