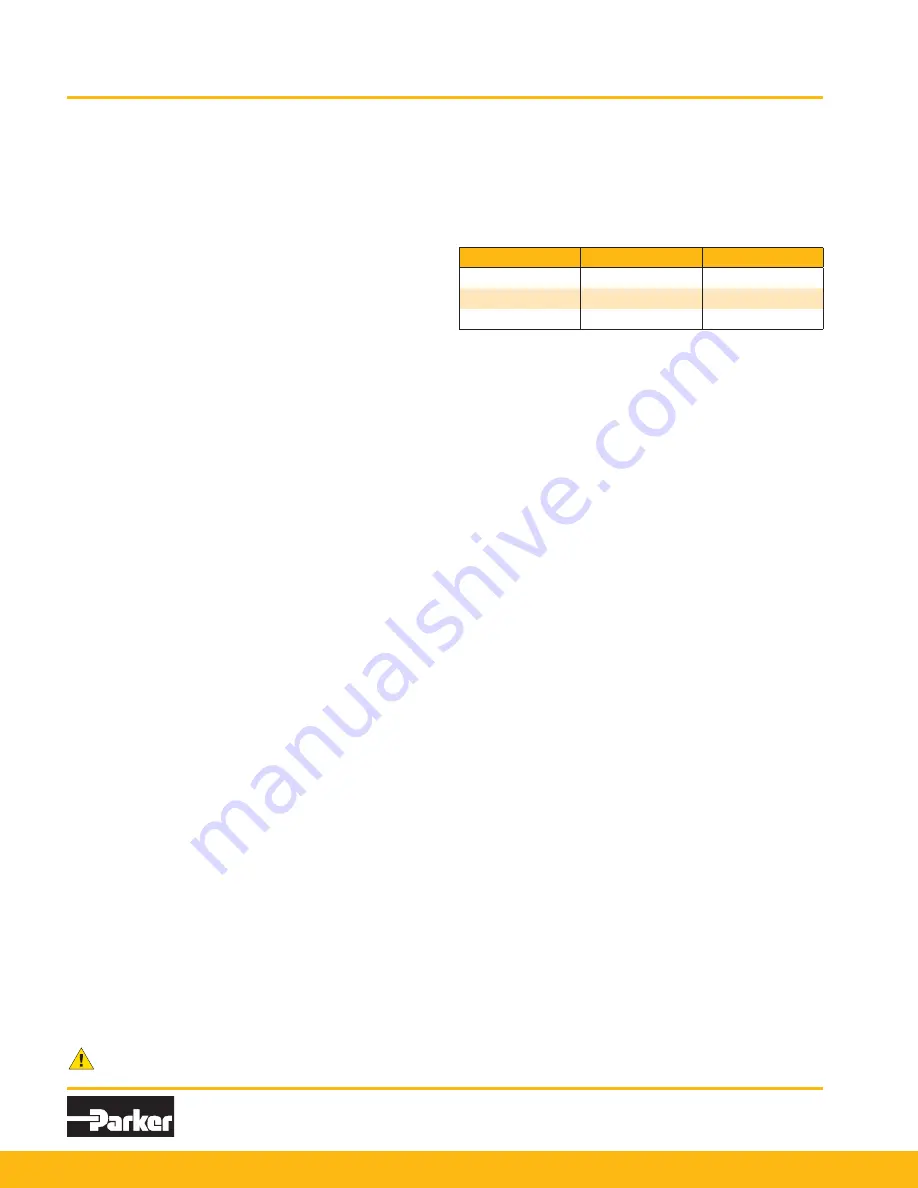
21
22
Parker Hannifin Corporation
|
Pump & Motor Division
|
Kings Mountain, NC
Parker Hannifin Corporation
|
Pump & Motor Division
|
Kings Mountain, NC
WARNING:
This product can expose you to chemicals including lead or DEHP which are known to the state of California to cause cancer,
birth defects, and other reproductive harm. www.p65warnings.ca.gov
WARNING:
This product can expose you to chemicals including lead or DEHP which are known to the state of California to cause cancer,
birth defects, and other reproductive harm. www.p65warnings.ca.gov
Catalog HY13-PMD500-SM/US
PGP/PGM 500 Series
Gear Pumps & Motors Service Manual
Fluid Recommendations
Operating Temperature
The optimum oil operating temperature is in the range of
120°-140°F (49°-60°C). Oil operating temperature should
not exceed 200°F (93°C) with a maximum of 180°F (82°C)
generally recommended. If the oil temperature will be above
180°F (82°C) for significant periods of time, then Viton (FKM)
seals should be used. High temperatures may result in rapid
oil deterioration and may point out the need for an oil cooler
or a larger reservoir. The nearer to optimum temperature,
the longer the service life will be of the oil, pump and other
components.
Cold Weather Operation
Oils for use in cold weather should have a viscosity not
exceeding 7500 SUS (1620 cSt) at the minimum start-up
temperature and a pour point of at least 20°F (7°C) below
that temperature. Experience on the Alaskan North Slope
has been satisfactory without using special oils or fluids.
Start-up procedures must allow for a gradual warm-up and
equipment should not be operated at full pressure until the
oil reaches a reasonably fluid state.
Inlet Vacuum
Vacuum measured at the inlet port of the pump generally
should not exceed 5 in. (13 cm) Hg. Higher vacuum can
result in cavitation which may severely damage the pump. A
usually acceptable rule of thumb is that the inlet line velocity
should not exceed 8 fps (2.5 m/s). A long inlet line or the use
of several fittings may necessitate increasing the line size.
We suggest that each inlet port of a tandem pump have its
own line from the reservoir.
Reservoir
Reservoir capacity in gallons should at least equal total
pump output in GPM. When filling the reservoir, oil should
pass through a 100-mesh screen. Pour only clean oil from
clean containers into the reservoir. The reservoir should have
a breather to allow air in or out. The filler cap and breather
should be sealed to prevent moisture from entering. A
hydraulic oil water content of as little as 0.1% can cause
damage to hydraulic components.
Filtration
Good filtration assures improved service life at today’s high
operating pressures. System filtration is recommended that
will maintain a contamination level according to ISO 4406:
ISO 4406
psi
bar
21/19/16
2000
140
19/17/14
3000
210
17/15/12
4000
275
The specific filter recommendation should come from your
equipment manufacturer or filter supplier.
A 100 mesh screen should generally be used in the suction
line leading to the pump. It should be of sufficient size
to handle twice the pump capacity. The screen must be
cleaned and checked regularly to avoid pump and system
damage.
Oil and filters should be changed on a regular schedule
and the system flushed in accordance with the original
equipment manufacturer's recommendations. Reservoir air
breather filters should be cleaned periodically.
Filtration is not a substitute for practicing cleanliness
and proper preventive maintenance.
Hydraulic Oil Recommendations (Continued)
Petroleum Oils (Mineral-based) (Continued)