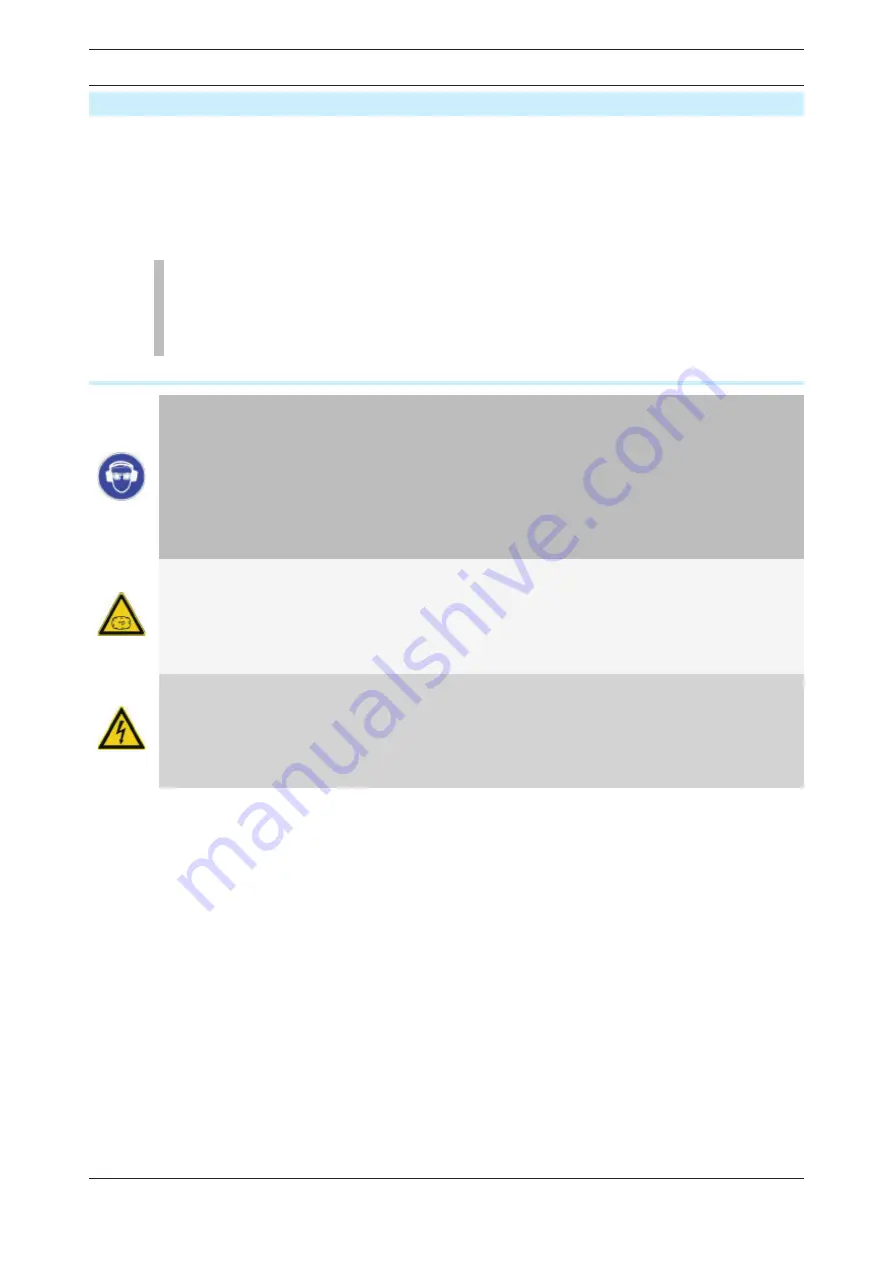
EN
| User Manual
For your own safety
6
K-MT 10-95/D3
For your own safety
The dryer has been built in accordance with the state of the art and the recognized technical
safety regulations. Nevertheless, there is a risk of personal injury and damage to property
when the dryer is used, if
◊
it is operated by non-qualifi ed personnel,
◊
not used within its intended design specifi cations,
◊
is repaired or maintained incorrectly.
Note:
For your own safety and to prevent machine damage, please note the informa-
tion and safety notes in these operating instructions when working with the
dryer.
General safety notes
Warning against sudden air ejection
When the hollow section vessels are depressurised, air fl ows suddenly out of
the sound absorber.
◊ This causes a sudden loud cracking noise.
◊ Due to particles carried in the air fl ow, there is a very considerable risk of
eye injury.
When working on the dryer, always wear eye and ear protection equipment.
Hazard due to a sudden release of pressure!
Never remove any parts of the dryer, or manipulate the same in any way, for
as long as the plant is still pressurised! A sudden escape of pressure may
cause serious injuries.
Before carrying out any work on the dryer, fi rst depressurise the plant.
Risk of injury due to voltage-carrying parts!
The electrical supply cable and external power lines are live even after the
dryer is switched off and, in the event of body contact, may cause serious
injury! Before carrying out any work on the electrical system, the electrical
supply cable and all external power lines must be made voltage-free!
Personnel qualifi cation
Only authorized and qualifi ed specialist personnel may be tasked with the work on the dryer
described in these operating instructions.
Conversions and modifi cations
Without prior approval by the manufacturer, no conversions and modifi cations must be made
to the dryer! Any non-approved modifi cations may restrict the operational safety of the dryer
and cause damage to property or personal injury.
Handling drying agents
The drying agents used do not pose any risk to health. However, when fi lling and emptying
the hollow section vessels with drying agents, increased dust generation may occur. Please
comply with the following instructions:
◊
When fi lling drying agents, wear a dust mask and eye protection!
◊
If a spillage occurs, any spilt drying agent must be taken up immediately. There is a risk of
skidding!