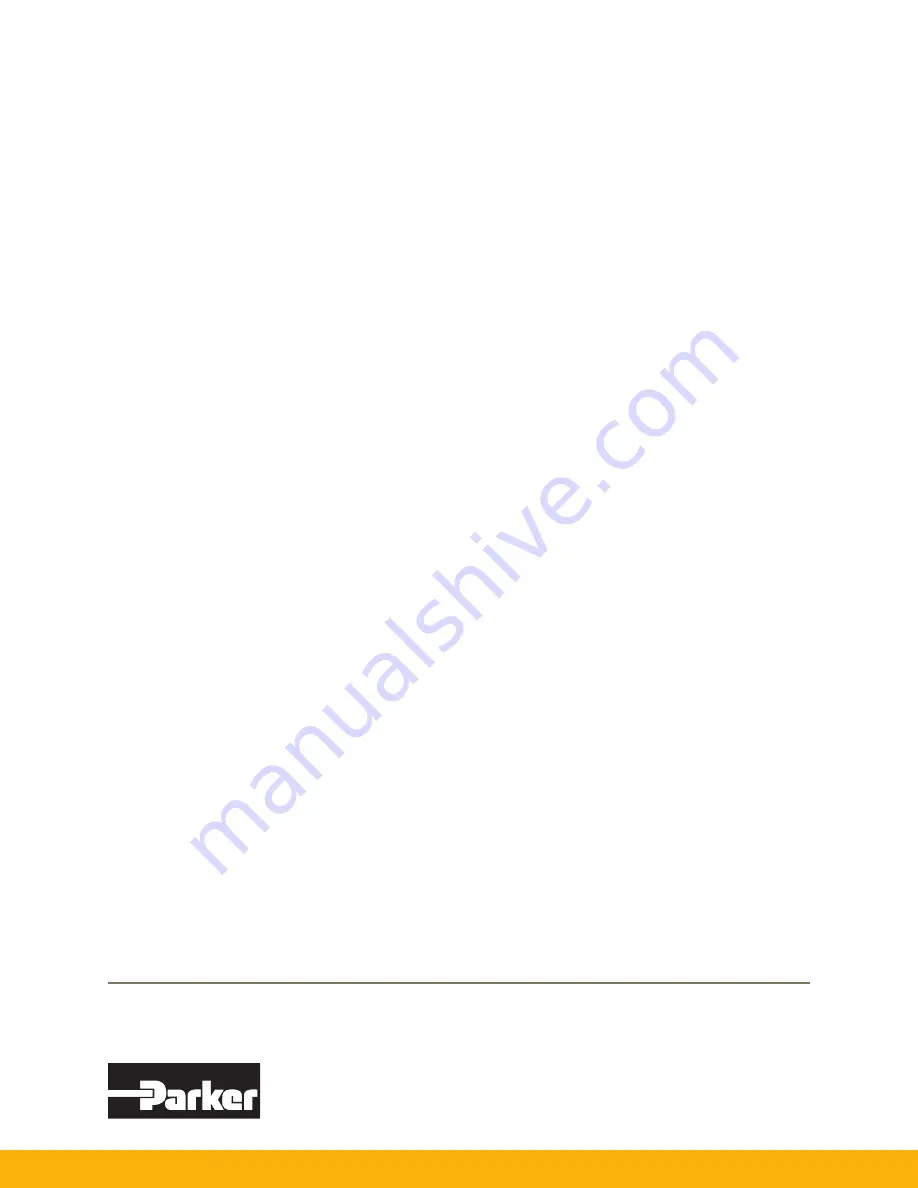
North America
Compressed Air Treatment
Filtration & Separation/Balston
Haverhill, MA
978 858 0505
www.parker.com/balston
Finite Airtek Filtration
Airtek/domnick hunter/Zander
Lancaster, NY
716 686 6400
www.parker.com/faf
Finite Airtek Filtration/Finite
Oxford, MI
248 628 6400
www.parker.com/finitefilter
Engine Filtration &
Water Purification
Racor
Modesto, CA
209 521 7860
www.parker.com/racor
Holly Springs, MS
662 252 2656
www.parker.com/racor
Beaufort, SC
843 846 3200
www.parker.com/racor
Racor – Village Marine Tec.
