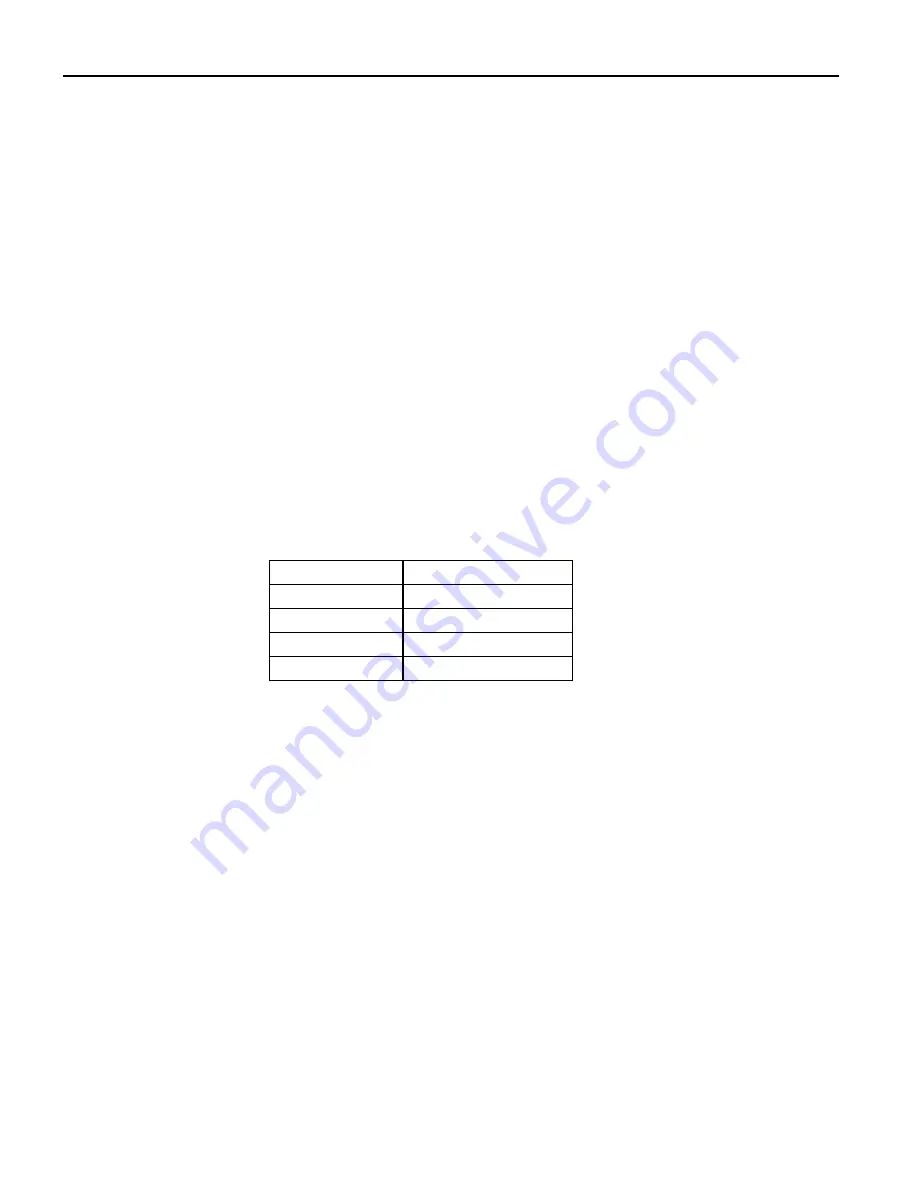
30
BD SERVO DRIVES USER GUIDE
For a single deceleration in current limit, the maximum system inertia which may be braked from
the maximum speed (approximately 55 rps) is 125 kg cm
2
, without any danger of blowing the
dump fuse.
Radial Loads
The ‘Bearing load data’ graph shown above, provides an estimate of the maximum radial load
that can be tolerated at a particular motor speed, when set against the bearing life of a system.
For example, if a typical bearing life expectancy of 20,000 hours was chosen as being
reasonable for a system operating at a speed of 2000rpm, the maximum radial load that could be
tolerated is 550N.
Fuses
BD drives are fitted with fuses which limit circuit damage in the event of a fault occurring, they
are not user replaceable. If the drive fails to operate correctly or you suspect a fuse has blown
return the drive for repair. See
Returning The System in the Maintenance and
Troubleshooting section. Warranty is void if the case is opened.
Cable Sets
Ready-made cable pairs are available in the following lengths:
Part No.
Cable length
BDC-10
3m (10ft)
BDC-25
7.5m (25ft)
BDC-50
15m (50ft)
BDC-100
30m (100ft)
Table 4-3. Cable Sets
Encoders
The BDE1024/6 is a 1024 line, 6 pole self-contained encoder that can be used with motors from
other suppliers.
Summary of Contents for BD-E Series
Page 6: ...ii BD SERVO DRIVES USER GUIDE...
Page 31: ...SECTION 3 INSTALLATION 25...
Page 32: ......
Page 46: ...40 BD SERVO DRIVES USER GUIDE...