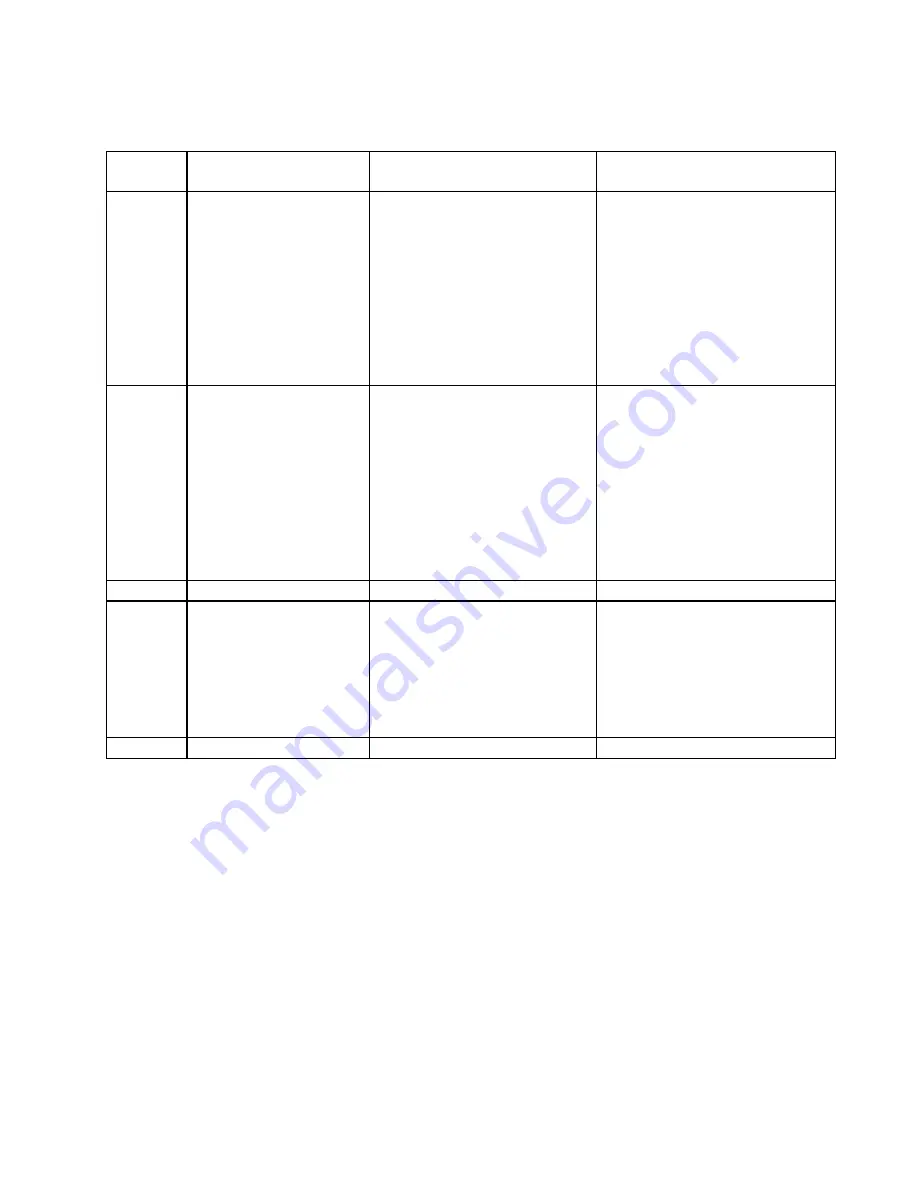
© PAT Revision E // SB // 09/03/02
190137_E
8. ERROR CODES - continued
ERROR
CODE
ERROR CAUSE
ACTION
E12
Fallen below lower
limit value for the
analog channel
“pressure
transducer piston
side”.
a.) Cable leading from the
central unit to the
pressure transducer
defective, loose or water
in the connector.
b.)Pressure transducer on
piston side defective.
c.)Electronic component
on the analog input
module defective.
a.)Check cable and
connector and replace, if
necessary.
b.)Replace pressure
transducer and reset
pressure channel.
c.)Replace analog input
module and reset pressure
channels.
E13
Fallen below lower
limit value for the
analog channel
“pressure
transducer rod
side”.
a.)Cable leading from the
central unit to the
pressure transducer
defective, loose or water
in the connector.
b.)Pressure transducer on
rod side defective.
c.)Electronic component
on the analog input
module defective.
a.)Check cable and
connectors and replace, if
necessary.
b.)Replace pressure
transducer and reset
pressure channel.
c.)Replace analog input
module and reset pressure
channels.
E 15
Fallen below lower
limit value for the
analog channel
“angle main boom”.
a.)Cable from central unit
to the length/angle sensor
defective or loose.
b.)Angle sensor defective.
c.)Electronic component
on the analog input
module defective.
a.)Check cable. Replace if
necessary.
b.)Replace angle sensor
and reset mechanical
adjustment.
c.)Replace main board and
reset pressure channels.