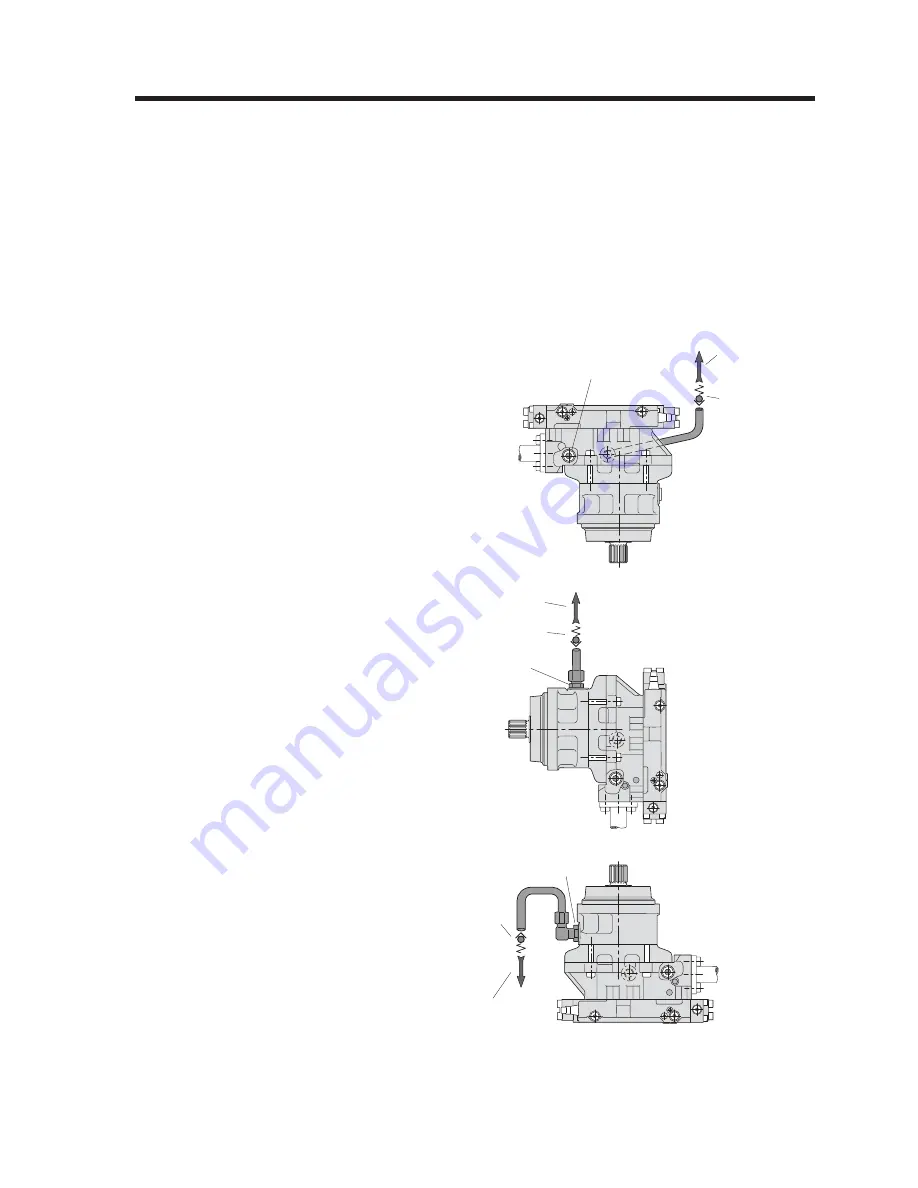
Hydraulic Motor/Pump
Series V14
Drain ports
There are two drain ports on the V14; the
uppermost drain port should always be
utilized (fig. 3).
In order to avoid excessively high case
pressure, the drain line should be connected
directly to the reservoir.
NOTE:
When the motor is operating, the
case must be filled with fluid to at
least 50%.
Hydraulic fluids
Ratings and performance data for series
V14 motors are valid when a good quality,
contamination-free, petroleum-based fluid is
used in the hydraulic system.
Hydraulic fluids type HLP (DIN 51524),
automatic transmission fluids type A, or
API CD engine oils can be used.
Fire resistant fluids, when used under
modified operating conditions, and synthetic
fluids are also suitable.
When the hydraulic system has reached full
operating temperature, the motor drain oil
viscosity should be above 8 mm²/s (cSt).
At start-up, the viscosity should not exceed
1500 mm²/s.
The ideal operating range for the V14 series
is 15 to 30 mm²/s.
The following publications (available from
Parker Hannifin, Mobile controls Div.) provide
additional information:
MI 180 - Hydraulic fluid specifications
MI 189 - Fire resistant fluids
Before start-up
Make sure the motor case as well as the
entire hydraulic system is filled with hydraulic
fluid. The internal leakage, especially at low
operating pressures, is not sufficient to
provide lubrication at start-up.
Note:
A drain line spring loaded check valve
(shown in fig. 2, 3 and 4) may have to be
installed in order to prevent oil from being
siphoned out of the motor case. This can
otherwise happen e.g. if the reservoir is
located below the utilized motor drain port.
Fig. 2.
Fig. 3.
Fig. 4.
Flushing valve
(optional)
Drain and
cooling flow
to reservoir
Drain port
To reservoir
Check
valve
To reservoir
Check valve
Check valve
Drain port
9