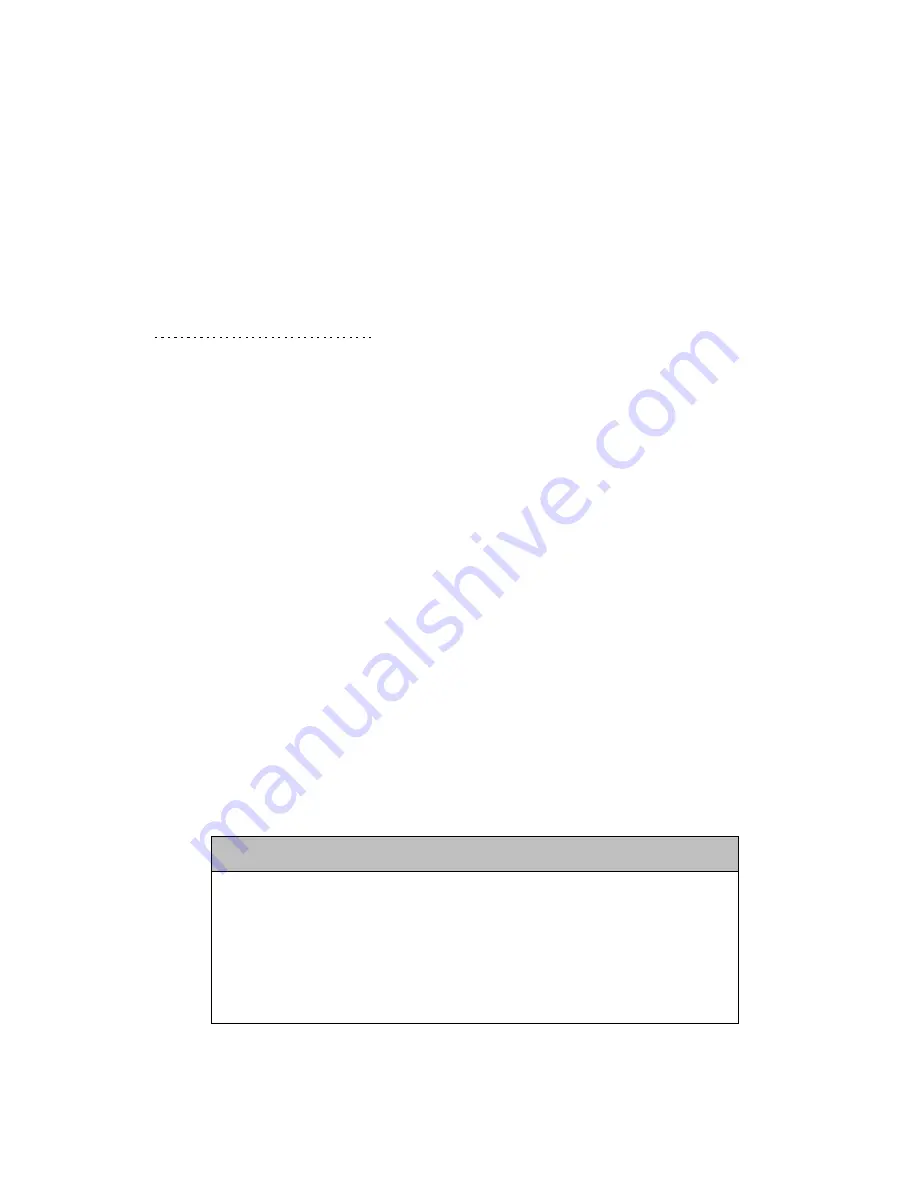
1
C H A P T E R O N E
Installation
IN THIS CHAPTER
•
Things to consider before you install your 6K controller .............................. 2
•
Product ship kit list........................................................................................ 3
•
General specifications table ........................................................................... 4
•
Dimensions and mounting guidelines............................................................ 6
•
Connecting all electrical components (includes specifications)..................... 8
•
Testing the installation................................................................................... 30
•
Preparing for what to do next ........................................................................ 31