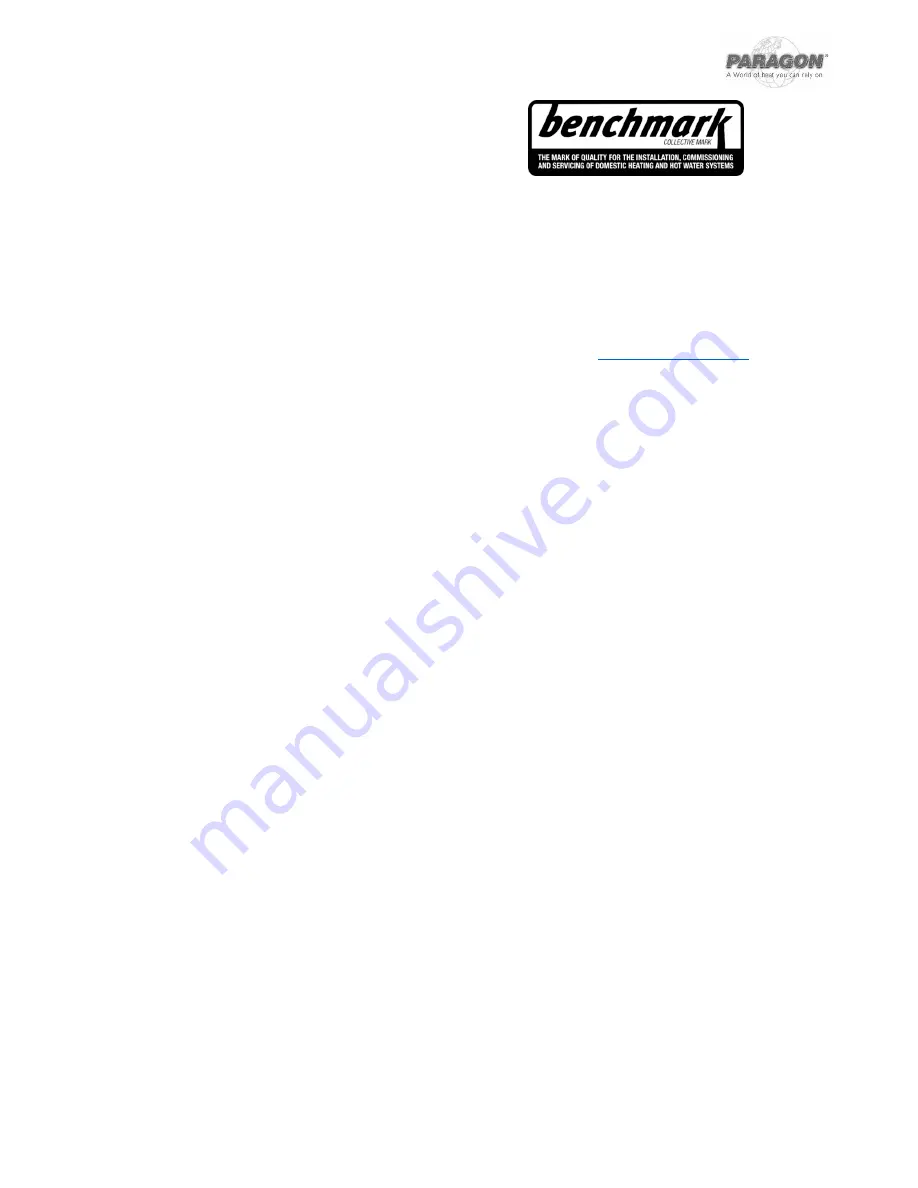
www.charltonandjenrick.co.uk
3
LT5674 (ISS 5)
Benchmark Scheme
Charlton and Jenrick Ltd is a licensed member of the Benchmark Scheme which aims to improve the standards of
installation and commissioning of domestic heating and hot water systems in the UK and to encourage regular servicing
to optimise safety, efficiency and performance. Benchmark is managed and promoted by the Heating and Hotwater
Industry Council. For more information and the full code of practice please visit
www.centralheating.co.uk
Please ensure that the installer has fully completed the Benchmark Checklist on the inside back pages of the installation
instructions supplied with the product and that you have signed it to say that you have received a full and clear
explanation of its operation. The installer is legally required to complete a commissioning checklist as a means of
complying with the appropriate Building Regulations (England and Wales).
All installations must be notified to Local Area Building Control either directly or through a Competent Persons Scheme.
A Building Regulations Compliance Certificate will then be issued to the customer who should, on receipt, write the
Notification Number on the Benchmark Checklist.
This product should be serviced regularly to optimise its safety, efficiency and performance. The service engineer
should complete the relevant Service Record on the Benchmark Checklist after each service.
The Benchmark Checklist will be required in the event of any warranty.
It is a requirement that the gas fire is installed and commissioned to the manufacturer’s instructions and the data fields
on the commissioning checklist completed in full.
To instigate the guarantee, the gas fire needs to be registered with the manufacturer within one month of the
installation.
To maintain the guarantee, it is essential that the gas fire is serviced annually by a Gas Safe registered engineer. The
service details should be recorded on the Benchmark Service Interval Record and left with the householder.