Gardena, CA
310 516 9911
desalination.parker.com
Parker Sea Recovery
Carson, CA
310 637 3400
www.searecovery.com
Hydraulic Filtration
Hydraulic Filter
Metamora, OH
419 644 4311
www.parker.com/hydraulicfilter
Laval, QC Canada
450 629 9594
www.parkerfarr.com
Process Filtration
domnick hunter Process Filtration
Oxnard, CA
805 604 3400
www.parker.com/processfiltration
Madison, WI
608 824 0500
www.scilog.com
Phoenixville, PA
610 933 1600
www.parker.com/processfiltration
Aerospace Filtration
Velcon Filtration
Colorado Springs, CO
719 531 5855
www.velcon.com
Europe
Compressed Air Treatment
domnick hunter Filtration & Separation
Gateshead, England
+44 (0) 191 402 9000
www.parker.com/dhfns
Parker Gas Separations
Etten-Leur, Netherlands
+31 76 508 5300
www.parker.com/dhfns
Hiross Zander
Padova Business Unit
Padova, Italy
+39 049 9712 111
www.parker.com/hzd
Hiross Zander
Essen Business Unit
Essen, Germany
+49 2054 9340
www.parker.com/hzd
Engine Filtration &
Water Purification
Racor
Dewsbury, England
+44 (0) 1924 487 000
www.parker.com/rfde
Racor Research & Development
Stuttgart, Germany
+49 (0)711 7071 290-10
www.parker.com/rfde
Hydraulic Filtration
Hydraulic Filter
Arnhem, Holland
+31 26 3760376
www.parker.com/hfde
Urjala Operation
Urjala, Finland
+358 20 753 2500
www.parker.com/hfde
Condition Monitoring Centre
Norfolk, England
+44 (0) 1842 763 299
www.parker.com/hfde
Parker Kittiwake
West Sussex, England
+44 (0) 1903 731 470
www.kittiwake.com
Parker Procal
Peterborough, England
+44 (0) 1733 232 495
www.kittiwake.com
Process Filtration
domnick hunter Process Filtration
Birtley, England
+44 (0) 191 410 5121
www.parker.com/processfiltration
Parker Twin Filter BV
Zaandam, Netherlands
+31(0)75 655 50 00
www.twinfilter.com
Asia Pacific
Australia
Castle Hill, Australia
+61 2 9634 7777
www.parker.com/australia
China
Shanghai, China
+86 21 5031 2525
www.parker.com/china
India
Navi Mumbai, India
+91 22 651 370 8185
www.parker.com/india
Parker Fowler
Bangalore, India
+91 80 2783 6794
www.johnfowlerindia.com
Japan
Tokyo, Japan
+81 45 870 1522
www.parker.com/japan
Parker Techno
Osaka, Japan
+81 66 340 1600
www.techno.taiyo-ltd.co.jp
Korea
Hwaseon-City
+82 31 359 0852
www.parker.com/korea
Singapore
Jurong Town, Singapore
+65 6887 6300
www.parker.com/singapore
Thailand
Bangkok, Thailand
+66 2186 7000
www.parker.com/thailand
Latin America
Parker Comercio Ltda.
Filtration Division
Sao Paulo, Brazil
+55 12 4009 3500
www.parker.com/br
Pan American Division
Miami, FL
305 470 8800
www.parker.com/panam
Africa
Aeroport Kempton Park, South Africa
+27 11 9610700
www.parker.com/africa
Parker Hannifin Corporation
Finite Airtek Filtration Division
4087 Walden Avenue
Lancaster, NY 14086
phone 716 686 6400
www.parker.com/faf
© 2013 Parker Hannifin Corporation. Product names are trademarks or registered trademarks of their respective companies.
MAN-DTX1
Worldwide Filtration Manufacturing Locations