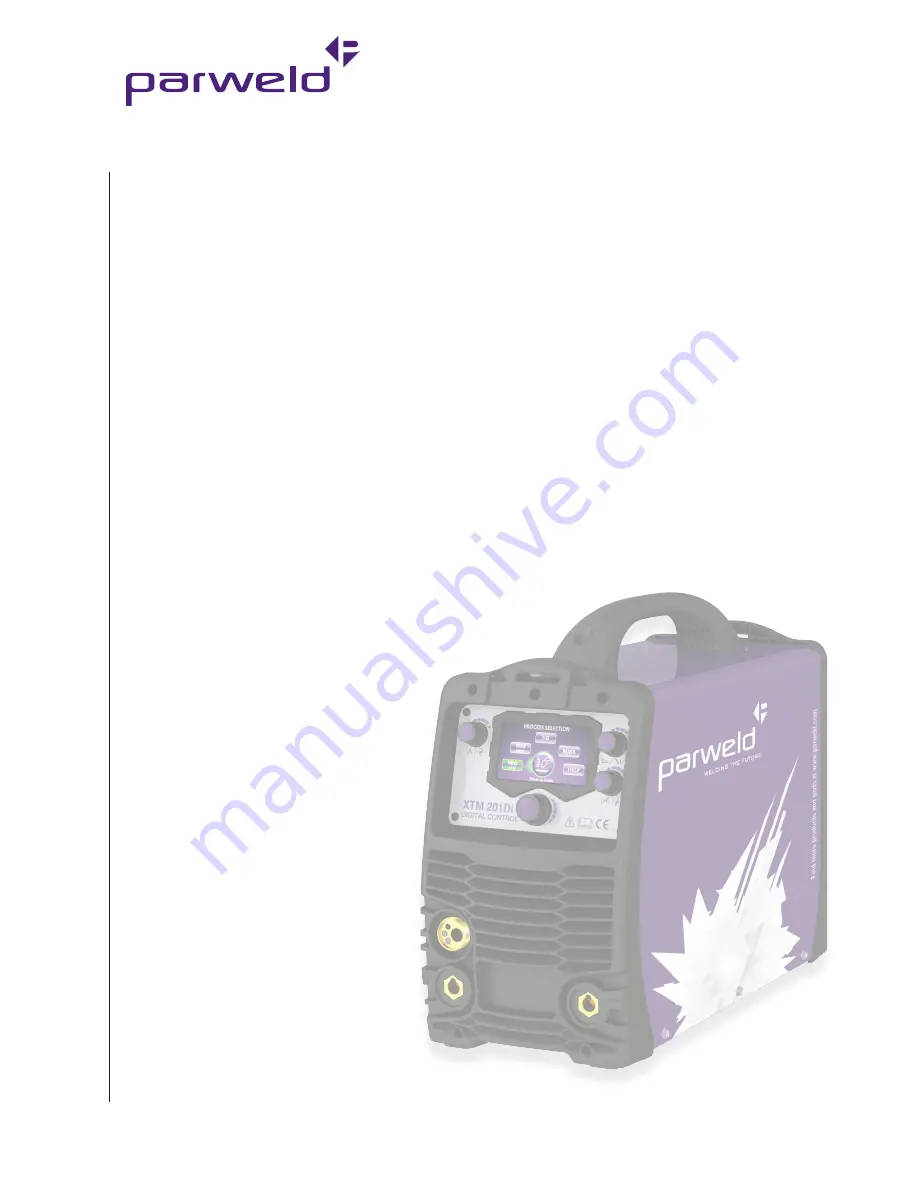
2
www.parweld.com
Welcome
Thank you for choosing Parweld. This Owner’s
Manual is designed to help you get the most
out of your Parweld products. Please take time
to read the Safety Precautions. They will help
you protect yourself against potential hazards
in the workplace. With proper maintenance
this equipment should provide years of reliable
service. All our systems conform to ISO9001:
2008 and are independently audited by NQA.
The entire product range carries the CE mark,
and is constructed in accordance with European
directives and the product specific standards
where they apply.
Further Information
Parweld is the UK’s leading supplier of MIG, TIG
and Plasma torches and consumables.
For more information about Parweld’s complete
range visit: www.parweld.com
Summary of Contents for XTM 201Di
Page 1: ...OPERATOR MANUAL ISSUE 1 XTM 201Di...
Page 21: ...www parweld com 21...
Page 22: ...www parweld com 22...
Page 23: ...www parweld com 23...