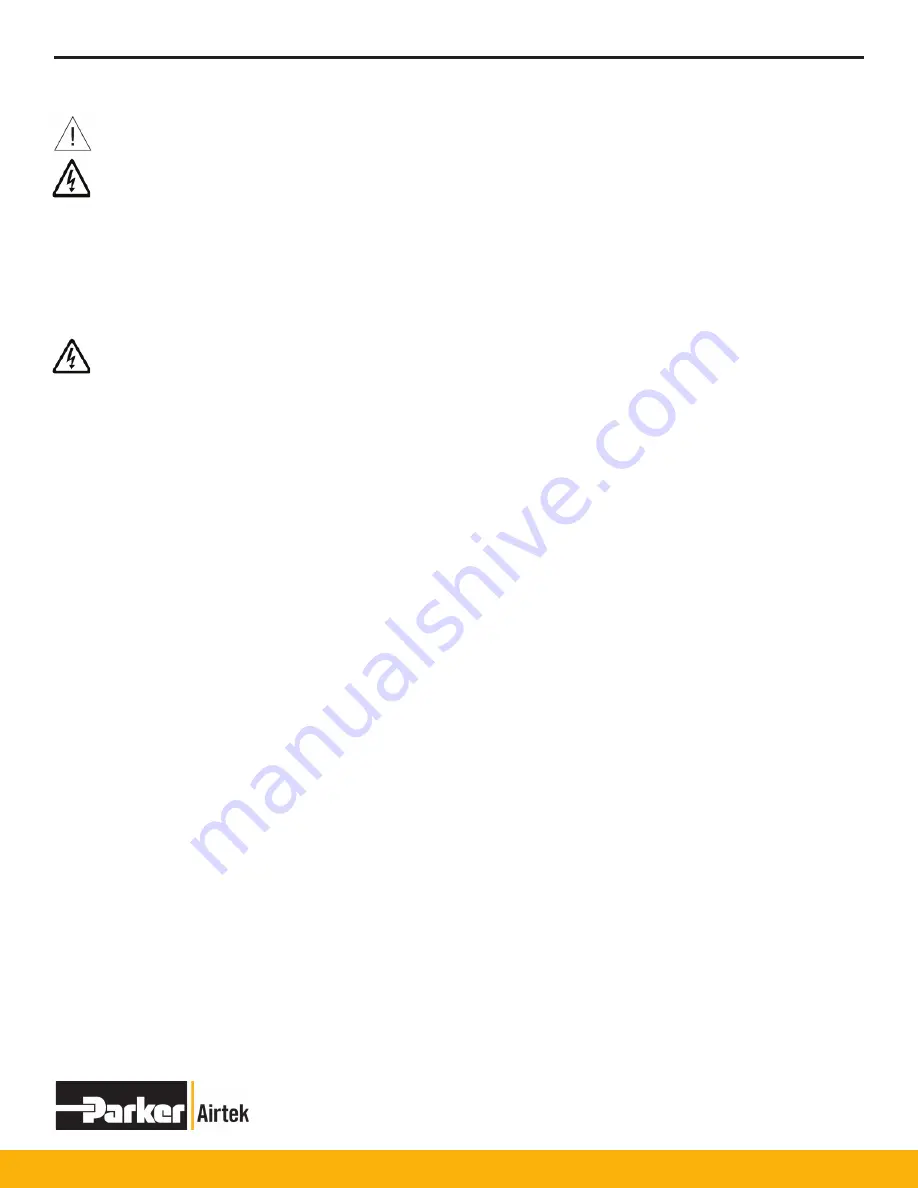
TWP/TWB200 – TWP/TWB9000
4
SAFETY AND PRECAUTIONS
Use EXTREME CAUTION when working in the vicinity of the dryer. Adhere to all warning labels on dryer.
Relieve pressure before servicing dryer or associated equipment.
Disconnect power before servicing dryer.
Always wear eye protection when in the vicinity of the dryer. Ear protection is recommended, especially if the dryer is
being operated without mufflers. Even when mufflers are used, a desiccant vessel blowing down to atmosphere will
raise particles, create more noise than during “normal” operation and may startle an individual not familiar with this
portion of the operation.
The dryer is uses heat to regenerate the desiccant. Any dryer surface may reach temperatures up to 350°F. Do not
touch hot surfaces. Partial insulation is provided to maximize dryer performance. The standard insulation does not
provide complete personnel protection or 100% thermal efficiency.
