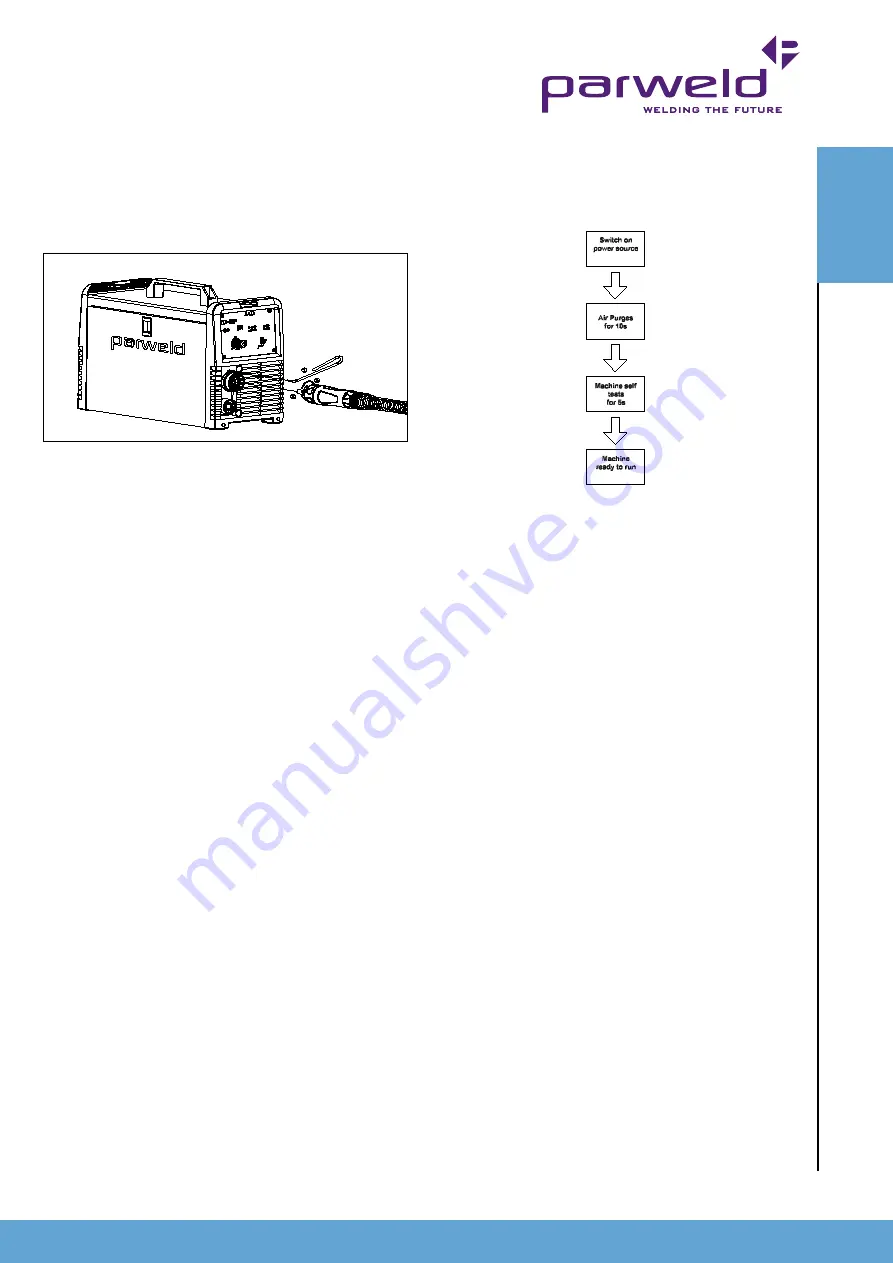
www.parweld.com
www.parweld.com
7
5.4 torch installation
Connect the torch to the machine using the special tool supplied as
illustrated below.
1) Insert the tool into the hole on the outside of the locking ring and
apply pressure to release the locking ring
2) Push the torch connector into the socket on the machine taking
care to line up the pins.
3) Tighten the hand nut on the torch to secure the torch
4) Release pressure on the locking tool and remove
CAUTION: Before switching on the machine ensure all spares
are fitted correctly to the torch and in good condition failure fit
spare parts can result in the destruction of the torch head.
5.6 Work return lead connection
Insert the connector in the socket and twist clockwise to lock.
6.0 Operation
WarnInG
When using an open arc process, it is necessary to use correct
eye, head, and body protection.
6.1 Consumable parts
The electrode, swirl ring and cutting tip are held in position by the
nozzle; removal of the nozzle allows these parts to be replaced.
Cutting tip size should be selected to match the selected amperage
on the machine and is not related to the thickness of the material to
be cut. Electrodes should be replaced when the insert has eroded
to a depth of no more than 1.2mm failure to replace the electrode
may result in permanent torch damage. The life of the electrode
is dependant upon the cut amperage and the number of starting
operations performed. The higher start frequency and cutting power
will give the shortest electrode life. Check the electrode condition
every 30 minutes of cutting
O
pera
tIO
n
6.2 Switching on the machine
When the machine is switched on it will perform a self
test routing as detailed following.
6.3 Setting the Air pressure
Connect the air line to the rear of the machine
and Switch on the machine. The air supply should be capable of
supplying compressed air at a pressure of 5Bar and a flow rate of
155lpm free air delivery. Switch on the machine and set the toggles
switch on the front panel to SET so that air flows through the torch.
With the air flowing ensure the interlock light does not come on, if the
interlock light illuminates then the air supply pressure to the machine
must be increased.
6.4 Getting ready to cut
Use the control knob on the front of the machine to
adjust the require output current, a higher current will give faster
cutting and a lower current slower cutting but more control for detail
cutting. The higher the set current the greater the wear rate will be
for the tip and electrode.
Summary of Contents for XTP-63
Page 1: ...Operator Manual ISSUE 1 XTP 63...
Page 13: ...www parweld com 13...