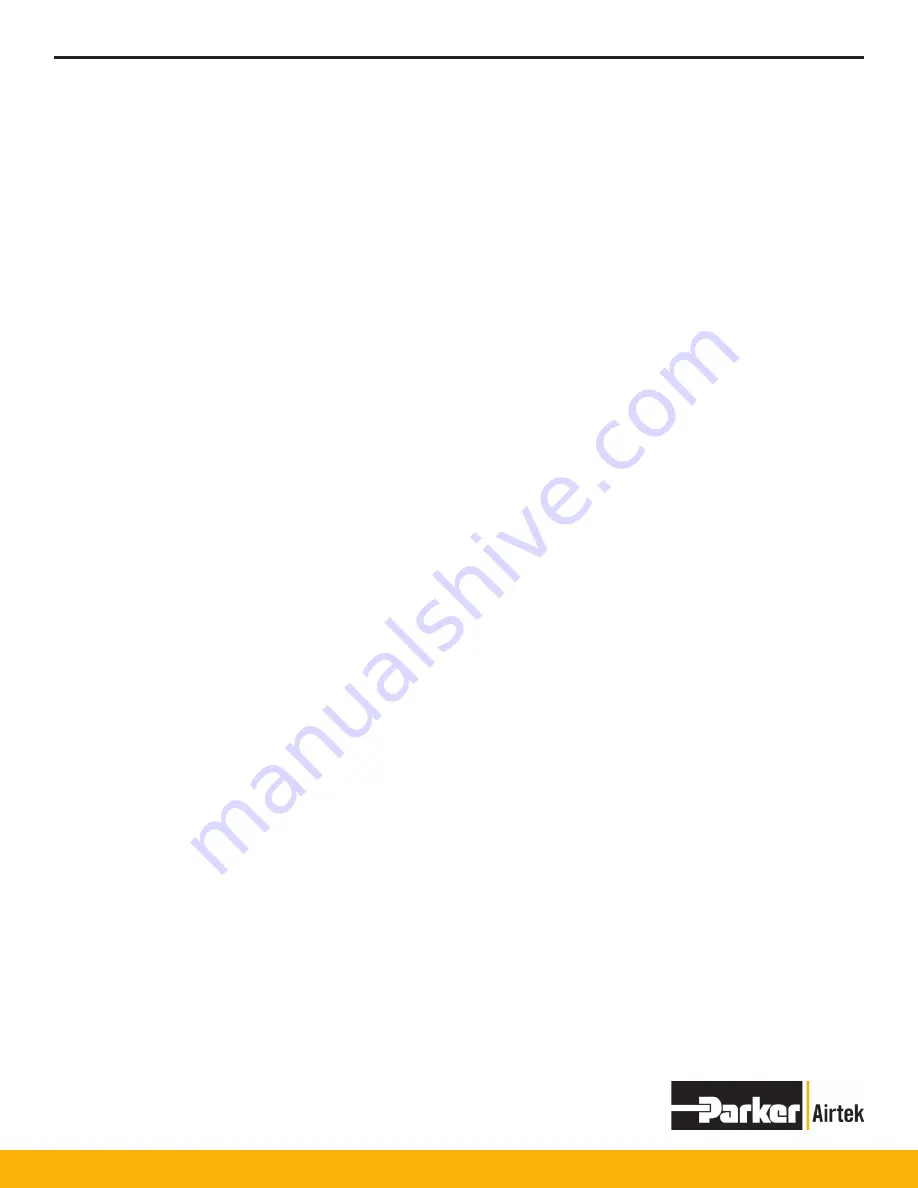
TWP/TWB201 – TWP/TWB7501
57
Weekly
Check air flow rate, air inlet pressure and temperature are within design specifications of dryer.
Check blower and blower inlet filter. (Blower purge models only).
Semi-annual
Check the condition of the prefilter and afterfilter elements. Verify the differential pressure across the filters.
Replace as needed.
Check desiccant quality. Desiccant from a freshly regenerated bed should be white, dry to the touch and of consis-
tent size and shape. Continuous adsorption and desorption causes the performance level of desiccant to decline
over time. Oil and contaminants causes reduction in the adsorption ability of the desiccant. It is recommended to
replace the desiccant every 3-5 years.
Check exhaust mufflers and verify there is no back pressure in regenerating vessel. If the muffler is clogged, it must
be cleaned or replaced.
Tighten wire connections to heater. Stud terminals should be tightened to a maximum torque of 20 in-lbs while the
bottom nut is supported. Stud terminals that do not have a bussbar or factory installed ring connector should only
be tightened to 9 in-lbs.
Check condition of blower inlet filter element and replace as needed. (Blower purge models only).
Inspect blower drive belt and idler pulley. Replace if needed. (Blower purge models 4001-7501 only).
Annual
Check condition of control air filter element. Replace as needed.
Check condition of all inlet and exhaust switching valves. It is recommended to clean and rebuild the valves to
maintain proper working condition.
Check dewpoint sensor and recalibrate as needed.
Check contactors and starters. Replace as needed.
Inspect blower head, tensioner, and pulleys for correct operation. (Blower purge models 4001-7501 only.)
Summary of Contents for TWP/TWB201
Page 1: ...1 Externally Heated Blower Purge Desiccant Dryers User Manual Models TWP TWB201 TWP TWB7501...
Page 9: ...TWP TWB201 TWP TWB7501 9 TWP Desiccant Dryer Operation TWB Desiccant Dryer Operation...
Page 10: ...TWP TWB201 TWP TWB7501 10 FLOW SCHEMATIC MODELS TWP201 301...
Page 11: ...TWP TWB201 TWP TWB7501 11 FLOW SCHEMATIC MODELS TWP401 801...
Page 12: ...TWP TWB201 TWP TWB7501 12 FLOW SCHEMATIC MODELS TWP1001 1201...
Page 13: ...TWP TWB201 TWP TWB7501 13 FLOW SCHEMATIC MODELS TWP1501 7501...
Page 14: ...TWP TWB201 TWP TWB7501 14 FLOW SCHEMATIC MODELS TWB201 801...
Page 15: ...TWP TWB201 TWP TWB7501 15 FLOW SCHEMATIC MODELS TWB1001 1201...
Page 16: ...TWP TWB201 TWP TWB7501 16 FLOW SCHEMATIC MODELS TWB1501 7501...
Page 17: ...TWP TWB201 TWP TWB7501 17 TWP WIRING DIAGRAM STANDARD CONTROLLER...
Page 18: ...TWP TWB201 TWP TWB7501 18 TWP WIRING DIAGRAM STANDARD CONTROLLER...
Page 19: ...TWP TWB201 TWP TWB7501 19 TWP WIRING DIAGRAM STANDARD CONTROLLER...
Page 20: ...TWP TWB201 TWP TWB7501 20 TWP WIRING DIAGRAM STANDARD CONTROLLER...
Page 21: ...TWP TWB201 TWP TWB7501 21 TWB WIRING DIAGRAM STANDARD CONTROLLER...
Page 22: ...TWP TWB201 TWP TWB7501 22 TWB WIRING DIAGRAM STANDARD CONTROLLER...
Page 23: ...TWP TWB201 TWP TWB7501 23 TWB WIRING DIAGRAM STANDARD CONTROLLER...
Page 24: ...TWP TWB201 TWP TWB7501 24 TWB WIRING DIAGRAM STANDARD CONTROLLER...
Page 25: ...TWP TWB201 TWP TWB7501 25 PANEL LAYOUT STANDARD CONTROLLER...