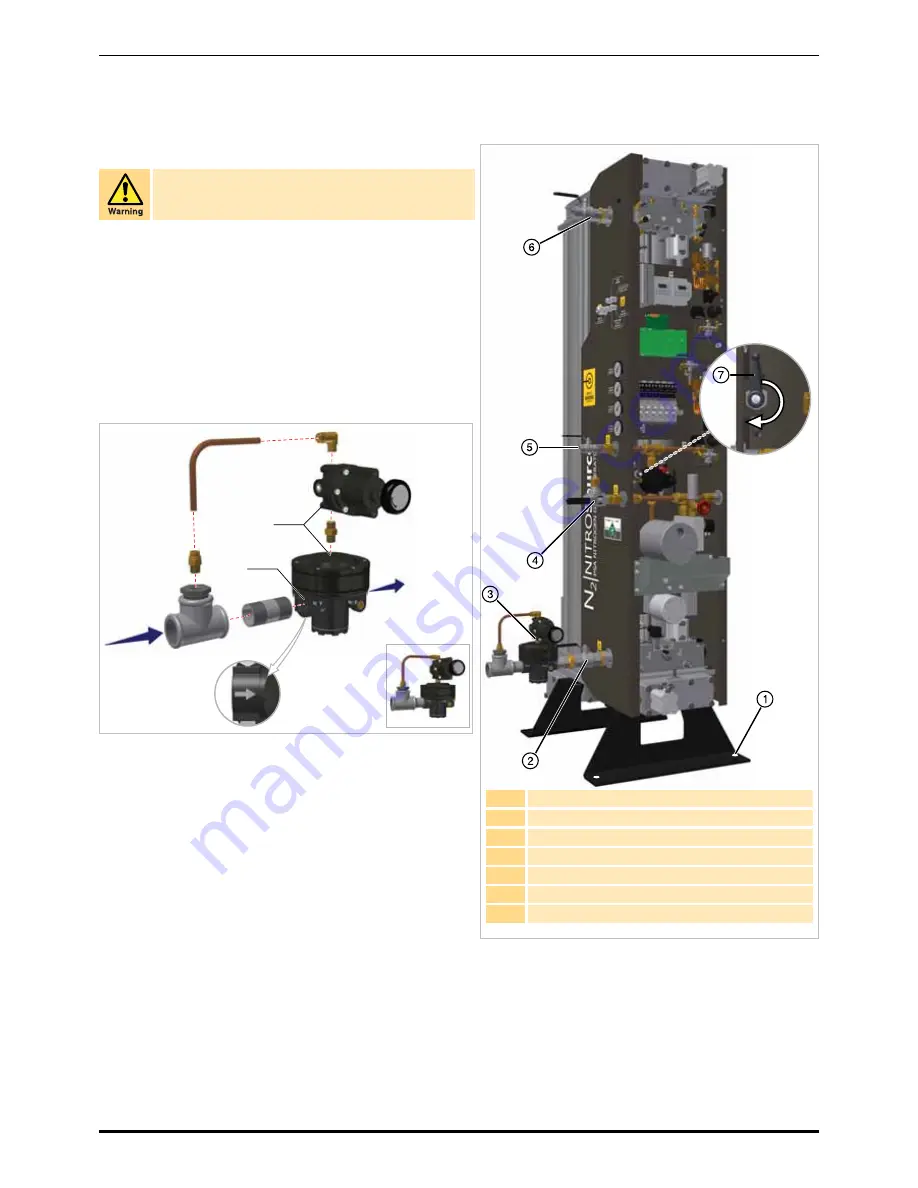
14 - EN
3.3.2 Securing the Generator
3.3.3 Making the Connections
Refer to the “Recommended System Component Layout” on page 11 for
the desired system configuration.
Port connections are provided on both sides of the generator. Connect the
ball valves supplied to the ports, using PTFE tape on the threads to provide
a leak free seal.
Assemble the inlet pressure regulator as illustrated below taking note of the
flow directions marked on the underside of the pilot operated regulator.
Use PTFE tape on the threads to provide a leak free seal.
Note.
Fittings are not supplied.
When installing the 3-way ball valve to the Nitrogen Outlet port ensure that
it is positioned in a vertical position and so that there is unrestricted access
to the centre port for the connection of a flow meter.
Install the pipe-work ready for connection to the buffer vessel and
compressed air supply. We recommend that additional ball valves are
connected to the buffer vessel ports to allow it to be isolated during
maintenance activities.
Setting the inlet Pressure Regulator
The inlet pressure must be set prior to running the generator.
1
Adjust the internal Inlet / Outlet pressure ball valve to the
Inlet
Pressure
position (pointing down).
2
Power up the generator and navigate to menu 3.5. The inlet
compressed air pressure will be displayed.
3
Check the rating plate for the required set pressure then adjust the regulator until the required set pressure is displayed on menu 3.5.
4
Tighten the lock nut on the regulator adjustment handle to prevent inadvertent adjustment.
5
Reposition the internal Inlet / Outlet pressure ball valve to the
Outlet Pressure
position (pointing upwards).
The generator MUST be fixed in position using suitable
M20x40mm Rawl bolts (or equivalent). Mounting holes are
provided in the feet of the generator.
1
Mounting holes
2
Inlet Port: Compressed Air Inlet (1” BSPP ball valve)
3
Inlet Pressure Regulator
4
Outlet Port: Nitrogen Outlet (1/2” 3-way ball valve)
5
Inlet Port: From Buffer Vessel (1/2” ball valve)
6
Outlet Port: To Buffer Vessel (1” BSPP ball valve)
7
Internal inlet / outlet pressure ball valve
1” BSPP
1/4” BSPP