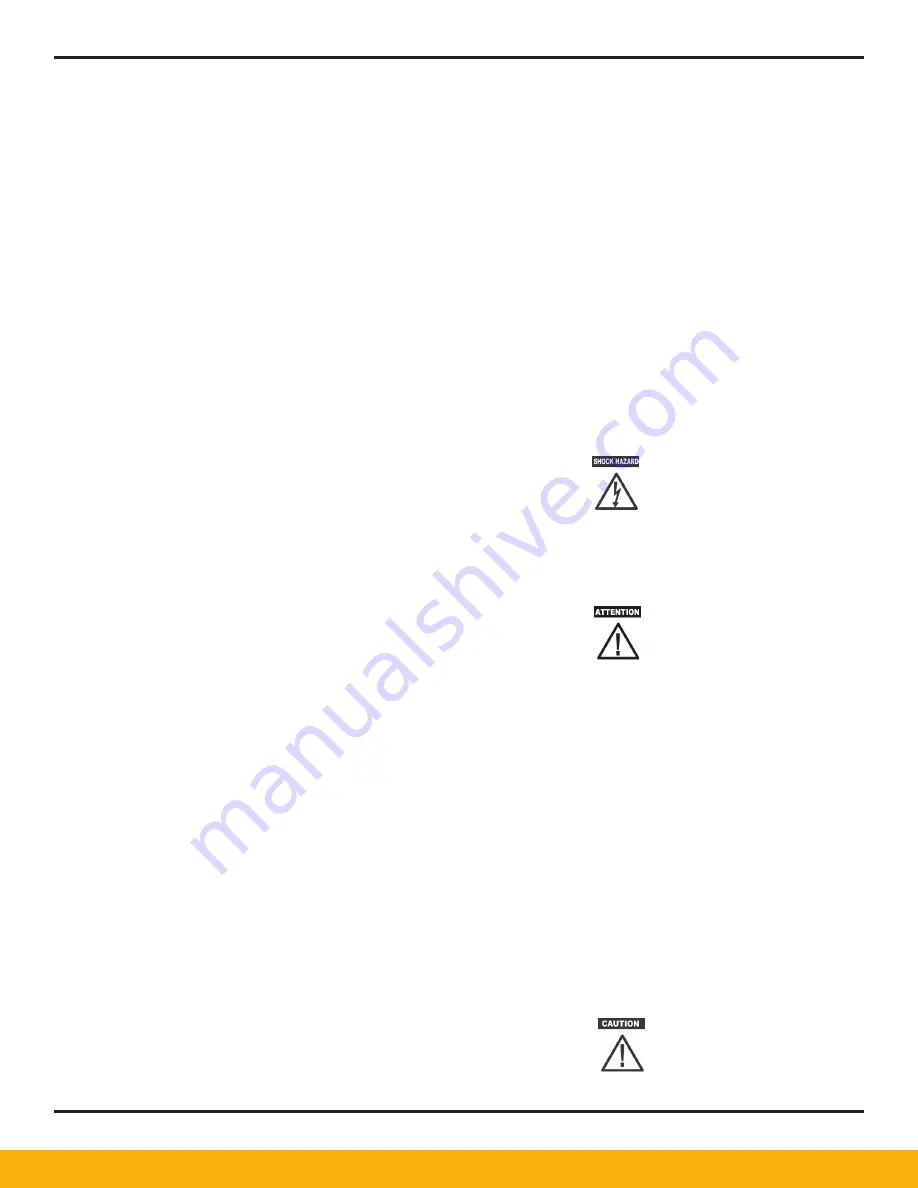
PTM200 - PTM1000 USER GUIDE
Page 4 - Rev D
•
Air piping must be supported independently of the dryer.
•
A properly sized Parker Airtek pre-filter must be installed ahead of the
dryer to maintain optimal performance and warranty validation. It should be
installed as close to the dryer as possible. Any piping between the pre-filter
and inlet of the dryer must be stainless steel, copper, galvanized, aluminum
or other non-corroding material.
•
Direction of the air flow must be observed for proper installation.
•
Install a bypass line and gate valves to permit isolation of the dryer from the
air system. This is done to provide easy service and/or removal of the dryer
without interruption of air to the system.
•
Make the connection to the draining system, avoiding connection in a closed
circuit shared by other pressurized discharge lines. Check the correct flow
of condensate discharges. Dispose of all condensate in conformity with
current local environment regulations.
2.2
Electrical Connections
To be performed by a qualified person only. Risk of serious injury or death.
Observe Lock out/Tag Out Procedure: Disconnect, lock out and tag all power at
source prior to attempting repairs or adjustments to rotating machinery and prior
to handling any ungrounded conductors.
Provide breach and short circuit protection as well as disconnect means per
local and national codes.
Before connecting electrical power to the dryer check for correct voltage at
the connection box. Panel Removal: To remove front or side panels, remove
screws and lift panel up, then pull out the bottom.
All units must be externally grounded to protect against severe electrical shock.
1.
Remove electric box cover from inside unit.
2.
Locate the wires.
3.
Locate hole on side of box, place and tighten connector, run wires
through connector.
4.
Make sure no bare wire is exposed; replace box cover and screw closed.
5.
Line input wiring connections are made to line side on compressor
contactor
6.
Should the compressor not start, see start up procedure.
Summary of Contents for PTM Series
Page 18: ...PTM200 PTM1000 USER GUIDE Page 18 Rev D 12 Associated Drawings REF ADE11249 REV F...
Page 19: ...PTM200 PTM1000 USER GUIDE Page 19 Rev D REF ADE11249 REV F...
Page 20: ...PTM200 PTM1000 USER GUIDE Page 20 Rev D REF ADE11249 REV F...
Page 21: ...PTM200 PTM1000 USER GUIDE Page 21 Rev D REF ADE11249 REV F...
Page 22: ...PTM200 PTM1000 USER GUIDE Page 22 Rev D REF ADE11249 REV F...
Page 23: ...PTM200 PTM1000 USER GUIDE Page 23 Rev D REF ADE11249 REV F...
Page 24: ...PTM200 PTM1000 USER GUIDE Page 24 Rev D REF ADE11249 REV F...
Page 25: ...PTM200 PTM1000 USER GUIDE Page 25 Rev D REF ADE11249 REV F...