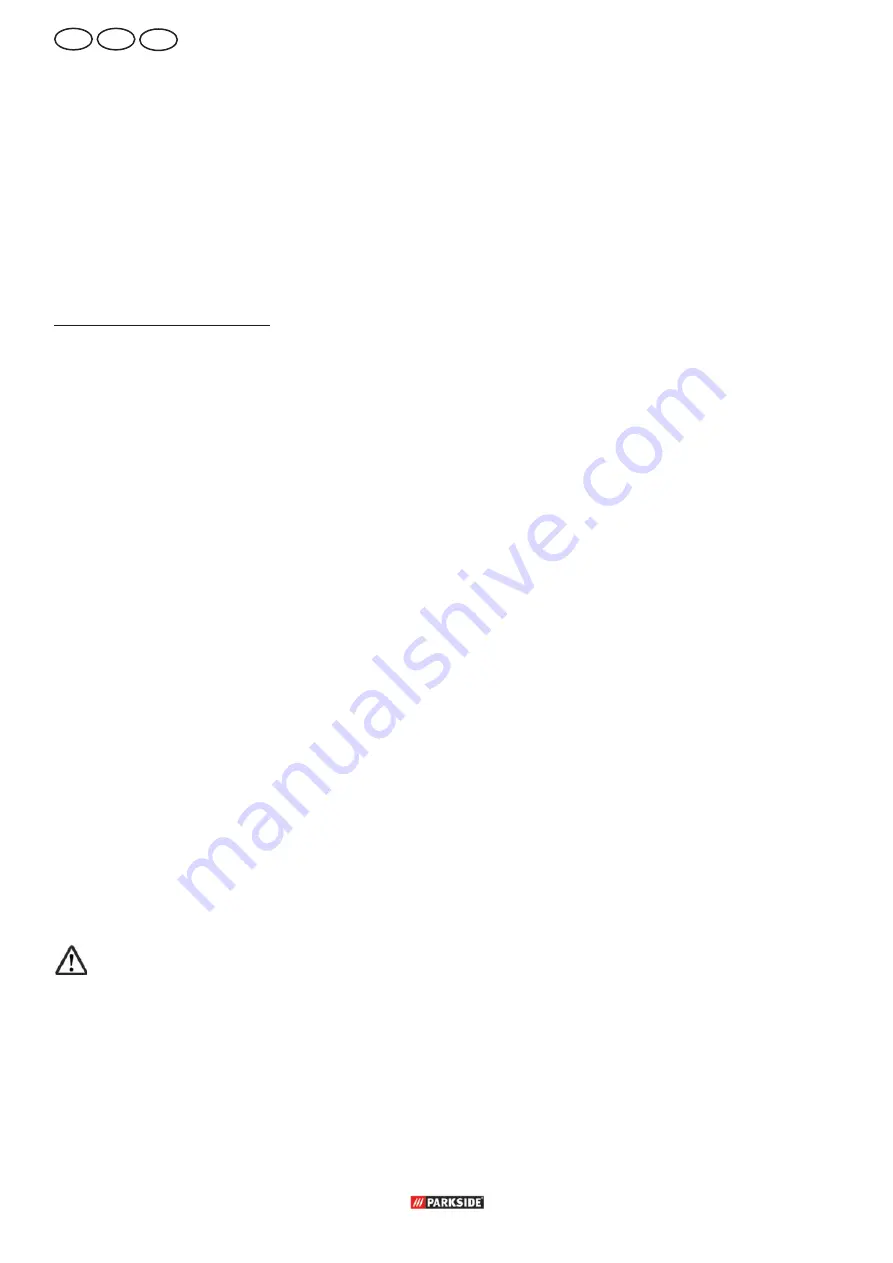
GB
IE
12
NI
point to the public mains is sufficient for the connection of
the product.
Important Instructions
If the motor is overloaded, it switches itself off automatically.
After cooling down (times vary), the motor can be switched on
again.
