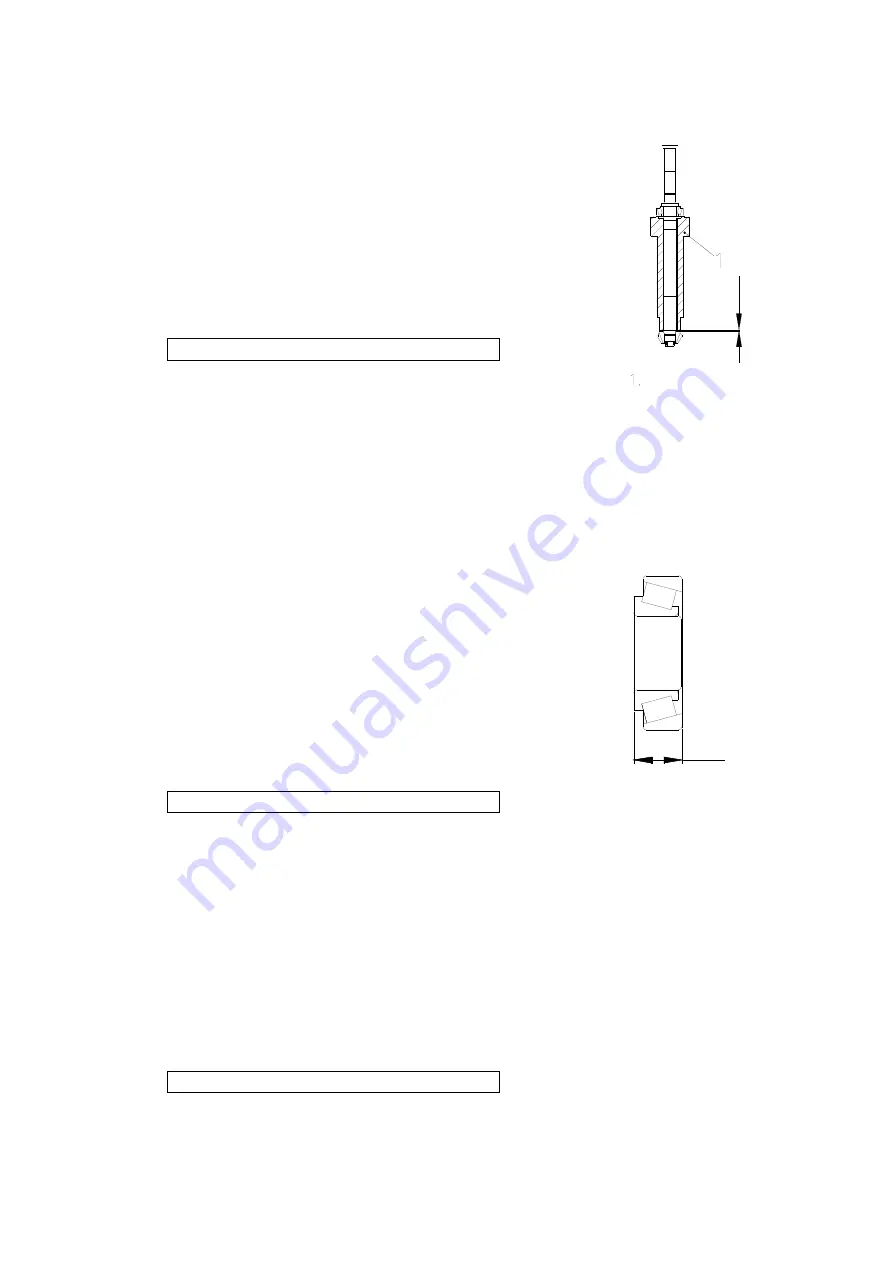
105
Pinion Shim
1.
Check the P value engraved on the Lower casing unit.
2.
Attach the drive shaft to the special tool. Fit the pinion and lock the pinion nut
according to the specified torque.
