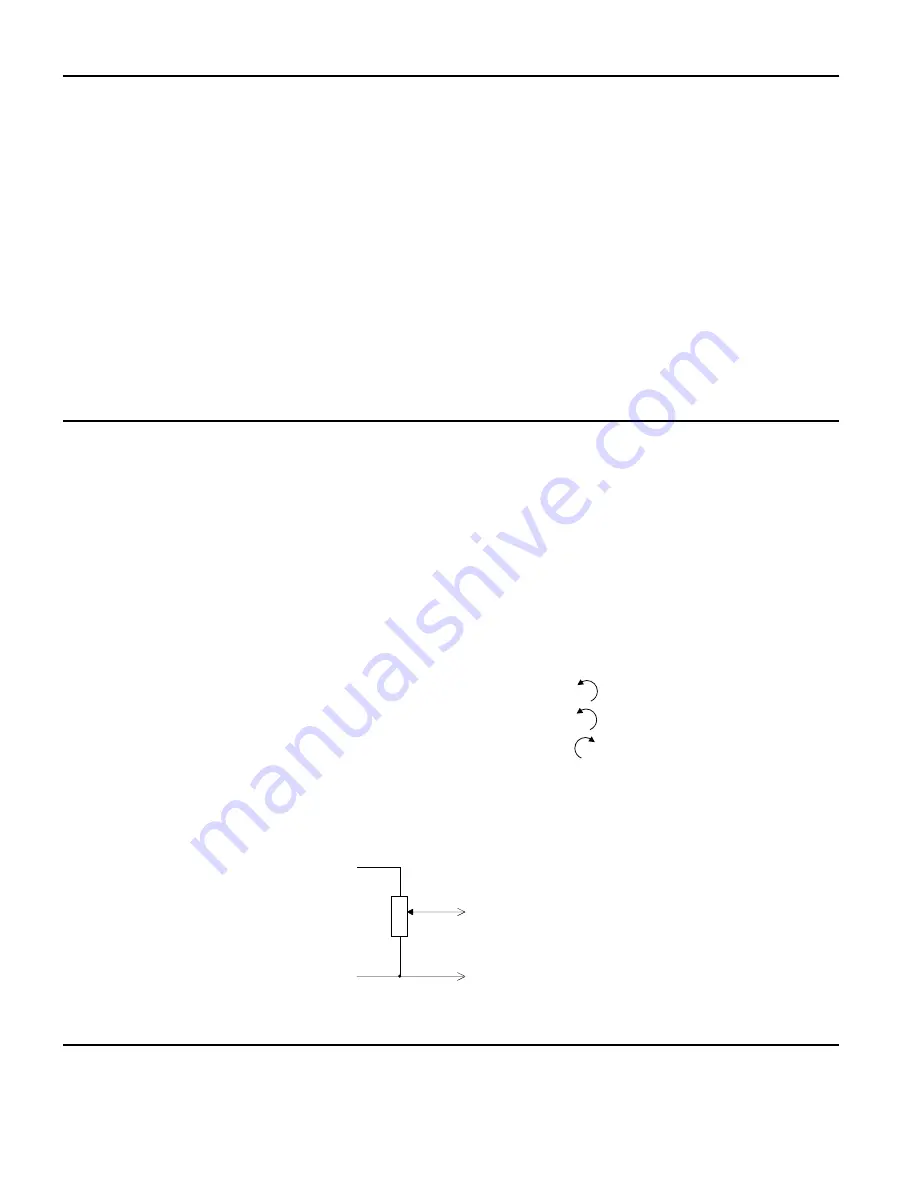
24
BD SERVO DRIVES USER GUIDE
Step 9 -
Increase the input signal to run the motor at high speed (not full speed) and check for
smooth behaviour. If there is excessive noise or vibration, try turning the Time Constant control
anti-clockwise.
Step 10 -
Periodically apply and remove short 20% velocity input signal pulses at approximately 1-
second intervals. If the control system will not permit this method of control, remove the signal
connections and use a separate DC power source (i.e., a battery or a DC power supply) to
provide the signal.
The object is to observe the motor response to each input pulse, using an oscilloscope attached
to the Tach monitor output. The optimum response will be slightly damped with no "ringing" of
the waveform.
Step 11 -
Remove the input signal and ground VEL1 and VEL2 to each other, and, if necessary,
readjust the Balance control until the shaft remains stationary.
Setting up the Drive as a Torque Amplifier
Use the following procedure to tune the drive.
Step 1 -
Set bit switches. Bit switch 5 ON.
Step 2 -
Make sure the power to the drive is off and that the motor is held securely and the shaft is
free to rotate.
Step 3 -
Adjust the front panel controls as follows:
TIME CONSTANT Fully CW
DAMPING Fully CCW
TACH GAIN Fully CCW
In some torque amp applications it is necessary to set an accurate torque amp gain (i.e.
Amps/Volt or Nm/Volt). This can be achieved using an external potentiometer introduced
between the V1 and V2 inputs of the drive, as shown in Figure 3-6.
V1
V2
V1 Drive input
V2 Drive input
Figure 3-6. Circuit for accurate torque amp gain setting
Summary of Contents for BD-E Series
Page 6: ...ii BD SERVO DRIVES USER GUIDE...
Page 31: ...SECTION 3 INSTALLATION 25...
Page 32: ......
Page 46: ...40 BD SERVO DRIVES USER GUIDE...