The emergency stop button will cut off 120V control voltage only. Supply voltage is not disconnected.
In the case of an overpressure situation there is a safety relief valve installed on each desiccant vessel designed to
protect the equipment. If the valves are pointed in a hazardous location to operators after dryer installation, they
should be piped to a safe location.
Dryers are designed for fail safe operation. In the event of a power failure, the inlet valves will fail in the open or last
position and the exhaust valves will fail closed. Compressed air will continue to flow through the dryer. When power
is restored, the cycle will continue on from where it left off at the time of the power loss.
Automatic or manual drain valves will eject water, oil, particulates, and air under partial pressure when operated.
Proper precautions must be taken.
Condensate drainage from compressed air systems may contain oil or other contaminants. Follow all applicable
regulations for safe handling and disposal.
Various component failures could cause large air loss and subsequent pressure drop. Preventative maintenance
should be performed to reduce this possibility. If this situation occurs, bypass the dryer immediately to restore
flow and pressure.
Oil in the desiccant bed combined with high regeneration temperature may create a potential for fire or
explosion. Proper cooling, pre-filtration, and condensate drainage must be maintained to reduce the possibility
of oil contamination.
Activated alumina dust is considered a nuisance dust. Proper precautions should be taken when handling desiccant.
For more information and for other types of desiccant, refer to the applicable Safety Data Sheet. For disposal of
used desiccant, refer to the local codes and regulations.
NOTE:
desiccant contaminated with oil or other foreign substances may be covered under disposal regulations for
the contaminant.
Heated dryers are designed with a cooling cycle after heated regeneration to alleviate high temperatures from the
regenerated desiccant and vessel. It is normal for residual heat to remain in the regenerated vessel. Temperatures
of 200-350°F may be seen at switchover. The residual heat will dissipate quickly once the tower is online at full flow.
Downstream piping and components must be suitable for the elevated temperatures.
DOWNSTREAM AIR TEMPERATURE MAY EXCEED 200°F FOR A DURATION OF 15 MINUTES AFTER DRYING
VESSEL SWITCHOVER! TEMPERATURE CAN EXCEED 350°F AT LOWER FLOW!
Summary of Contents for Airtek TWP200
Page 1: ...1 Externally Heated Blower Purge Desiccant Dryers User Manual Models TWP TWB200 TWP TWB9000...
Page 9: ...TWP TWB200 TWP TWB9000 9 TWP Desiccant Dryer Operation TWB Desiccant Dryer Operation...
Page 10: ...TWP TWB200 TWP TWB9000 10 FLOW SCHEMATIC MODELS TWP200 300 DWG FS11682 Rev...
Page 11: ...TWP TWB200 TWP TWB9000 11 FLOW SCHEMATIC MODELS TWP400 800 DWG FS11683 Rev...
Page 12: ...TWP TWB200 TWP TWB9000 12 FLOW SCHEMATIC MODELS TWP1000 1500 DWG FS11684 Rev...
Page 13: ...TWP TWB200 TWP TWB9000 13 FLOW SCHEMATIC MODELS TWP2000 9000 DWG FS11685 Rev...
Page 14: ...TWP TWB200 TWP TWB9000 14 FLOW SCHEMATIC MODELS TWB200 800 DWG FS11686 Rev...
Page 15: ...TWP TWB200 TWP TWB9000 15 FLOW SCHEMATIC MODELS TWB1000 1500 DWG FS11687 Rev...
Page 16: ...TWP TWB200 TWP TWB9000 16 FLOW SCHEMATIC MODELS TWB2000 9000 DWG FS11688 Rev...
Page 17: ...TWP TWB200 TWP TWB9000 17 WIRING DIAGRAM STANDARD CONTROLLER...
Page 18: ...TWP TWB200 TWP TWB9000 18 WIRING DIAGRAM STANDARD CONTROLLER...
Page 19: ...TWP TWB200 TWP TWB9000 19 WIRING DIAGRAM STANDARD CONTROLLER...
Page 20: ...TWP TWB200 TWP TWB9000 20 WIRING DIAGRAM STANDARD CONTROLLER...
Page 21: ...TWP TWB200 TWP TWB9000 21 PANEL LAYOUT STANDARD CONTROLLER...
Page 38: ...TWP TWB200 TWP TWB9000 38 Service Screen...
Page 71: ...TWP TWB200 TWP TWB9000 71...