Specified torque: 95 Nm
3.
Measure the clearance between the special tool and
the pinion with a gauge,
Calculate the thickness T3 according to the formula.
Formula: T3=M3
-
(P/100)
Formula for CD/CT: T3=M3
-
(P/100)+0.1
4.
Shims that can be selected.
0.10, 0.12, 0.15, 0.18, 0.3, 0.4, 0.5 mm
Note:
The thickness of the shim can be 0 ~ 0.05
thicker than T3, and the closest size is selected.
Shims for Forward Gear
1.
Check the F value engraved on the Lower casing unit.
2.
Turn the outer ring of the forward gear bearing so that the roller falls completely into
the bearing casing.
3.
Measure the bearing height and calculate the thickness T1
according to the formula.
Formula: T1=26.70
+
(F/100)
-
M1
Formula for CD/CT: T1=24.2
+
(F/100)
-
M1
Note:
When measuring the thickness, it is measured at 3 points.
Average the results.
4.
Shims that can be selected.
0.10, 0.12, 0.15, 0.18, 0.3, 0.4, 0.5 mm
Note:
The thickness of the shim can be 0 ~ 0.05 thinner than T1, and the closest size is
selected.
Shims for Reverse Gear
1.
Check the R value engraved on the Lower casing unit.
2.
Formula: T2=0.5
+
(R/100)
Formula for CD/CT: T2=0.5
-
(R/100)
3.
Shims that can be selected.
0.10, 0.12, 0.15, 0.18, 0.3, 0.4, 0.5 mm
Note:
The thickness of the shim can be 0 ~ 0.05 thinner than T2, and the closest size is selected.
For CD/CT, the thickness of the shim can be 0 ~ 0.05 thicker than T2, and the closest size is selected.
M3
专用工具
M1
Summary of Contents for F60 BEL-D
Page 1: ...PARSUN OUTBOARD MOTOR SERVICE MANUAL F60 50 Suzhou Parsun Power Machine Co Ltd...
Page 16: ...11 Dimensions Outline Dimension D T model...
Page 17: ...12 Outline Dimension CD CT model...
Page 18: ...13 Mounting dimensions of clamp bracket...
Page 26: ...21 Decomposition Schematic Diagram M20 mm 160 Nm...
Page 27: ...22...
Page 28: ...23...
Page 29: ...24...
Page 30: ...25...
Page 31: ...26...
Page 39: ...34 Decomposition Schematic Diagram...
Page 40: ...35...
Page 41: ...36...
Page 42: ...37...
Page 43: ...38...
Page 49: ...44...
Page 50: ...45...
Page 51: ...46...
Page 52: ...47...
Page 53: ...48...
Page 54: ...49...
Page 55: ...50...
Page 56: ...51...
Page 57: ...52...
Page 58: ...53...
Page 59: ...54...
Page 72: ...67 Upper Casing Top Cowling Decomposition Schematic Diagram...
Page 74: ...69 Bottom Cowling Decomposition Schematic Diagram...
Page 75: ...70...
Page 76: ...71...
Page 77: ...72...
Page 79: ...74 Steering Handle Decomposition Schematic Diagram...
Page 80: ...75...
Page 82: ...77 Upper casing unit and Brackets Decomposition Schematic Diagram...
Page 83: ...78...
Page 84: ...79...
Page 85: ...80...
Page 86: ...81...
Page 87: ...82...
Page 90: ...85 Manual Tilting Device Disassembly Schematic Diagram...
Page 92: ...87 Hydraulic Tilting Device Disassembly Schematic Diagram...
Page 95: ...90 Lower casing Part Decomposition Schematic Diagram D T model...
Page 96: ...91...
Page 97: ...92...
Page 98: ...93...
Page 99: ...94...
Page 100: ...95...
Page 101: ...96...
Page 102: ...97 Decomposition Schematic Diagram CD CT model...
Page 103: ...98...