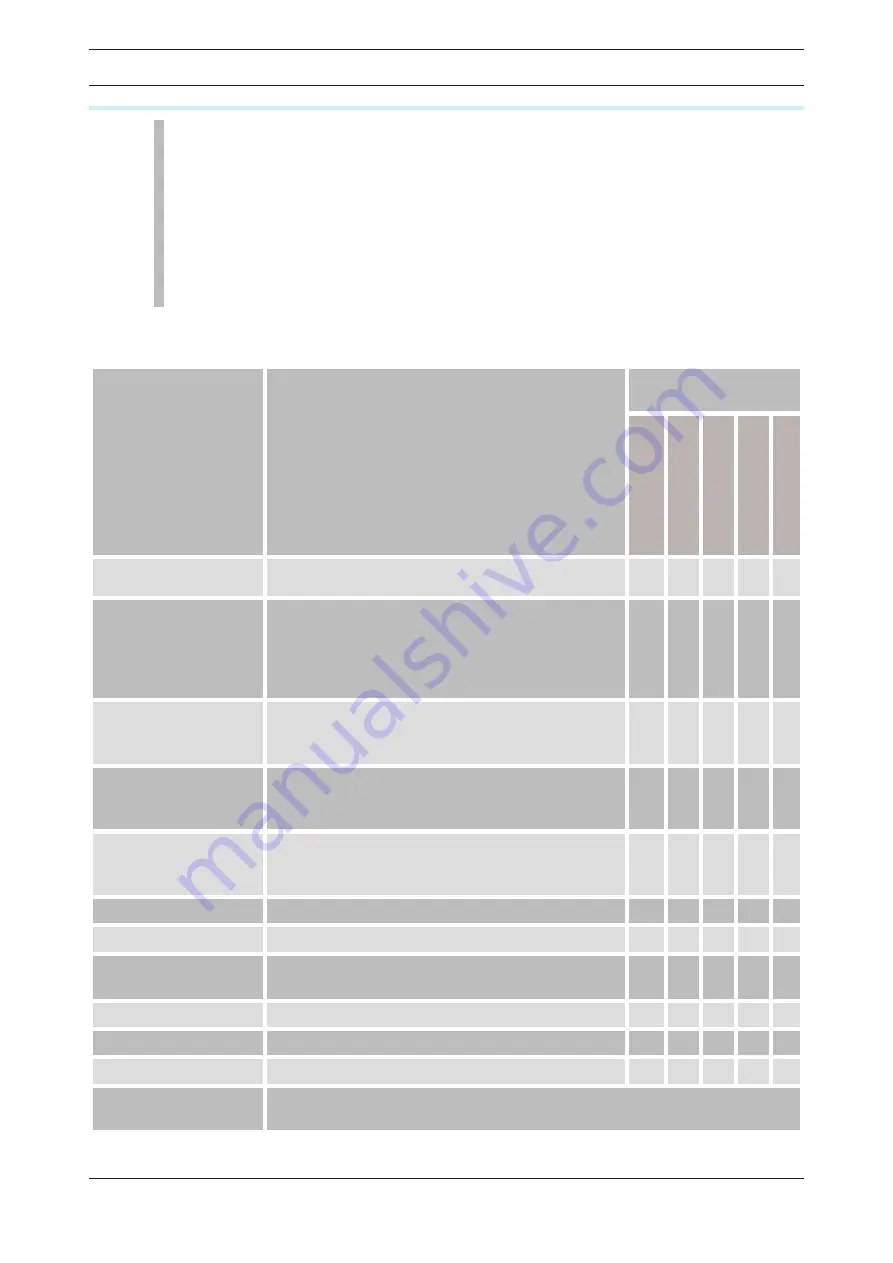
EN
| User Manual
Maintenance and repair of the dryer
34
K-MT 10-95/D3
Regular maintenance intervals
Note:
If a chamber has been depressurised, e.g. after completion of the ex-pansion
phase, and the pressure remains above 0 bar, the chamber is pressurised by
what is known as ram pressure. This might be due to
◊ blockage at the muffl er(s)
◊ contamination of the perforated plates
◊ spent drying agent
To prevent such malfunctions, regularly service the dryer as described below.
The table provides an overview of the maintenance work to be carried out. The individual
tasks are described in the following pages.
Component
Maintenance task to be carried out
Maintenance
interval
daily
12 months
24 months
48 months
See page
Complete dryer
Carry out visual checks and function checks.
•
36
Vessel pressure gauge Check dam pressure. For a dam pressure
exceeding 0.3 bar:
– Check muffl er.
– Check dust sieve.
– Check drying agent.
•
36
Muffl er
Replace muffl er after 1 year of operation and
after renewing the dessicant.
•
•
36
Fine fi lter muffl er
(option)
Replace element of fi ne fi lter muffl er after 1
year of operation and after renewing the drying
agents.
•
37
Dew point sensor
(with optional dew
point sensing-control)
Renew.
•
37
Pilot valves
Renew
•
39
Main valves V1/V2
Renew
•
39
Expansion valves
V3/V4
Renew
•
39
Check valves V5/V6
Renew
•
39
Solenoids
Renew
•
39
Drying agent
Renew
•
39
Upstream and down-
stream fi lter
Please see the enclosed operating instructions for the attached fi lters.
Maintenance work has to be carried out as specifi ed in this document.