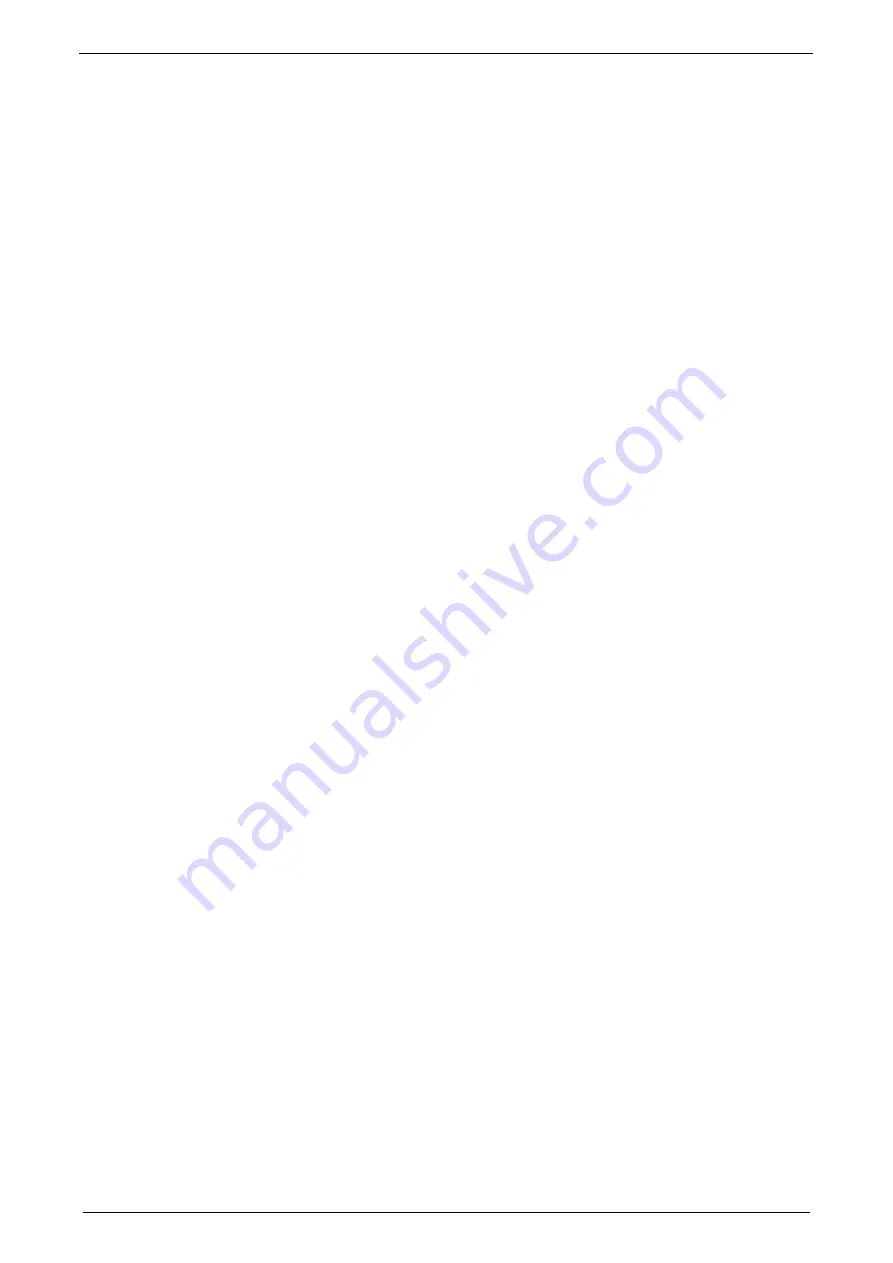
Supply repair
HLR Mounting Instruction
52
192-510201N1 HLR 2019-04
In the event of a damage or a mechanical defect, the entire unit must be returned
for repair (Parker Hannifin (see page 1)). The repair must be made by trained
Parker personnel.
User conversions and changes are not Permitted
The linear actuator must not be changed in its design or in terms of safety without
our approval. Any change as defined here made by the user excludes any liability
on our part.
6. Supply repair
Summary of Contents for HLR Series
Page 6: ...Introduction HLR Mounting Instruction 6 192 510201N1 HLR 2019 04 1 3 Mounting explanation...
Page 14: ...Device description HLR Mounting Instruction 14 192 510201N1 HLR 2019 04...
Page 15: ...Parker EME Conditions of utilization 192 510201N1 HLR 2019 04 15...
Page 16: ...Device description HLR Mounting Instruction 16 192 510201N1 HLR 2019 04 2 1 Technical data...
Page 17: ...Parker EME Dimensions 192 510201N1 HLR 2019 04 17 2 2 Dimensions...
Page 18: ...Device description HLR Mounting Instruction 18 192 510201N1 HLR 2019 04...
Page 19: ...Parker EME Dimensions 192 510201N1 HLR 2019 04 19...
Page 54: ...Index HLR Mounting Instruction 54 192 510201N1 HLR 2019 04...
Page 55: ...Parker EME Spare and Wear Parts 192 510201N1 HLR 2019 04 55...
Page 56: ...Index HLR Mounting Instruction 56 192 510201N1 HLR 2019 04...