Faulty Electrical Connection Cable
Insulation damage often occurs to electrical connection cables.
The causes of this may be as follows:
•
Pressure points if connection cables are routed through
windows or door gaps.
•
Kinks caused by improper attachment or routing of the
connection cable.
• Cut surfaces caused by vehicles driving over the connection
cable.
• Insulation damage caused by tearing out of the wall socket.
• Cracks resulting from the insulation becoming old.
Such faulty electrical connections must not be used and may
endanger life due to the damage to the insulation.
Electrical connection cables should be checked regularly for
damage. Ensure that during such checks, the connection cable is
not connected to the mains.
Electrical connection cables must comply with the relevant
BS standards. Only use connection cables with the marking
H05VV-F.
It is stipulated by law that the type of connection cable must be
printed on it.
Alternating Current Motor
•
The mains voltage must be 230 V~.
• Extension cables up to 25 m in length must have a cross-sec-
tion of 2.5 mm².
Connections and repairs to the electrical equipment may only be
performed by a qualified electrician. If you have any queries,
please provide the following information:
• Current type of the engine
• Data from the machine type plate
• Data from the motor type plate
Assembly
Prior to first use, check the tightness of the
outer flange of the saw blade.
Assembly, Replacement of Parts and Adjustments
Caution! The mains plug must be removed before all
servicing, retooling and assembly work.
Place all of the parts supplied on a flat surface. Form groups of
the parts which are similar.
Insert the bolts from the outside to the inside in each case, secu-
ring the connections with nuts from the inside.
Note:
Tighten the nuts and bolts during assembly only to the
extent that they cannot fall off.
If you tighten the nuts and bolts any further before final assembly,
it is not possible for final assembly to be carried out.
Assembling the frame and table width
extender with length extender
(Figures. 1-10)
1. Place the table circular saw with saw table (1) onto the
ground. If the saw table (1) does not lie flat on the ground,
correct the position of the riving knife (3) and saw blade (4)
using the crank handle (12).
2. Align the table width (7) and length extension (17) flush with
the saw table. The ‘Parkside’ logo on the table extensions (7)
points away from the saw table (1).
3. Loosely tighten the table width extender (7) and table length
extender (17) on the saw table (1) using the hexagon bolts
with collar (a). (Fig. 6).
Screw the four legs (20) and the table supports
(26, 27) onto the housing.
4. Loosely tighten the table supports (26, 27) on the housing of
the table circular saw along with the four legs (20). Use the
hexagon bolts with collar (a). Use the table width extender
(7)/table length extender (17), hexagonal bolts with collar
(a), washers (c), spring washers (d) and nuts (e). The short
supports (26) are for the table widening extension, the long
supports (27) are for the length extension (Fig. 8, 9, 10).
5. Now loosely screw the central struts (21/22) onto the legs
(20). Use the carriage bolts (b), the washers (c), the spring
washers (d) and the nuts (e) (Fig. 11).
6. Next, tighten all the screws of the legs (20) and the table
width extender (7)/table length extender (17).
7. Now attach the rubber feet (23) to the legs (20) (Fig. 12).
8. Place the table circular saw onto the base frame (13).
Attention! Both stand brackets must be attached
to the rear of the machine at the attachment
points (25)! (Fig. 7).
9. Screw the stand brackets (24) into the rear legs (20) using
the drill holes. Assembly material for each: 2 carriage bolts
(b), the washers (c), the spring washers (d) and the nuts (e)
(Fig. 13).
Mounting a guide rail with scale (Fig 40 +
41)
10. Loosely attach the four carriage bolts (b) to the saw table (1)
and table width extender (7) using the nuts. The bolt heads
need to point outwards.
Select the two external drill holes in the saw table (1) and the
two external drill holes in the table width extender (7).
Thread both parts of the guide rail (16) onto the carriage
bolts on the saw table and table width extender. Assemble
the two parts of the guide rail.
Place the parallel stop with stop rail (6+39) onto the guide
rail (16) (Fig. 26).